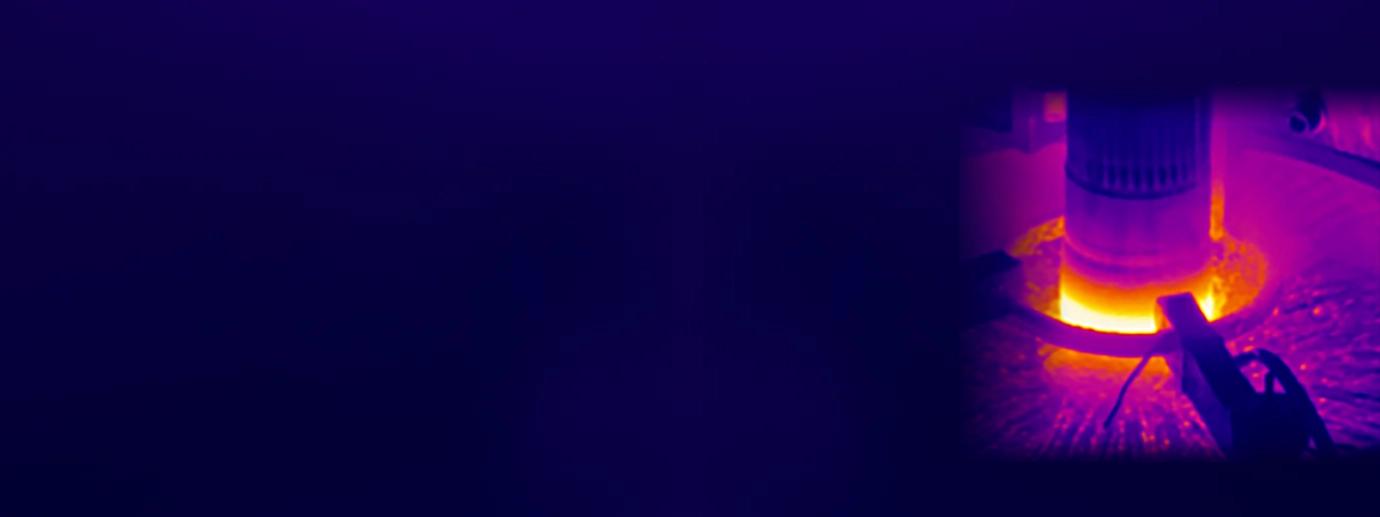
Induction Soldering Requires Precise Temperature Control
Advantages of Using Ratio Pyrometers for Accurate Temperature Measurement in Induction Heating Processes
Induction Soldering requires Precise Temperature Control
Induction soldering joins two conductive materials using a filler metal that melts at a low temperature, distinguishing it from brazing, which occurs at higher temperatures. Induction generates an electromagnetic field in a work coil, inducing currents in the conductive material of the workpiece, which elevates the temperature of the workpieces and filler for soldering.
Induction soldering delivers precise, localized heat, increasing production rates with faster heating cycles and reducing defect rates through repeatable, reliable heating while maintaining the metallurgical characteristics of the metals. This process is accomplished without an open flame. Although the joint may be slightly weaker than a brazed one, induction heating is ideal for sensitive electronics or small components as it controls the soldering process and avoids thermal stress.
The principle of inductive heating can be understood as a simple process. The inductor acts as a primary transformer, and the workpiece as a secondary short circuit. When a metal part enters the electromagnetic field, it heats up due to induced circulating eddy currents.
Precise temperature control is crucial in induction soldering. Even slight fluctuations can cause incomplete or defective solder joints. High thermal conductivity materials can dissipate heat quickly, complicating uniform temperature rise. Excessive temperatures can damage materials, so the soldering temperature must match the thermal stability of all materials involved. Additionally, exposure to high temperatures must be optimized; a short duration can result in complete melting, while too long can overheat and damage the component. Thermocouples can be a reliable and cost-effective choice for temperature measurement, though their placement must be carefully considered due to potential electromagnetic field interference.
Industrial induction soldering systems require a more automated feedback system, incorporating input from temperature sensors, to adjust and optimize the process in real-time.
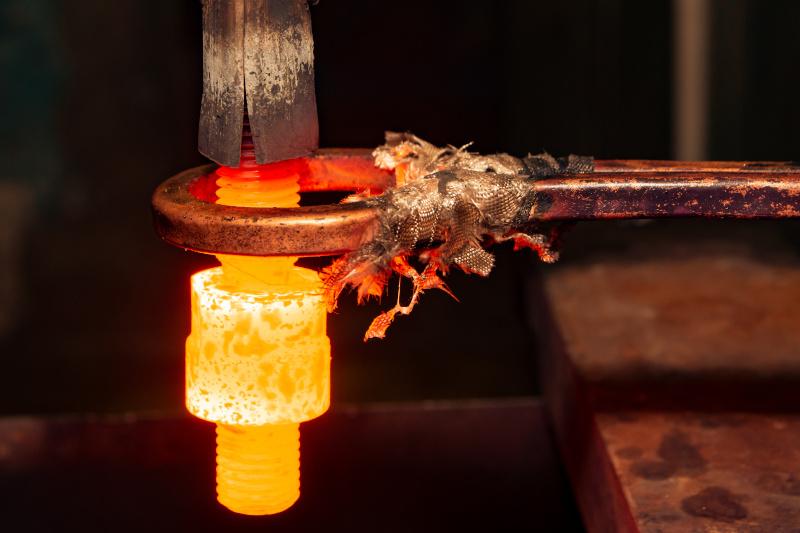
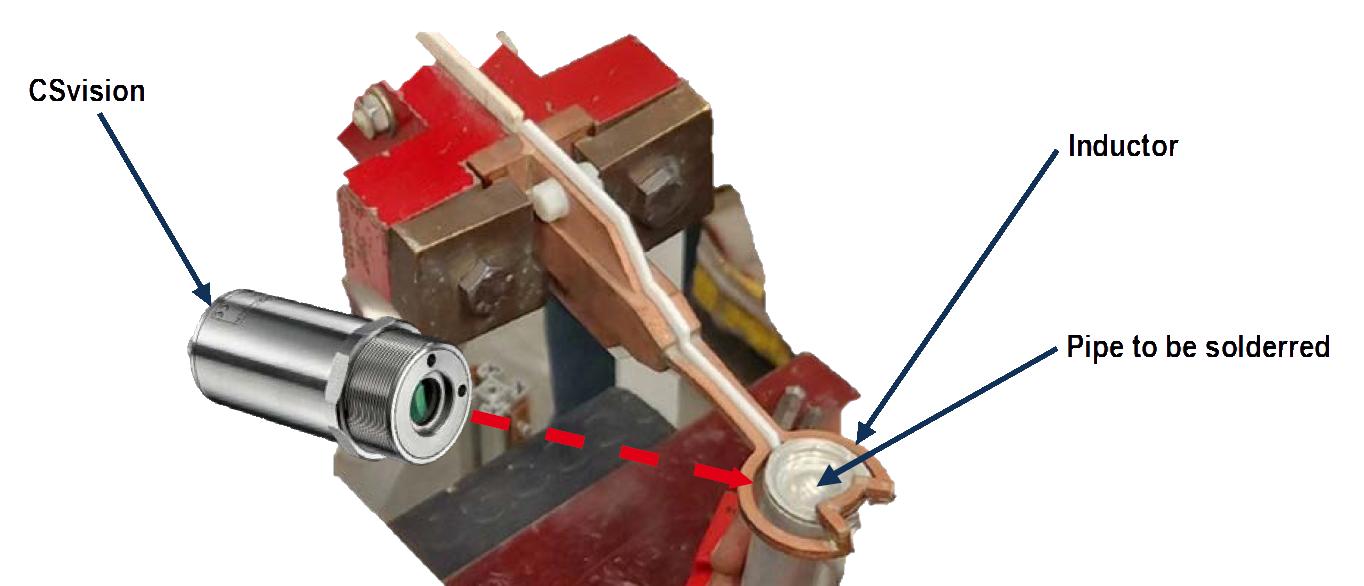
Advantages of Using Ratio Pyrometers for Accurate Temperature Measurement in Induction Soldering
The CSvision, a ratio pyrometer, also known as a two-color pyrometer, measures temperature based on the ratio of infrared radiation at two different wavelengths. Reflective and shiny surfaces, common in metals used in soldering, can pose challenges for single-wavelength pyrometers. Unlike single-color pyrometers, which rely solely on intensity measurements, the CSvision utilizes a ratio-based approach, measuring infrared radiation at two closely spaced wavelengths. This method provides unparalleled accuracy, particularly as temperatures rise and an object’s emitted radiation increases across the wavelength range.
Optris ratio pyrometers, such as the CSvision, are highly reliable for measuring temperatures in environments where the target’s emissivity might change during the process. Ratio pyrometers are better suited for these conditions as they can minimize the effects of reflections and provide more accurate readings. The Optris CSvision can be aimed at very small areas of interest.
The CSvision series’ innovative video sighting and crosshair laser make aligning the sensor easy. This provides a real image of where the pyrometer is spotting, and even the spot size is indicated by the image. The brightness reduction filter damps the very bright emitted light from the soldering so that controlled placement of the soldering is monitored.
The CSvision also features motorized focus capability, allowing for adjustable focusing from 350mm to infinity in the standard focus version and from 200mm to 400mm in the close focus version.
CSvision Ratio Pyrometers are the best Instrument to Monitor Induction Heating Processes
The Optris CSvision ratio pyrometers offer several advantages that make them well-suited for inductive soldering applications. They provide accurate temperature measurements even when emissivity changes. The two-color pyrometer allows for reliable readings in the challenging environment of inductive soldering, where contaminants and reflective surfaces can pose significant measurement challenges. It offers a high distance-to-spot size ratio and low thermal resolution. With the ability to tolerate up to 90% attenuation and still detect the correct temperature, the CSvision ensures accurate results even under partial obstructions.
The pyrometers cover a wide temperature range from 250 °C to 3000 °C, offering exceptional versatility and high precision. Real-time monitoring is enabled by their fast response times of up to 1 ms, allowing for immediate adjustments and control during the soldering process. The integrated video sighting and crosshair laser make aligning the sensor straightforward, while the brightness reduction filter helps manage the intense light emitted during soldering, ensuring controlled and accurate placement. These features collectively ensure that ratio pyrometers deliver reliable and consistent temperature measurements, which are critical for maintaining the quality and integrity of solder joints in inductive soldering processes. These advanced capabilities make the Optris CSvision an indispensable tool for achieving optimal results in complex soldering environments.
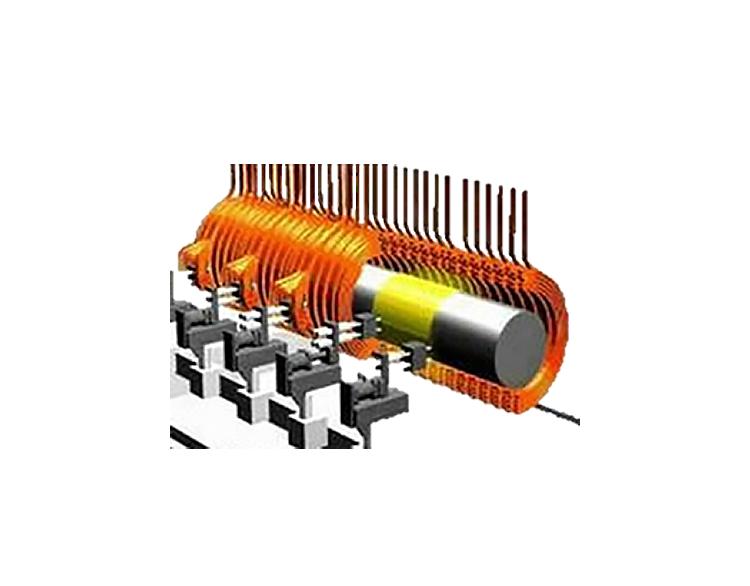
Recommended Products
Other Metal Applications
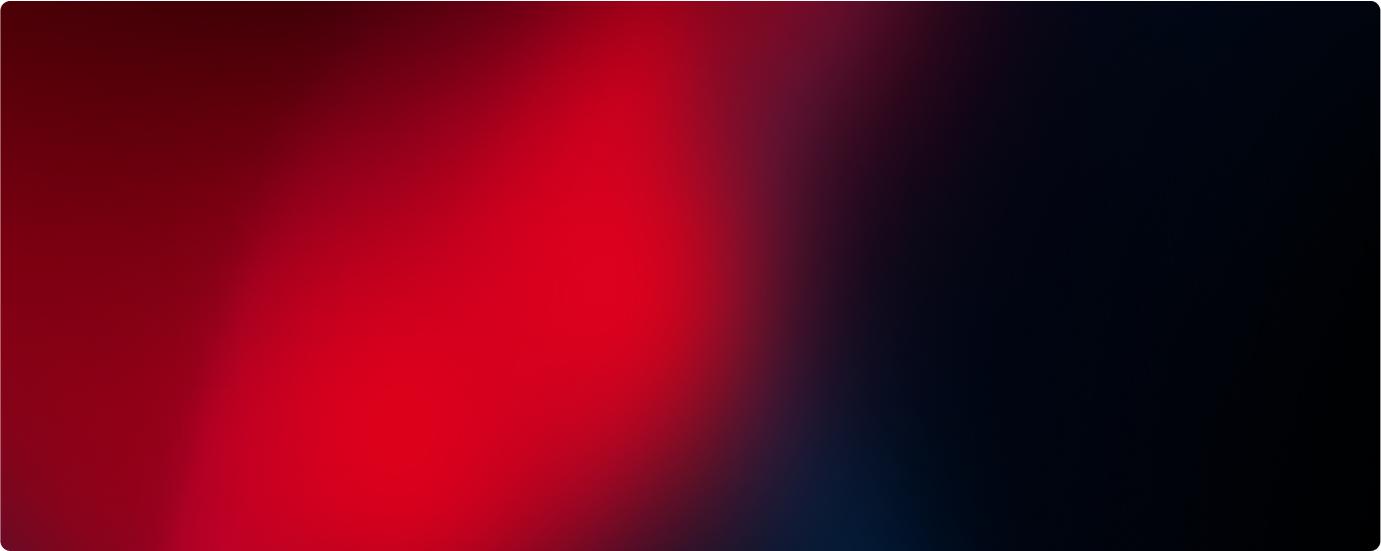
Talk to us about your IR Temperature Measurement Requirements
There are over 300 different pyrometer variants to choose from in the Optris infrared pyrometer portfolio each optimized for material, spot size, distance from the target, and environmental conditions. Fortunately, there is a trained engineer to phone or chat with to guide you through the process of choosing the perfect infrared sensor for your application.
The same support is available for the extensive IR camera product line.
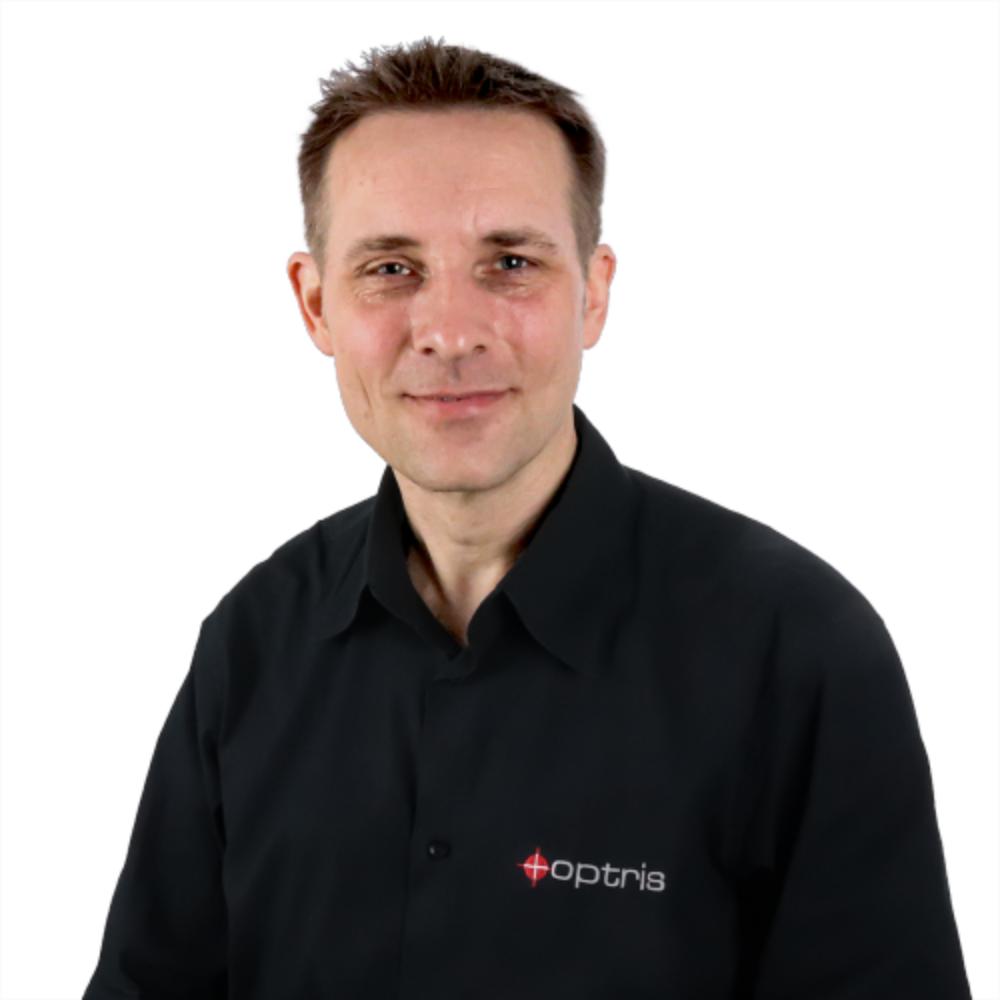