
Optimize Fuel Combustion with the Cost-Effective Flame Measurement
Precision Without the Expense: Reliable and Cost-Effective Flame Temperature Measurement
Accurate Flame Temperature Measurement to Maximize Efficiency in Fuel Combustion Processes
In combustion studies, the adiabatic flame temperature represents the maximum temperature a flame can reach under ideal conditions. It serves as the theoretical upper limit for flame temperatures in actual processes, assuming that all the enthalpy of combustion is fully transferred into the gases produced during combustion. A 100% equivalence ratio indicates a perfect stoichiometric mixture, where all the fuel reacts entirely with all the available oxygen in the mixture. This condition maximizes the flame temperature because no heat is lost to heating excess oxygen or other unreacted components.
In real-world scenarios, flame temperatures are generally lower than the adiabatic flame temperature at a 100% equivalence ratio. The highest flame temperature occurs when all the energy from combustion is used to heat the gaseous combustion products. This optimal temperature is achieved when there is precisely enough air for complete combustion neither too much nor too little. If excess air is present, the additional air absorbs some of the combustion energy, lowering the flame temperature. Conversely, if there is insufficient air, incomplete combustion reduces the energy released, resulting in a lower flame temperature.
Accurate flame temperature measurements are crucial for developing and testing new fuels in rocket propulsion and other high-performance applications. These measurements help researchers refine fuel compositions and improve their performance.
Flame temperature measurement is also vital for optimizing combustion processes. Accurate temperature data enables better combustion control, leading to enhanced efficiency and reduced emissions.
Additionally, flame temperature measurement plays a critical role in assessing the performance of various fuel compositions. Understanding how different chemical reactions occur at varying temperatures allows industries to develop or select fuels that offer better efficiency and lower emissions, thus contributing to environmental sustainability.
Thermocouples are the most commonly used traditional tool for measuring flame temperature. They consist of two dissimilar metal wires joined at one end, forming a junction. When exposed to a flame, the junction generates a voltage corresponding to the temperature, which can then be measured and converted into temperature data. While thermocouples are widely used due to their simplicity and cost-effectiveness, they have notable limitations. They provide only point measurements, meaning they measure the temperature at the specific location where the thermocouple is placed within the flame. This can lead to incomplete or inaccurate readings, particularly in heterogeneous flames. Moreover, thermocouples are invasive, potentially disturbing the flame and accumulating soot, which can cause measurement errors. Additionally, the accuracy of thermocouple measurements is affected by heat exchange through conduction and radiation, resulting in discrepancies between the thermocouple and the actual gas temperature.
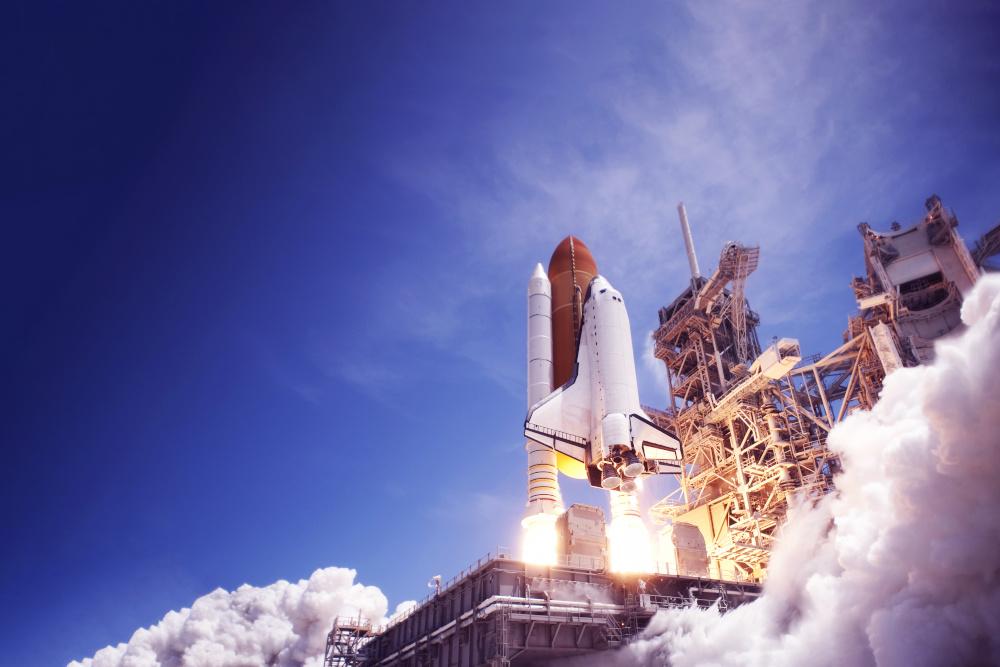
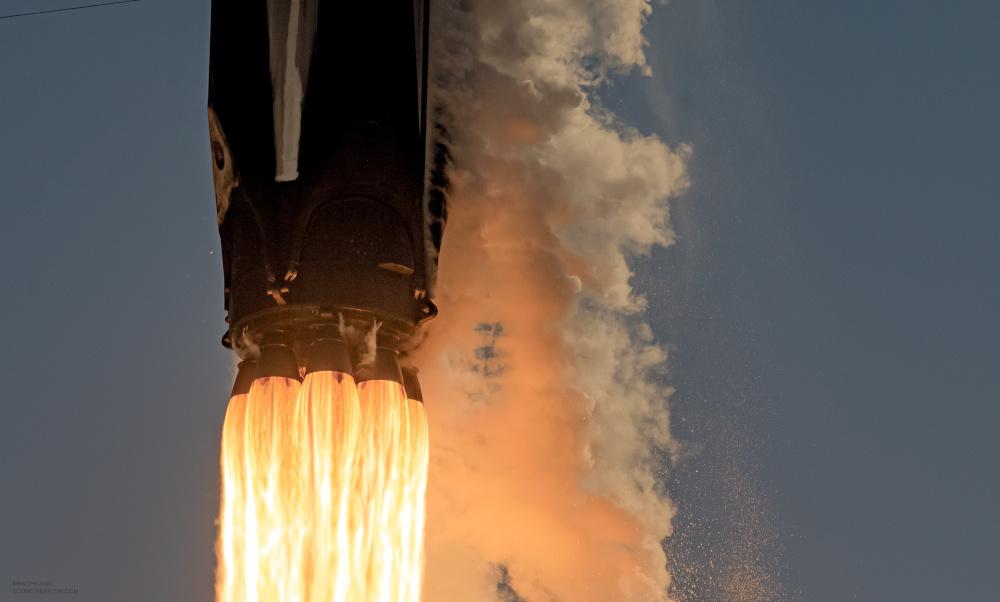
Optimizing Combustion with 4.3 µm Infrared Thermometry for Non-Intrusive Flame Temperature Measurement
Infrared thermometry is a non-intrusive method for measuring flame temperature by detecting the thermal radiation emitted by the flame. Unlike thermocouples, this technique does not require physical contact with the flame, thereby avoiding potential disturbances and inaccuracies associated with invasive measurements.
In this method, detectors sensitive to specific infrared wavelengths capture the radiative emission from the flame. The intensity of this radiation is then compared to that of a known blackbody source to estimate the flame temperature accurately.
One of the primary advantages of IR thermometry is its ability to measure temperature without disturbing the flame. However, accurate readings require careful calibration and consideration of factors such as emissivity, absorption, and scattering by combustion gases and soot particles.
Infrared thermometry for flame temperature measurement typically focuses on a wavelength around 4.3 micrometers (µm). This wavelength is particularly significant because it aligns with the strong infrared emission band of carbon dioxide (CO₂), a major product of hydrocarbon combustion. At 4.3 µm, the asymmetric stretch vibration of CO₂‚ molecules are a dominant emitter in the infrared spectrum, making this wavelength ideal for detecting the thermal radiation emitted by the flame. This specific focus ensures that the temperature readings closely correspond to the actual flame temperature, as the radiation intensity at this wavelength is directly linked to the temperature of the CO₂, molecules.
The Optris CTLaser F2 pyrometer is specifically designed to measure CO₂‚ flame gases accurately within this spectral range of 4.3 µm. By targeting this precise wavelength, the pyrometer minimizes interference from other gases and background radiation, enhancing the accuracy of flame temperature measurements.
Calibrated for a temperature range of 200 °C to 1650 °C (382 °F to 3002 °F), the Optris CTLaser F2 is well-suited for various industrial combustion processes. It provides reliable temperature measurements without physical contact with the flame, thereby preserving the integrity of the combustion process. Additionally, the pyrometer is built to operate effectively in harsh environments without the need for additional cooling, making it a versatile and dependable tool in industrial settings.
Why The CTLaser F2 is the Ideal Cost-Effective Alternative to Cooled Cameras
The high temperatures of flames result in the emission of substantial infrared radiation, offering valuable insights into the combustion process. The CTLaser F2 is a highly affordable and robust solution for flame temperature measurement, providing a cost-effective alternative to more expensive cooled infrared imaging systems. Cooled infrared systems, while offering high sensitivity and precision, come with several significant disadvantages. They require complex cooling mechanisms, often using cryogenic cooling or thermoelectric coolers, which add to the overall cost, maintenance, and operational complexity. These cooling systems are not only expensive to install and operate but also prone to failure in harsh industrial environments, leading to increased downtime and higher maintenance costs.
In contrast, the CTLaser F2 delivers precise and reliable temperature readings without the need for such cooling equipment, making it an excellent choice for industrial applications where budget considerations are important. Its durable design ensures long-lasting performance even in challenging conditions, further reducing the risk of operational disruptions. This combination of affordability, durability, and high accuracy makes the CTLaser F2 a compelling option for those seeking reliable temperature measurement without the high costs and maintenance burdens typically associated with cooled infrared technologies.
Recommended Products
Other Condition Monitoring Applications
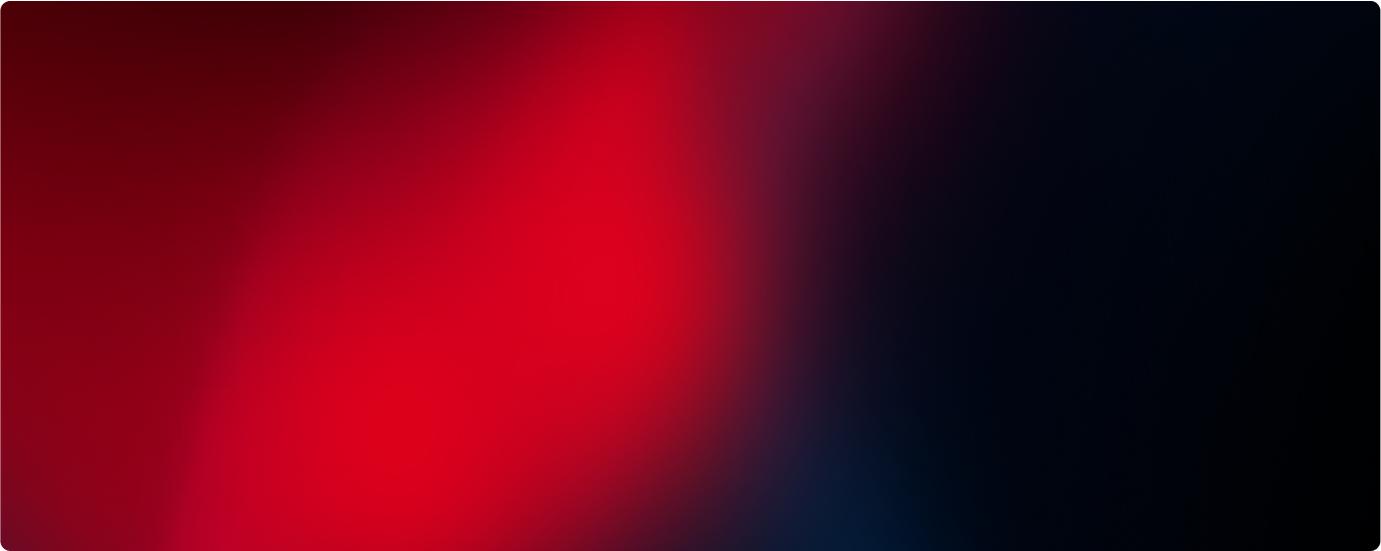
Talk to us about your IR Temperature Measurement Requirements
There are over 300 different pyrometer variants to choose from in the Optris infrared pyrometer portfolio each optimized for material, spot size, distance from the target, and environmental conditions. Fortunately, there is a trained engineer to phone or chat with to guide you through the process of choosing the perfect infrared sensor for your application.
The same support is available for the extensive IR camera product line.
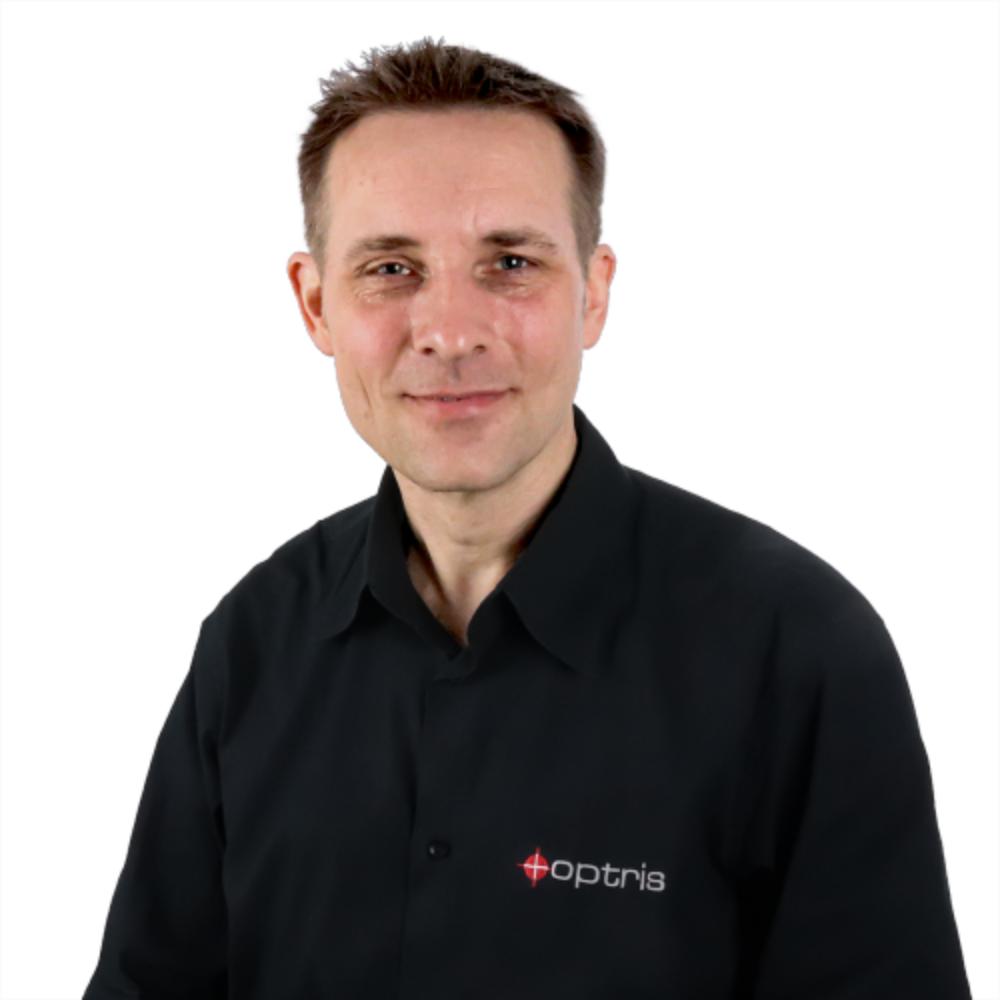