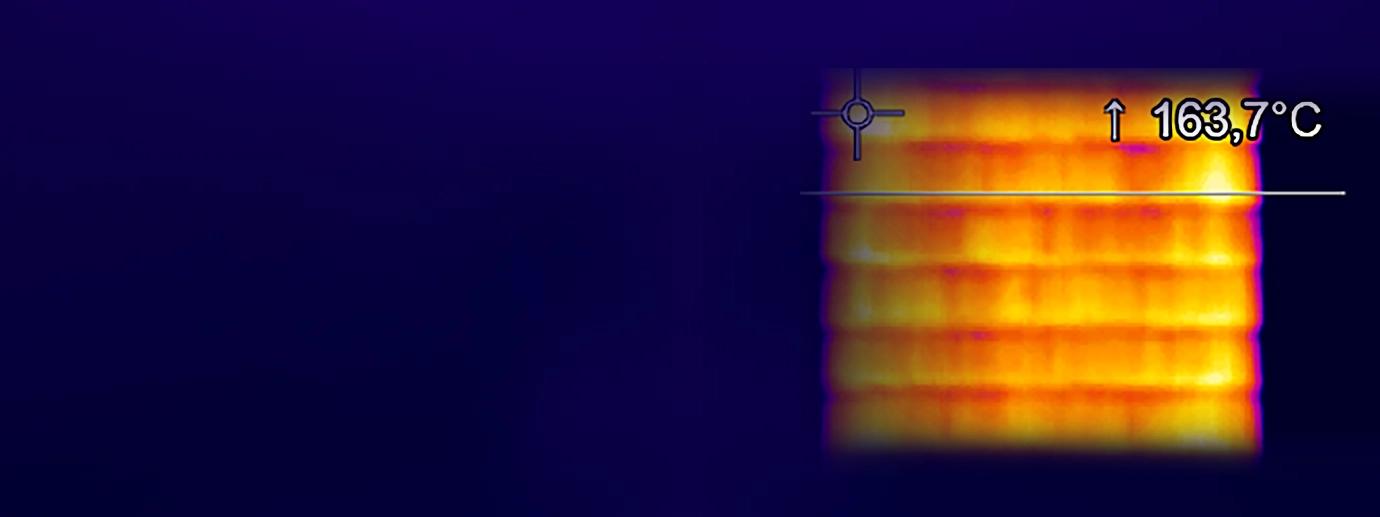
Optimizing Temperature Control of Industrial Infrared Heaters and Dryers
Integrating Compact and High-Temperature-Tolerant Pyrometers into Infrared Heaters for Drying Coatings, Paints, Composites and Plastics
Preventing Overheating and Insufficient Drying of Coating and Paints with Infrared Heaters
An infrared dryer or heater is a heating system for drying water-based paints, coatings, and inks. It is also often used to heat plastic, plastic films, and composites for the next manufacturing step.
It consists of powerful infrared emitters and reflectors that focus the IR radiation on the substrate, accelerating industrial drying processes. Infrared radiators offer several advantages, requiring neither contact nor an intermediate transfer medium. They allow for controllable heat application with fast response times, ensuring precise heat delivery only where and for as long as needed. Compared to hot-air ovens, infrared heating often results in lower energy consumption, higher production speeds, less production space, and superior heating results.
Materials interact with infrared radiation by absorbing some of it, reflecting some on the surface, and allowing some to pass through. The key to successful process heating lies in selecting emitters with a suitable spectrum, ensuring the maximum possible radiation is absorbed by the material and converted into heat. This careful matching of the infrared emitter to the properties of the product in terms of its wavelength, shape, and power output is crucial for successful process heating.
The temperature of the heating element determines the radiation wavelength of an infrared emitter, influencing the heating process. Short-wave radiation can penetrate deeply into some solid materials, ensuring uniform through heating, while medium-wave radiation is absorbed mostly on the outer surface, predominantly heating it. Medium-wave radiation is particularly well-absorbed by many plastics, glass, and especially water, converting directly into heat.
Controlling the infrared radiation emitted by the heater is essential. If the IR heater is positioned too closely and emits too much heat, the drying material can overheat, causing blisters or burns. On the other hand, if the IR heater does not emit enough heat, the material may not dry completely, leading to sagging and an insufficient surface finish. Therefore, it is crucial to maintain the right balance in controlling the infrared radiation for successful process heating.
Using conventional contact-based temperature sensors on dried materials is impractical in industrial, volume-oriented manufacturing processes. Additionally, a bulky contact sensor head will absorb temperature differently than thin film coatings, paints, or inks due to different spectral absorption and higher thermal mass. Therefore, a non-contact temperature sensing method is required.
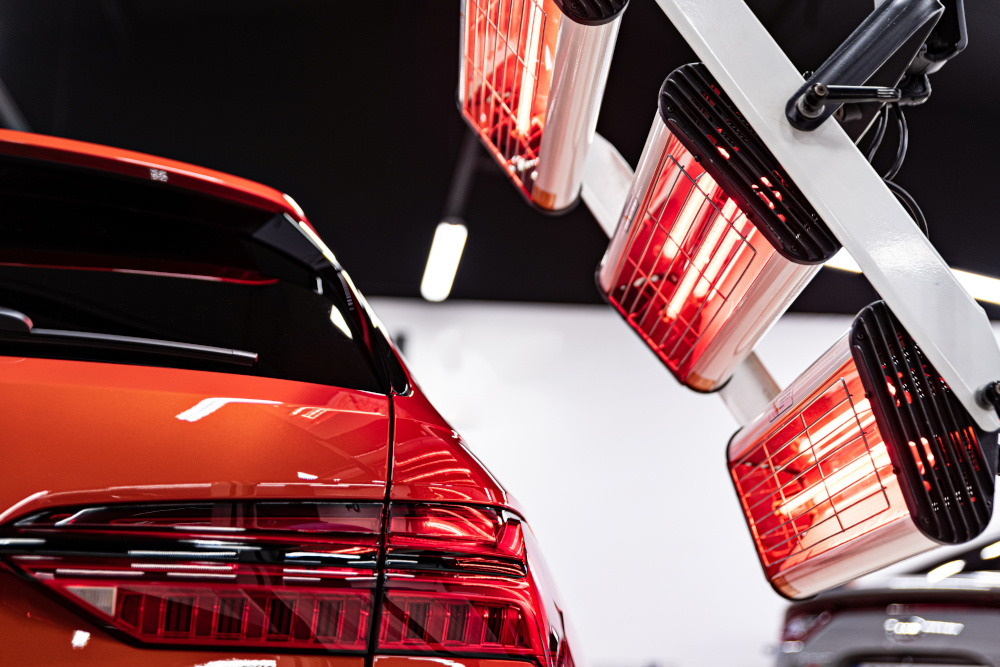
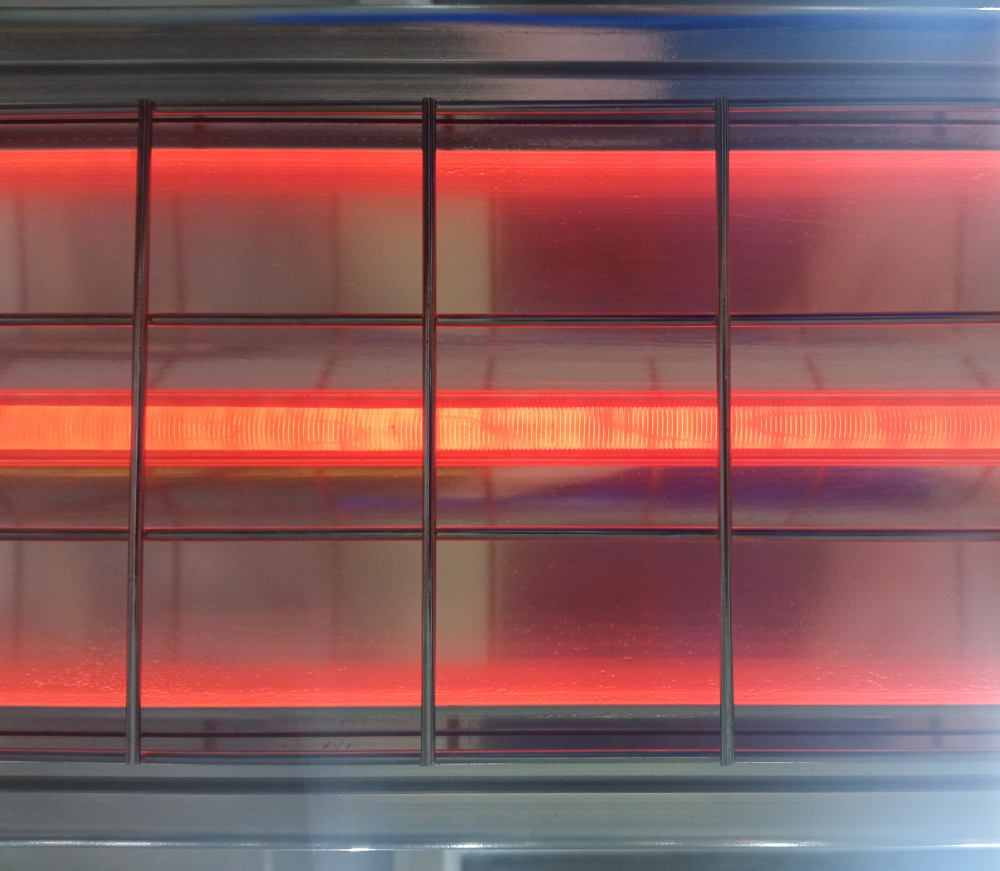
Mitigating Crosstalk between Infrared Heater and Pyrometers by Wavelength Separation
Understanding the condition of the heated surface is pivotal for controlling the heating process. Infrared measurement, the fastest and most direct method, plays a key role in this process. A pyrometer provides the measured temperature directly to the heater control unit, facilitating real-time optimization of energy. This ensures that the right amount of energy is always applied, leading to the best and most efficient results. The infrared sensor, strategically placed in the center of the IR heaters, aligns with the direction of the heat radiation.
One challenge of IR measurement near IR heaters is avoiding measurement in the same spectral range in which the heaters operate. Infrared heaters and dryers typically function within the wavelength bands of near-infrared (NIR) and mid-infrared (MIR). NIR heaters usually work in the range of 0.75 µm to 1.5 µm, providing intense and focused heat ideal for rapid heating applications. MIR heaters operate within the 1.5 µm to 5.0 µm range, offering balanced heating suitable for both surfaces and slightly deeper penetration into materials.
To avoid crosstalk, a pyrometer typically operates in the 8 µm – 14 µm long wavelength (LT) range for most drying and heating applications. This is beneficial because most coating and painting materials have a wide spectral range with high emissivity. If a metallic surface is heat treated with an NIR infrared heater and the material’s emissivity is insufficient for the LT range, a 3M pyrometer with sensitivity at 2.3 µm can be paired with the IR heater. Although it is rare for an infrared heater to emit radiation at the long wavelength range from 8 µm – 14 µm, the same best practice applies: utilize an infrared sensor with a different sensitivity than the IR heater to avoid crosstalk. Here a short-wavelength infrared sensor would be recommended.
Precise Control of Infrared Heaters Requires Compact, High-Temperature-Tolerant Infrared Sensors
Integrating a pyrometer into an infrared heater presents a unique challenge due to the limited space available. The infrared sensor head must be as small as possible to fit within the narrow confines of the heater. Additionally, because the sensor head is installed close to the infrared emitter, it must be capable of withstanding high ambient temperatures. This dual requirement of compactness and high-temperature tolerance is essential for effective integration. Furthermore, the temperature data gathered by the pyrometer must be seamlessly fed into the heater’s controller to ensure precise control and optimization of the heating process. For mass-produced solutions, this signal integration must be both simple and cost-effective to meet the demands of large-scale manufacturing.
The Optris CSmicro addresses these challenges with its exceptionally small sensor head, featuring an M12 thread size that simplifies integration into infrared heaters. This compact sensor head is designed to withstand temperatures up to 180 °C (356 °F), including the cable, without compromising on temperature accuracy or necessitating cooling. The rapid heating of IR dryers makes the sensor’s resistance to temperature shocks particularly valuable, ensuring reliable and accurate temperature data and control.
The temperature data from the Optris CSmicro is transmitted via an analog 4-20 mA signal, providing direct integration with the heater’s control system. However, if a digital interface is preferred or required, the Optris CT series offers a versatile alternative. The CT series retains the same small-sized sensor head but connects to an electronic box that offers flexible signal output options. Users can choose from analog and a variety of digital interfaces, making the system adaptable to different control requirements and preferences.
This combination of small size, high-temperature tolerance, and versatile data output makes the Optris CSmicro and CT series ideal for integration into infrared heaters. They provide reliable, accurate temperature measurement and control, ensuring optimal performance in industrial heating applications.
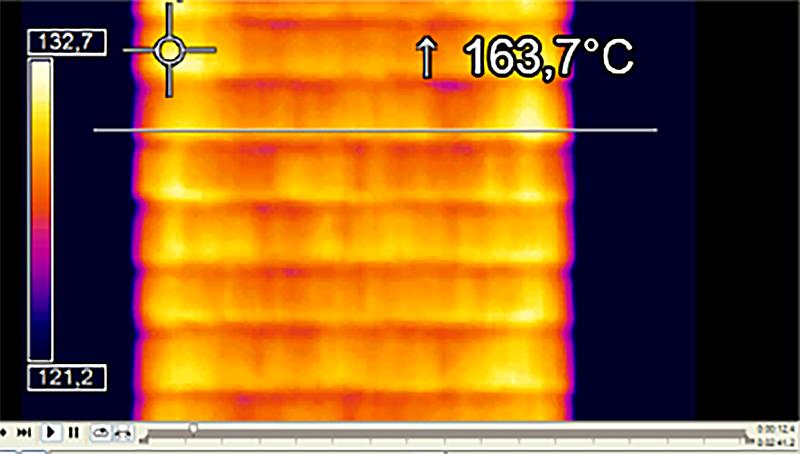
Recommended Products
Other General Manufacturing Applications
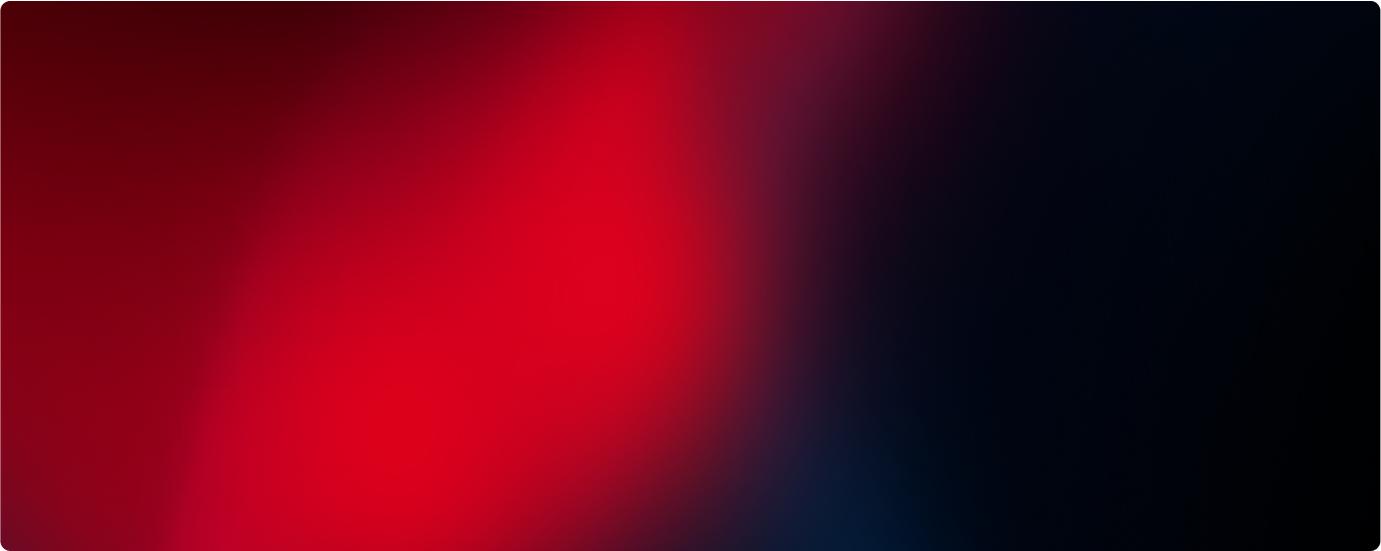
Talk to us about your IR Temperature Measurement Requirements
There are over 300 different pyrometer variants to choose from in the Optris infrared pyrometer portfolio each optimized for material, spot size, distance from the target, and environmental conditions. Fortunately, there is a trained engineer to phone or chat with to guide you through the process of choosing the perfect infrared sensor for your application.
The same support is available for the extensive IR camera product line.
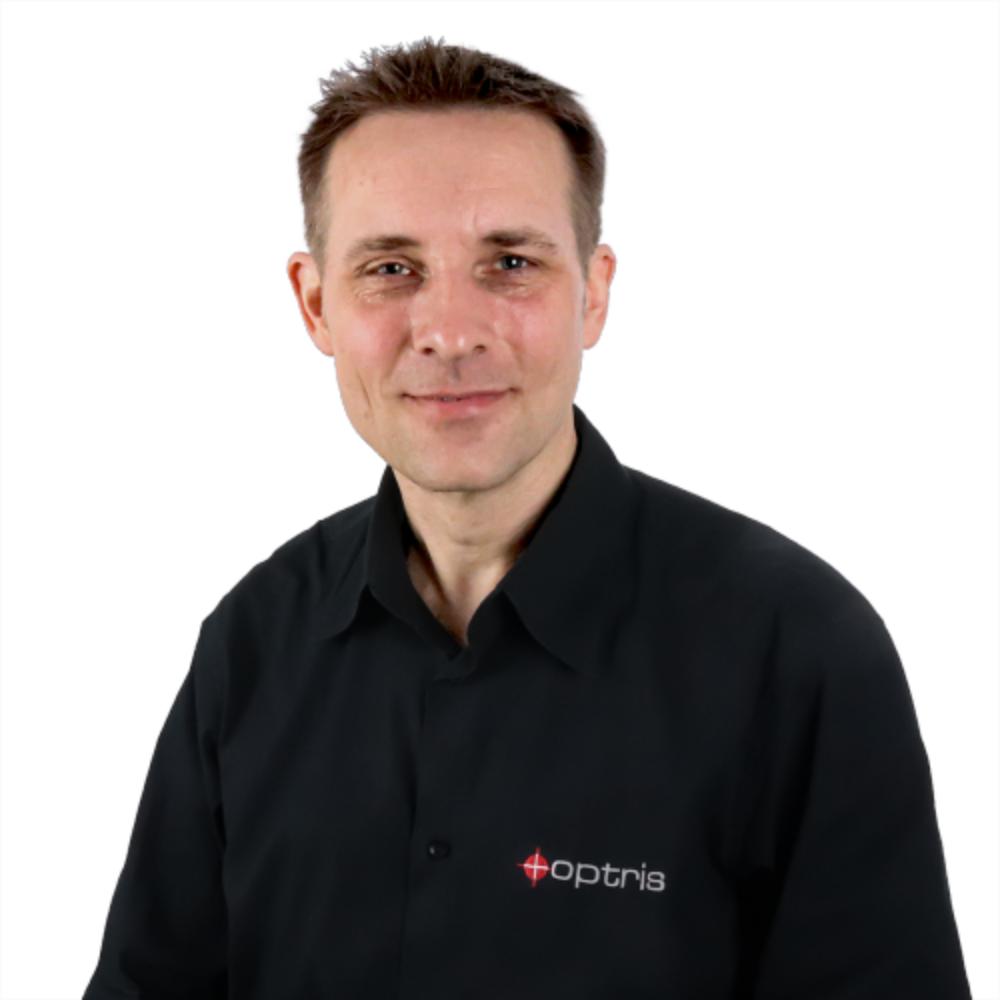