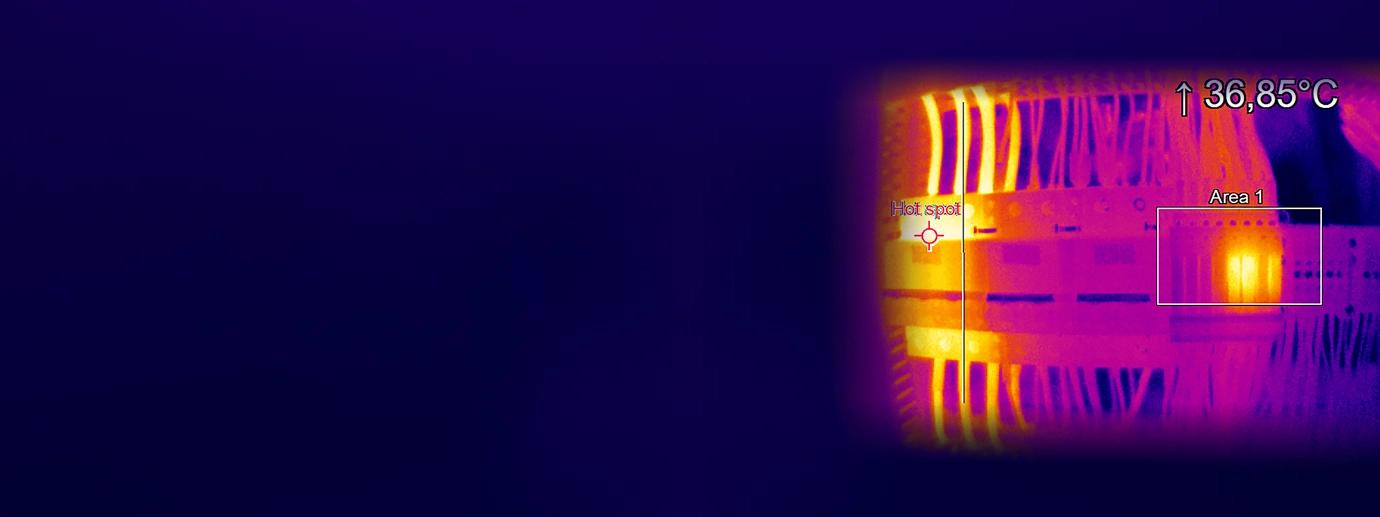
Smart IR Solutions for Control Cabinets and Predictive Maintenance
Achieving Continuous Monitoring and Early Fault Detection with the Xi 80 Infrared Camera
Why IR Temperature Monitoring is Raising in Control Cabinets prevents Overheating and Failures
Temperature monitoring in control cabinets helps prevent overheating and equipment failure by detecting potential issues early and allowing for preventive measures to be taken. This is essential for safety, as high temperatures can pose serious risks, including fire or explosion, especially in high-voltage environments. By ensuring that equipment operates within safe temperature limits, the safety of the entire system is maintained.
Monitoring the temperature also improves the lifespan of the installed equipment inside, as heat is a major factor in the degradation of electrical components. Keeping the temperature within optimal ranges minimizes wear and tear, extending the operational lifespan of these components. Additionally, excessive heat generation often indicates energy loss and inefficiency within the system. Identifying and addressing these inefficiencies through temperature monitoring leads to better energy utilization and reduced operational costs.
Temperature anomalies can serve as early indicators of issues such as phase imbalance, overload, poor electrical connections, or corrosion. Continuous monitoring allows for early detection and timely maintenance, preventing minor issues from escalating into major problems. This helps maintain the operational reliability of components inside control cabinets. Continuous temperature data also enables condition-based maintenance, optimizing maintenance schedules by performing maintenance proactively based on actual conditions rather than fixed schedules. Furthermore, many industries have regulations and standards that require temperature monitoring to ensure safe and reliable operation.
Temperature measurement in high-voltage (HV) environments poses safety challenges. Traditional electrical measurement methods, like thermocouples and RTDs, require highly insulated electronics and cables, which can interfere with HV objects and complicate installation and maintenance. Thick cable insulation hinders multi-channel applications in tight spaces, and sensor failures necessitate replacing the entire unit. Signal quality can also be affected by electromagnetic and electrostatic disturbances. In switchgear cabinets, where copper busbars are bolted together, rising joint temperatures indicate potential issues, highlighting the need for continuous temperature monitoring.
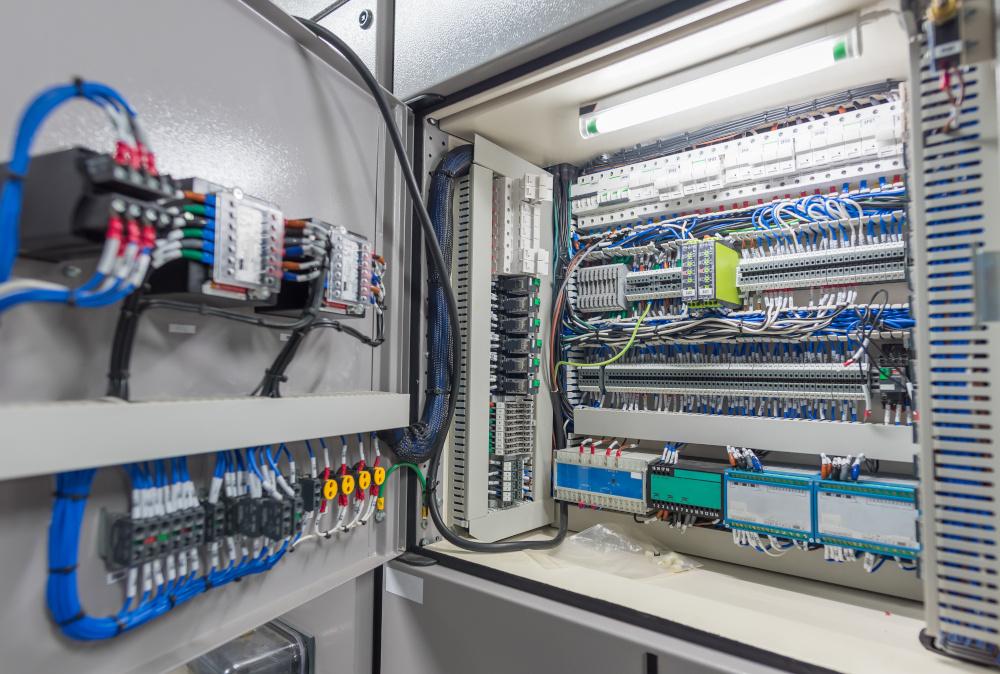
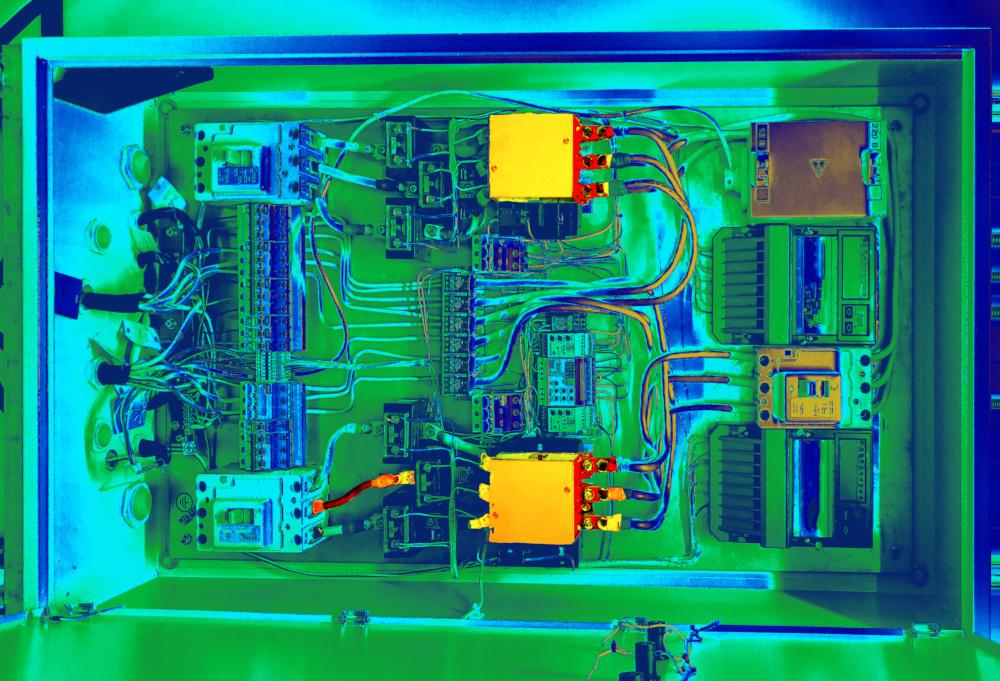
From Handheld IR Thermometers over Fixed IR Thermometers to Stationary IR Cameras
Traditionally, IR specialists use handheld infrared thermometers to inspect equipment for potential issues by detecting temperature anomalies. However, this method is being automated by fixed IR sensors for predictive maintenance. These stationary IR sensors offer continuous, real-time temperature monitoring, allowing for early detection of defects in hard-to-reach or expansive areas like large plants or high-rise buildings. Importantly, fixed IR pyrometers not only provide consistent data and reduce the need for manual inspections but also significantly enhance safety by promptly identifying overheating in electrical and mechanical systems.
Nevertheless, a stationary thermal camera should be considered when multiple spots need to be monitored close to each other. Especially inside switchgear cabinets, power is transferred by copper busbars bolted together at connections, which are particularly susceptible to failure. An increase in joint temperature can be an early sign of deterioration, detectable through continuous temperature monitoring using sensors. Busbars are often laid in triplicate in close approximation because of the three-phase alternating current. Instead of installing multiple CS LT pyrometers close to each other, a smart autonomous Xi 80 thermal camera is installed within the control cabinet. The wide-angle lens of the Xi 80 of 80° allows a large field of view and covers multiple measurement spots.
The IR camera must be installed inside the cabinet because infrared energy cannot penetrate solid substances like sheet metal. Measuring connections from the outside won’t effectively reveal internal issues unless specific IR windows are installed. While you can compare the exterior temperatures of sequential busway joints, the busway’s significant thermal mass often masks internal problems. A loose connection causing a significant temperature to rise inside may only result in a minor temperature change on the exterior. Installing the IR camera inside the cabinet provides a direct view of the internal connections, ensuring immediate detection of any problems.
Xi 80 Infrared Camera Revolutionizes Temperature Monitoring in Power Utilities
Traditionally, IR specialists use handheld infrared thermometers to inspect equipment for potential issues by detecting temperature anomalies. However, this method is being automated by fixed IR sensors for predictive maintenance. These stationary IR sensors offer continuous, real-time temperature monitoring, allowing for early detection of defects in hard-to-reach or expansive areas like large plants or high-rise buildings. Importantly, fixed IR pyrometers not only provide consistent data and reduce the need for manual inspections but also significantly enhance safety by promptly identifying overheating in electrical and mechanical systems.
Nevertheless, a stationary thermal camera should be considered when multiple spots need to be monitored close to each other. Especially inside switchgear cabinets, power is transferred by copper busbars bolted together at connections, which are particularly susceptible to failure. An increase in joint temperature can be an early sign of deterioration, detectable through continuous temperature monitoring using sensors. Busbars are often laid in triplicate in close approximation because of the three-phase alternating current. Instead of installing multiple CS LT pyrometers close to each other, a smart autonomous Xi 80 thermal camera is installed within the control cabinet. The wide-angle lens of the Xi 80 of 80° allows a large field of view and covers multiple measurement spots.
The IR camera must be installed inside the cabinet because infrared energy cannot penetrate solid substances like sheet metal. Measuring connections from the outside won’t effectively reveal internal issues unless specific IR windows are installed. While you can compare the exterior temperatures of sequential busway joints, the busway’s significant thermal mass often masks internal problems. A loose connection causing a significant temperature to rise inside may only result in a minor temperature change on the exterior. Installing the IR camera inside the cabinet provides a direct view of the internal connections, ensuring immediate detection of any problems.

Recommended Products
Other Condition Monitoring Applications
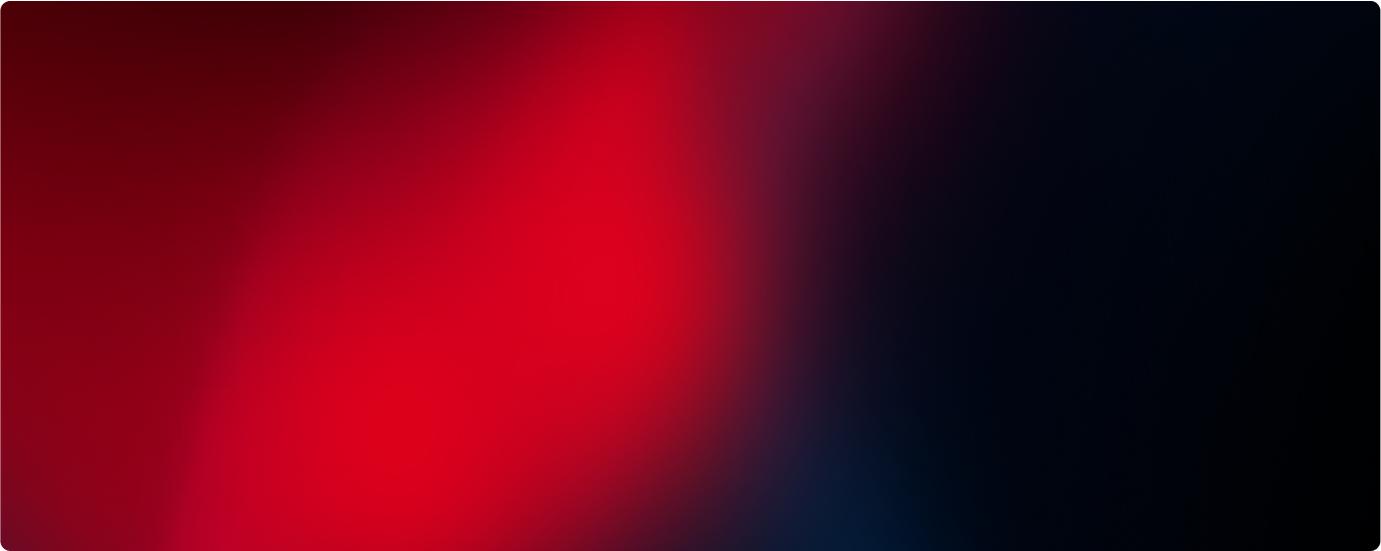
Talk to us about your IR Temperature Measurement Requirements
There are over 300 different pyrometer variants to choose from in the Optris infrared pyrometer portfolio each optimized for material, spot size, distance from the target, and environmental conditions. Fortunately, there is a trained engineer to phone or chat with to guide you through the process of choosing the perfect infrared sensor for your application.
The same support is available for the extensive IR camera product line.
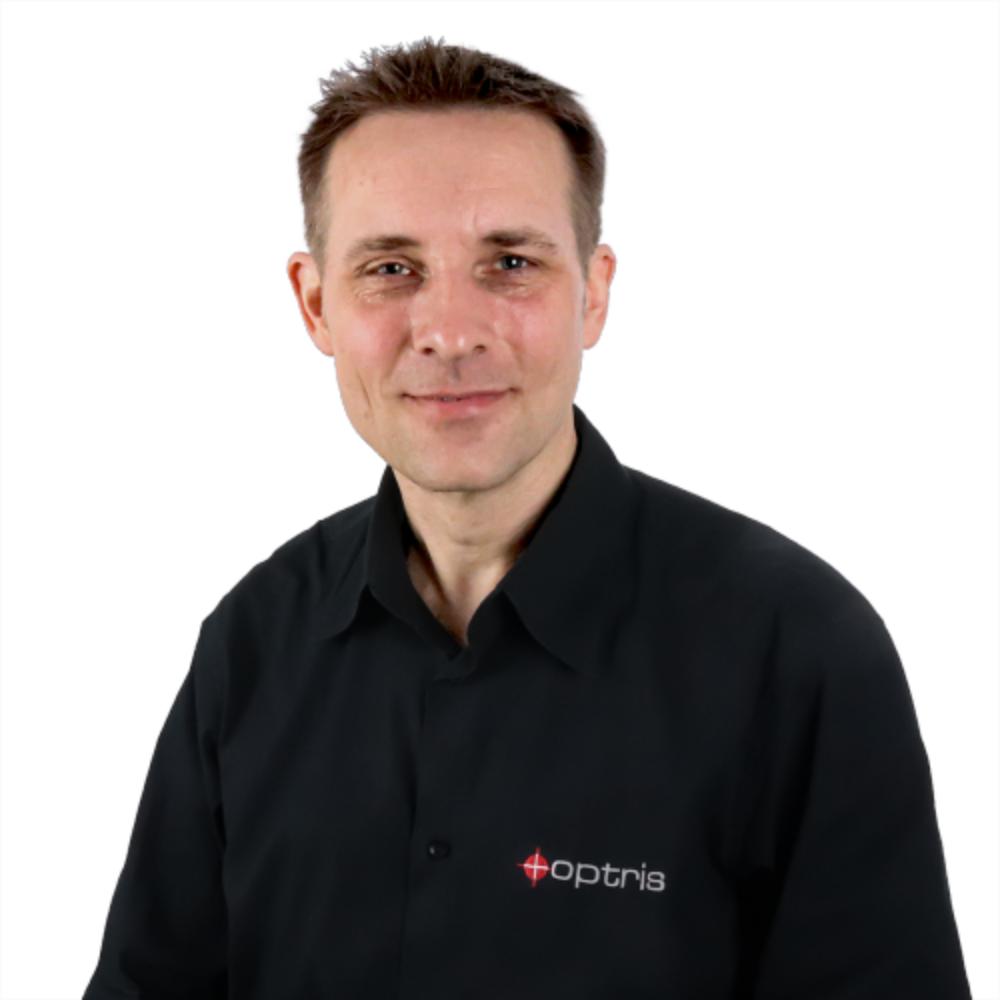