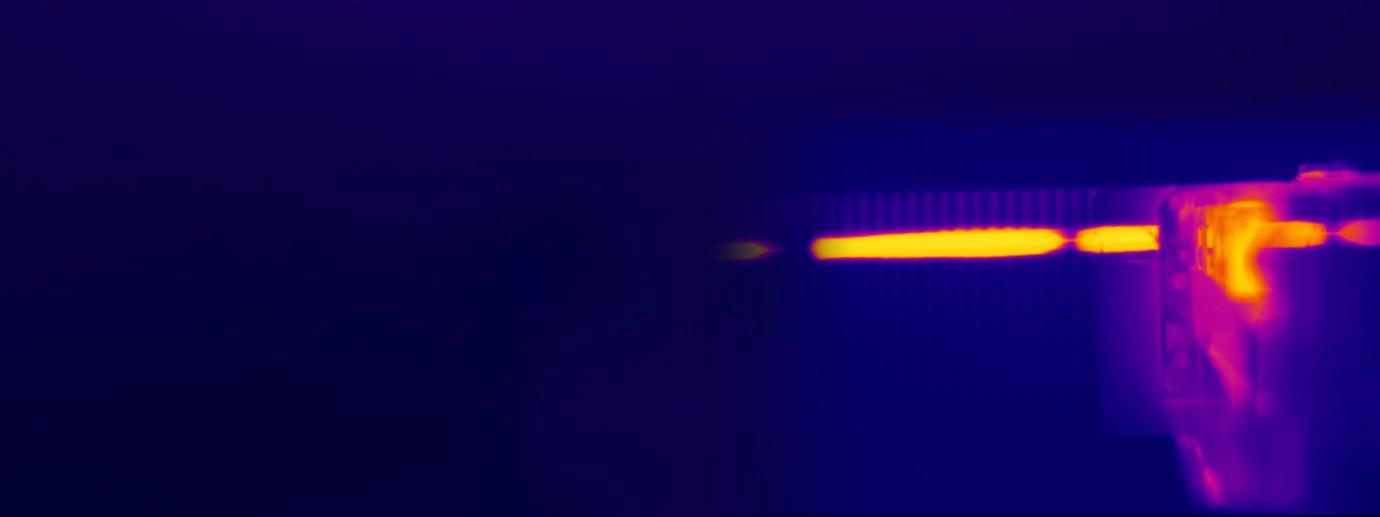
Adhesive Application and Bonding Quality Control
Inconsistent application of Adhesive on plastic part
An engineering firm that makes custom automation equipment for clients in many industries needs to produce a system for applying adhesive beads onto ribbed plastic sheets. Adhesive application has been inconsistent, and the client needs a consistent application of adhesive to maintain quality on the finished part which is a sandwich of two plastic sheets. Plastic sheets 3 feet long are ejected from the adhesive application system every three seconds. The adhesive bead is roughly 170 °C (340 °F). The area immediately adjacent to the adhesive bead is 25 °C (77 °F) and varies with the ambient temperature in the manufacturing facility.
Both the adhesive and the plastic part have very high emissivity and are perfect targets for infrared imaging and temperature measurement. The size and location of the plastic bead are easy to detect and measure with a long-wavelength infrared camera. The quality of the adhesive application correlates directly with the area covered on the plastic part. The client customer has used handheld infrared cameras with some success but the manual process of checking for adequate and consistent adhesive application is insufficiently quantitative.
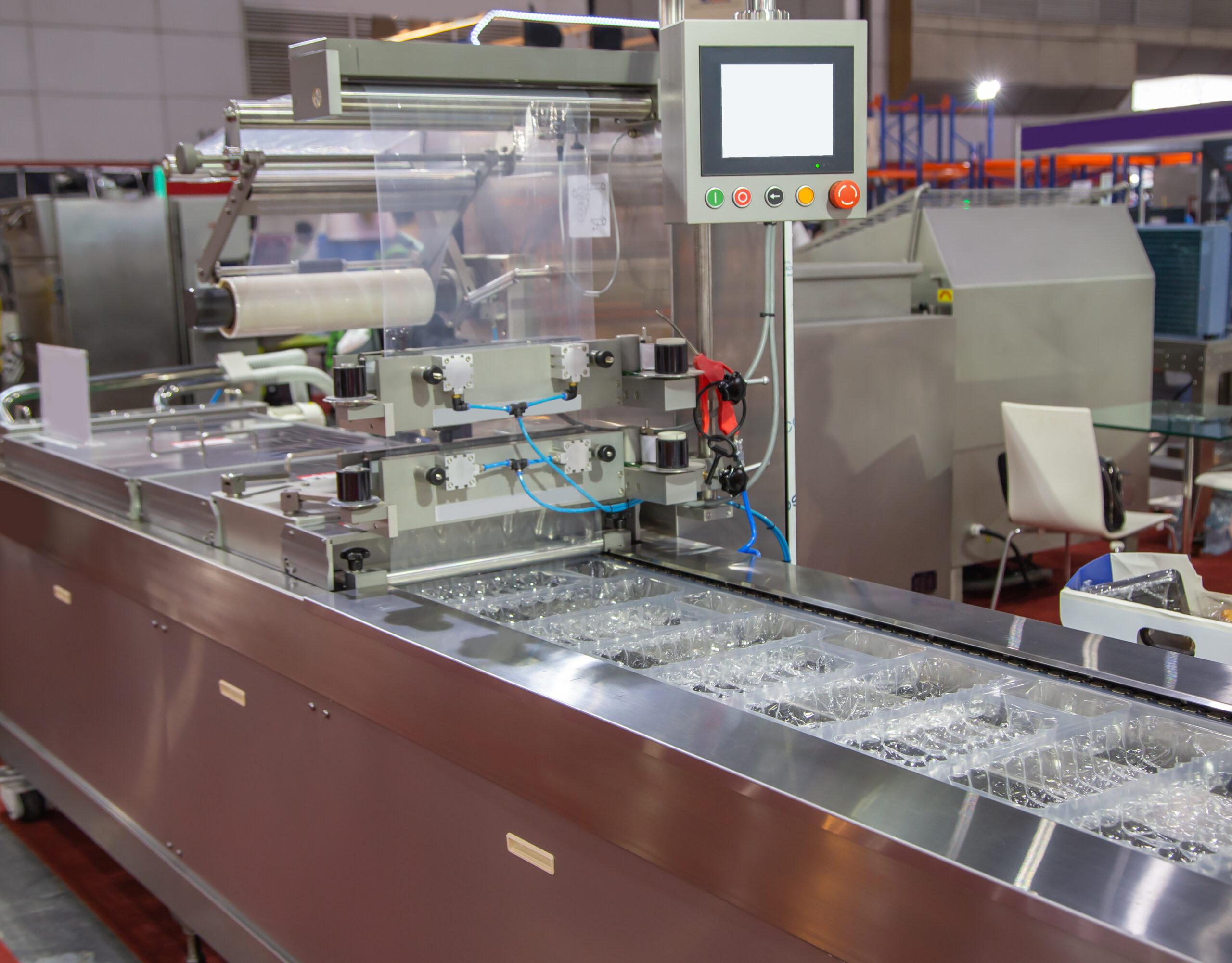
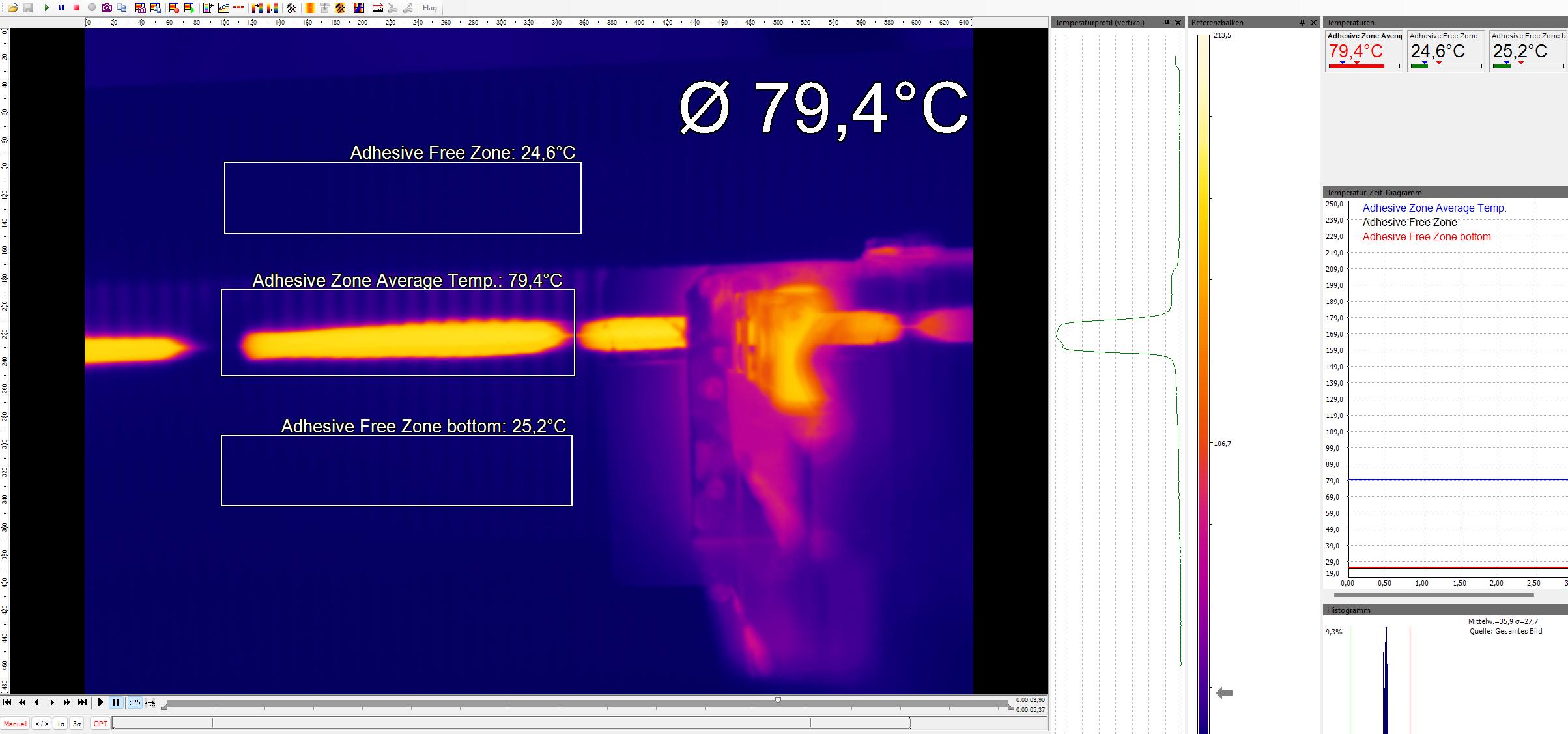
Long wavelength infrared camera PI 640i with PIX Connect software
To compare adhesive applications throughout the day, the best approach is to use a fixed infrared camera looking at the same area on the part at precisely the same time after part ejection. Measuring the precise physical area of adhesive on the part would require substantial custom programming which is not necessary in order to determine adequate application. Instead, it is determined that a specific area on the part (Adhesive Zone 1) can be measured which would include both the adhesive bead and the ambient temperatures immediately surrounding the bead. The temperature measured will be the average temperature of all of the pixels in the measurement area.
This average temperature can be used to determine adequate adhesive application provided the camera freezes and stores each image at the same time after ejection, and the size of the area measured is consistent. An average temperature representing an adequate bead application is determined through testing. In the image above, 190 °F is determined to be an adequate average temperature for a properly sized bead. If the adhesive bead is smaller than the acceptable size, the average temperature in the area will be lower than 190 °F and can be set to trigger an alarm. The Event Grabber feature in PIX Connect software will freeze an image when input from a thru-beam photoelectric sensor is received by the Industrial Process Interface. A holdoff time of 1.5 seconds is set to allow ideal timing for capturing the temperature of the Adhesive zone. Many companies require documentation of detected faults and some in the aerospace or defense industries may require documentation on every part so manufacturing parameters can be verified months or years after production.
PIX Connect software can archive fully radiometric thermal images where every pixel value can be measured on a stored radiometric TIFF image file. The images in the application example were captured with a PI 640i (640 x 480) with a 33 optic from 6 feet away which yielded the detailed image quality requested by the client. A mid-range special resolution (320 x 240) would have been adequate to service this application. Parts much larger or smaller can be tested in the same way through changes in optics or working distance. Details on the Optris Industrial Process Interface are available in the accessories section of the Optris website.
Simple temperature related product quality solution with no custom software development saves cost
Many production solutions may require custom software programming to deliver the information necessary to improve product quality in the manufacturing process. However, many solutions can be deployed simply by connecting the infrared camera to a PC equipped with PIX Connect software. Numerous measurement tools can deliver maximum, minimum, or average temperatures from any shape drawn on an infrared image. Triggering capabilities in the software that accept external inputs through the Optris Industrial Process Interface accessory ensure that the temperature measurement is made in the precise location and at the precise time necessary to take temperature data for comparison purposes.
The same Process Interface accessory that receives input triggers also communicates temperature or alarm information to the customer’s PLC through 0/4 – 20 mA or relay signals. The alarm conditions can be easily set in the Alarm tab in the PIX Connect software. Optris support is available for engineers looking for guidance on how to optimize event capture, non-contact temperature measurement, and alarming features in the PIX Connect software.
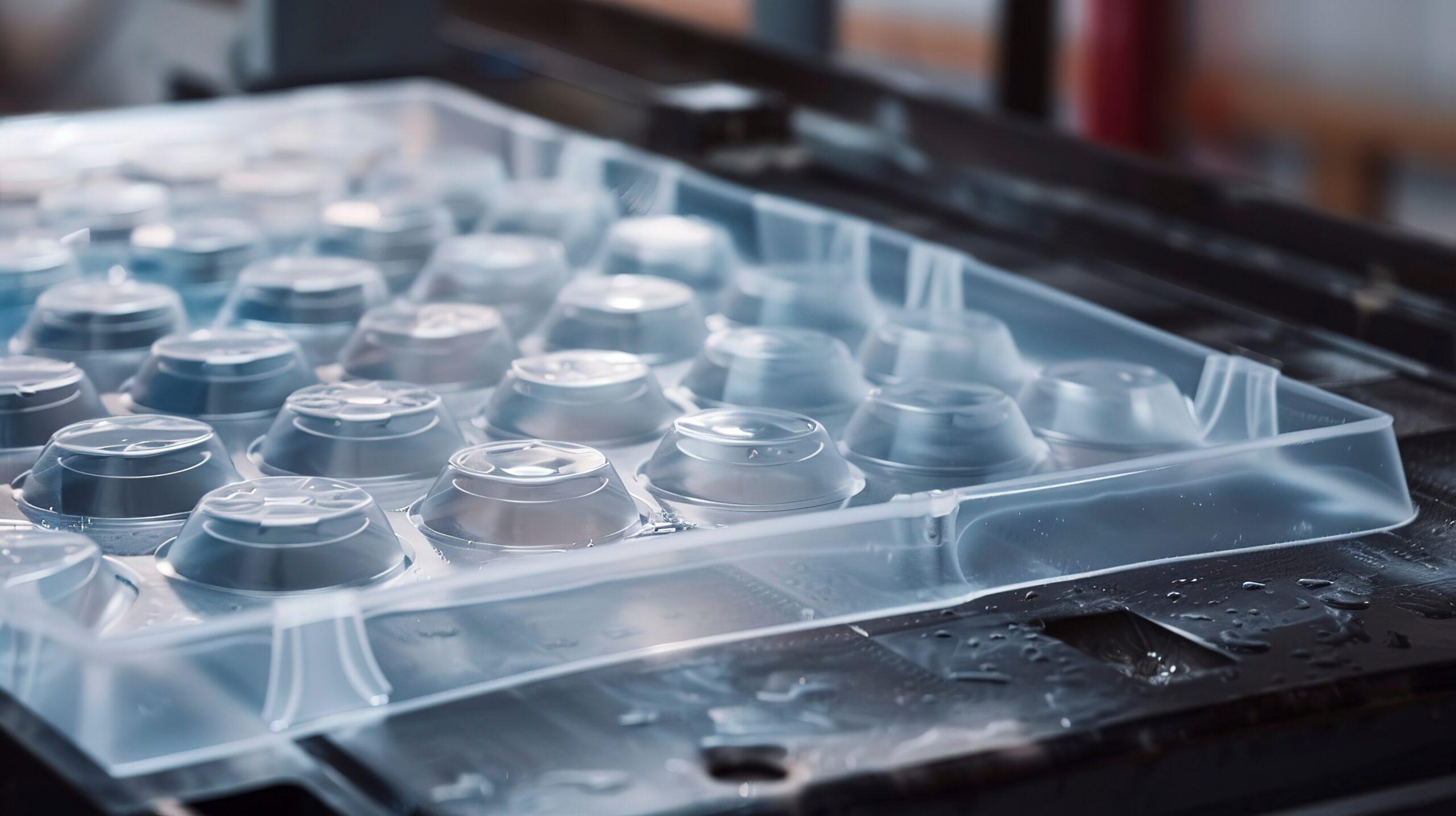
Recommended Products
Downloads
BROCHURE
PDF - 1.46 MB
Non Contact Temperature Measurement in Plastics Industry
Complete the form to download the file
Other Plastic Applications
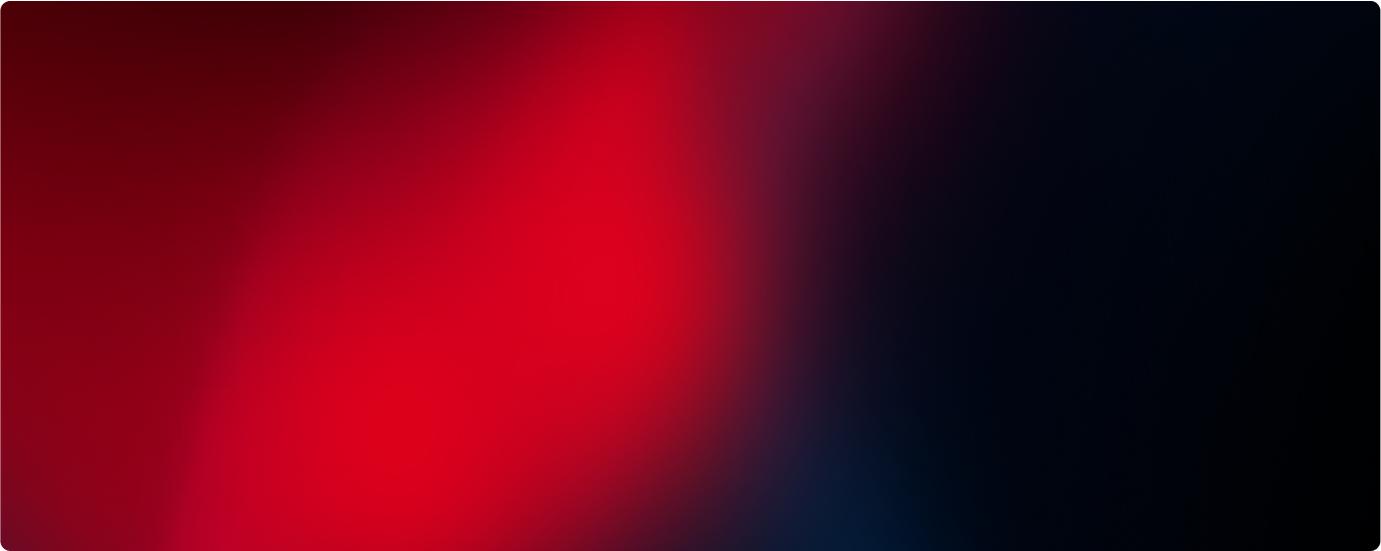
Talk to us about your IR Temperature Measurement Requirements
There are over 300 different pyrometer variants to choose from in the Optris infrared pyrometer portfolio each optimized for material, spot size, distance from the target, and environmental conditions. Fortunately, there is a trained engineer to phone or chat with to guide you through the process of choosing the perfect infrared sensor for your application.
The same support is available for the extensive IR camera product line.
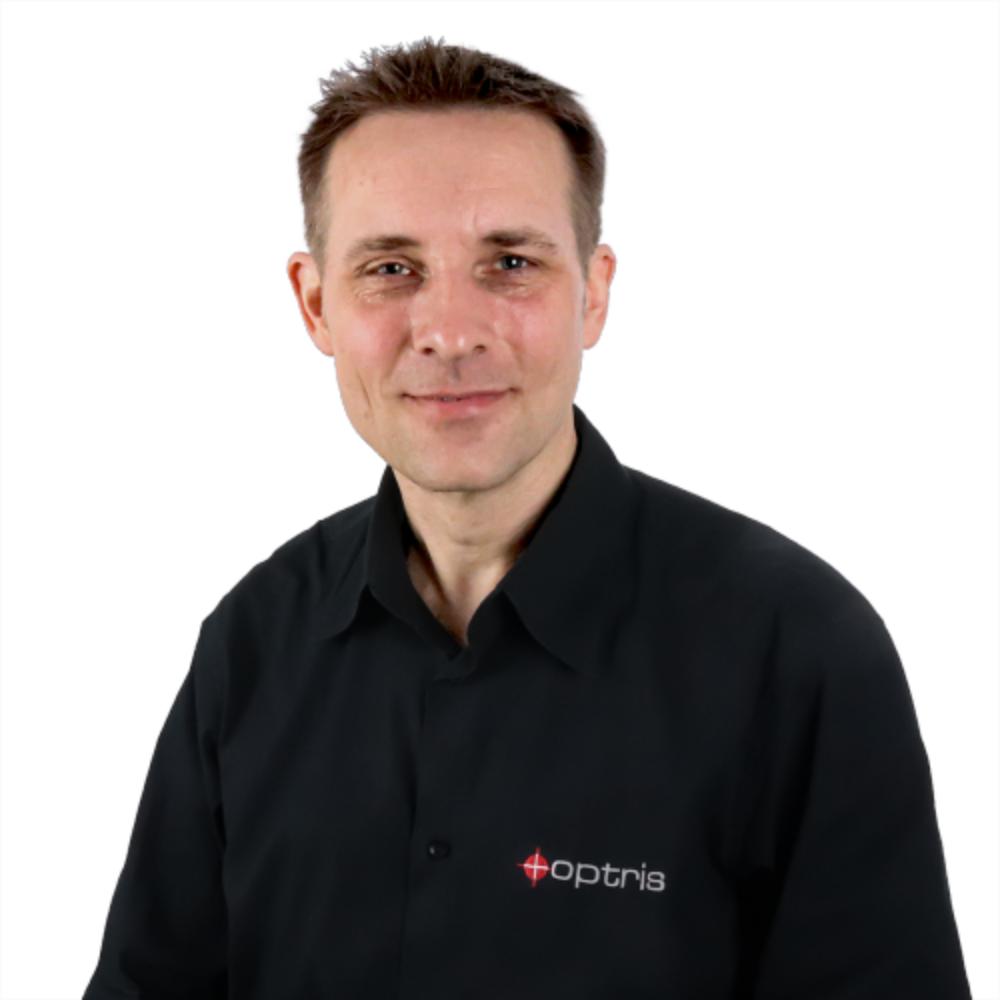