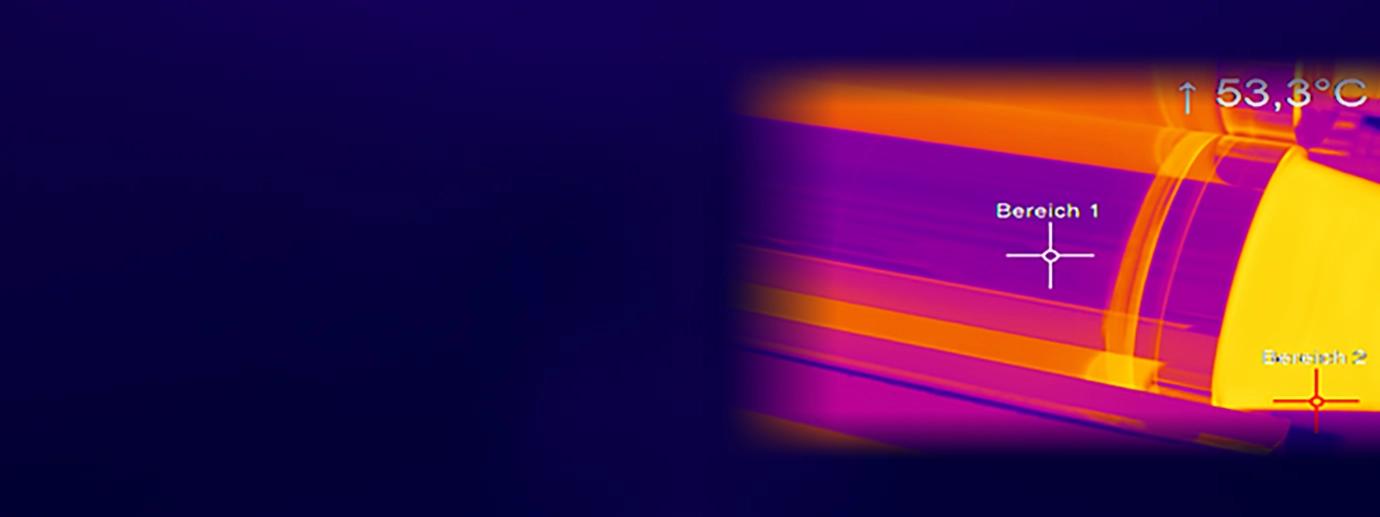
Ensuring Precise Temperature Control in Industrial Thermoforming Process
Optimal Thermoforming Through Controlled Heating and Infrared Temperature Monitoring even with Thin Film Thermoplastic
Controlling the Glass Transition Temperature in Thermoforming with Infrared Radiators
Thermoforming is a manufacturing process used to shape thermoplastic materials by heating a plastic sheet until it becomes pliable and then molding it into a specific form. This process is crucial in packaging, which is used to create food packaging, medical trays, and consumer goods packaging. In the automotive industry, thermoformed plastics are used for components such as dashboards, door panels, and interior trim. They are vital for producing window profiles, pipes, and insulation materials in construction. Additionally, thermoformed plastics are found in various consumer goods, including beverage bottles, functional shoe films, and other everyday products.
The thermoforming process begins by heating a thermoplastic sheet until it becomes soft and pliable, reaching its glass transition temperature. This step is essential as it allows the material to be easily shaped into the desired form. Infrared radiators are typically used for this purpose due to their efficiency and ability to provide controlled heating. Once the thermoplastic sheet is pliable, it is formed into the desired shape using a mold through methods such as vacuum forming, pressure forming, or mechanical forming.
Each method has specific applications and advantages but relies on molding the heated plastic by applying pressure or vacuum. After forming, the sheet must be cooled to solidify the new form, ensuring the plastic retains its shape and structural integrity. The cooled part is removed from the mold and may undergo additional trimming and finishing to achieve the final product specifications. Materials commonly used in thermoforming include polyethylene (PE), polypropylene (PP), polystyrene (PS), polyethylene terephthalate (PET), acrylonitrile butadiene styrene (ABS), and polyvinyl chloride (PVC). Ensuring temperature homogeneity is crucial to avoid defects in the final product, as uniform heating guarantees that the entire plastic sheet reaches the same pliability level, preventing weak spots or inconsistencies. Sufficient heat penetration is also essential for achieving the necessary pliability without overheating.
Infrared sensors are necessary to ensure the plastic reaches its glass transition temperature. However, temperature monitoring can be challenging because the plastics are often less than 400 µm thick, and the process involves infrared heaters. Infrared heaters transmit heat or energy contactlessly through directed infrared radiation. To use infrared heating processes as efficiently as possible, the emissivity of the plastic material must be considered, determining whether the IR emitter should operate in the short, medium, or long-wave infrared range. The emissivity depends on the material, surface quality, wavelength, angle, and, in some cases, the applied configuration.
The requirements for the radiant heater/infrared radiator differ depending on the wavelength of the IR radiation and the material of the product. A challenge in this aspect is that an infrared sensor working in the same wavelength range could pick up back reflection from the heat emitter.
Moreover, thin plastic film is used for thermoforming parts with thin wall thickness, which might be transparent in some spectral ranges. This makes this application even more challenging, as an infrared temperature sensor with the wrong spectral sensitivity might not pick up the plastic film’s infrared radiation.
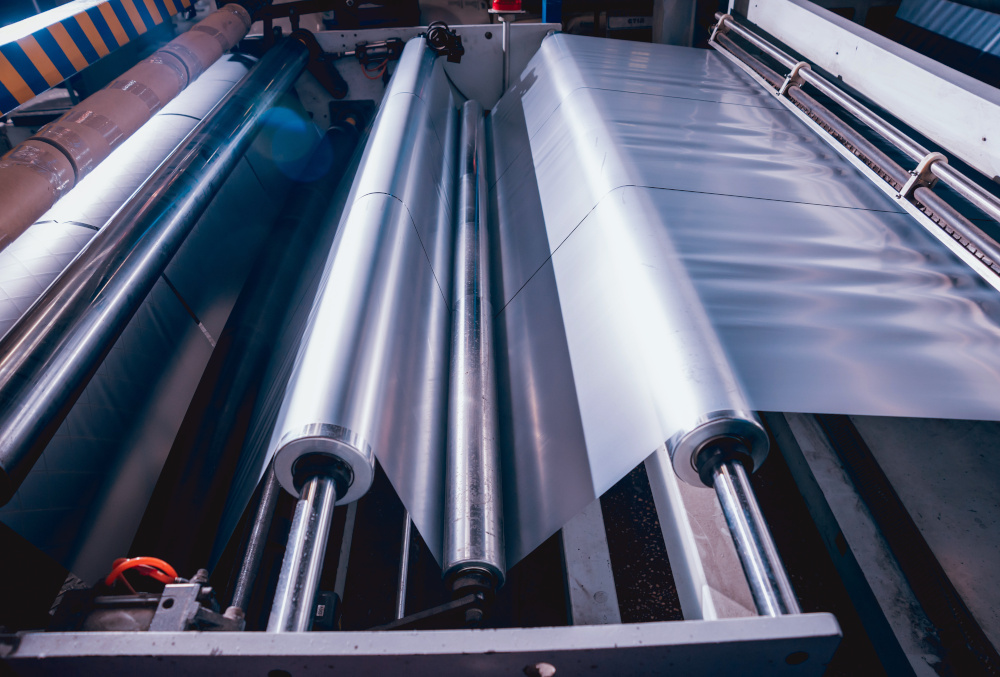
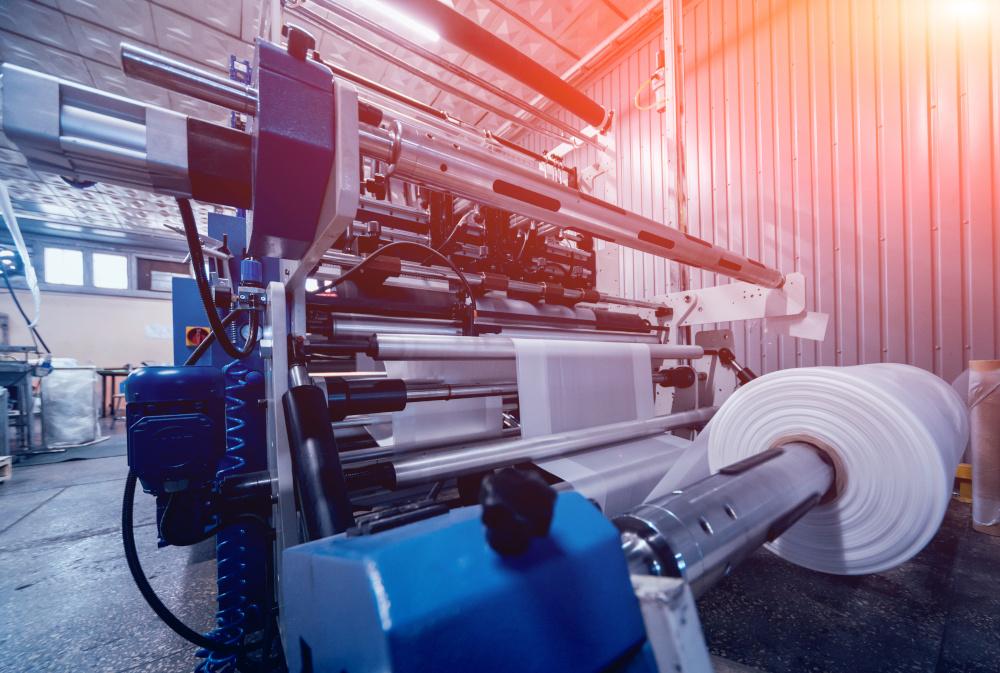
Control Thermoforming Temperature: The Role of Infrared Radiator and Pyrometer’s Spectral Ranges
Infrared radiators are typically employed because they can provide controlled and uniform heating, ensuring the thermoplastic sheet reaches the necessary glass transition temperature. Understanding the condition of the heated surface is pivotal for controlling the heating process. Infrared pyrometers monitor the glass transition temperature of the plastic before it is shaped, offering the fastest and most direct measurement method.
One challenge of IR measurement near IR heaters is avoiding measurement in the same spectral range in which the heaters operate. Infrared heaters and dryers typically function within the wavelength bands of near-infrared (NIR) and mid-infrared (MIR). NIR heaters usually work in the range of 0.75 µm to 1.5 µm, providing intense and focused heat ideal for rapid heating applications. MIR heaters operate within the 1.5 µm to 5.0 µm range, offering balanced heating suitable for both surfaces and slightly deeper penetration into materials. To avoid crosstalk, a pyrometer typically operates in the 8 µm – 14 µm long wavelength (LT) range for most drying and heating applications. The best practice is to use an infrared sensor with a different sensitivity than the IR heater to avoid crosstalk.
Challenges also arise with thin plastic films, which may be transparent in some spectral ranges. This necessitates using sensors with the correct spectral sensitivity to avoid inaccurate readings from back reflections. Plastics with a thickness greater than 0.4 mm and pigmented films can be measured easily in the long-wave IR spectral range (8-14 μm) with emissivities of ≥ 0.9. However, very thin plastic films are transparent in this spectral range, making temperature measurement possible only with material-specific absorption bands in the IR spectrum via narrow-band sensitive IR sensors.
Infrared temperature measurement in plastics involves specific spectral bands and temperature ranges. The C-H band, with a wavelength of 3.43 μm, is effective for temperatures above 50°C (P3 > 50°C). In contrast, the C-F Ester band, with a wavelength of 7.95 μm, is suitable for temperatures above 0°C (P7 > 0°C). Different plastic materials respond differently to these spectral bands. Polyethylene (PE), polypropylene (PP), cellophane, and polystyrene (PS) are sensitive to the C-H band at 3.43 μm but not to the C-F Ester band. In contrast, fluoroplastic (FEP) and polyimide are sensitive to the C-F Ester band at 7.95 μm but not to the C-H band. Some materials, such as acrylic and polycarbonate, respond to both bands. Polyester is effective with the C-H band for thicknesses greater than 10 μm and responds to the C-F Ester band. Polyvinyl chloride (PVC) is responsive to both spectral bands, making it versatile for infrared temperature measurement applications.
Cost-Effective Temperature Management in Thermoforming with Easy Installation and Thermoshock-Insensitive Pyrometers
CT LT sensors have been employed in an application producing inexpensive plastic packaging for grocery food items. Long-wavelength sensors are sufficient since the plastic film is thicker than 400 µm. The manufacturer has integrated several pyrometers in a line to monitor temperature inhomogeneities. If the temperature readings differ, the programmable logic controller (PLC) adjusts the power of the infrared heaters based on the temperature data received over analog inputs. The online thermometers are installed next to the infrared heaters, where the plastic film reaches its maximum temperature, to avoid any parasitic reflections. Despite this, the ambient temperature is significant, so the sensor must withstand temperatures.
The Optris thermoshock-insensitive feature of the pyrometer is crucial in this application, as it ensures accurate and reliable temperature measurements even in environments with rapid temperature fluctuations or nearby heat emissions. Optris supplies a range of mechanical accessories that greatly simplify the integration of their sensors into existing thermoforming machinery. These accessories include mounting brackets, adjustable stands, windows, and protective housings, making it easier for manufacturers to incorporate infrared temperature measurement systems into their machinery without extensive modifications. Moreover, the sensing head can be disconnected from the electronics box, simplifying installation and maintenance in complex machinery setups. This not only saves time but also reduces installation costs.
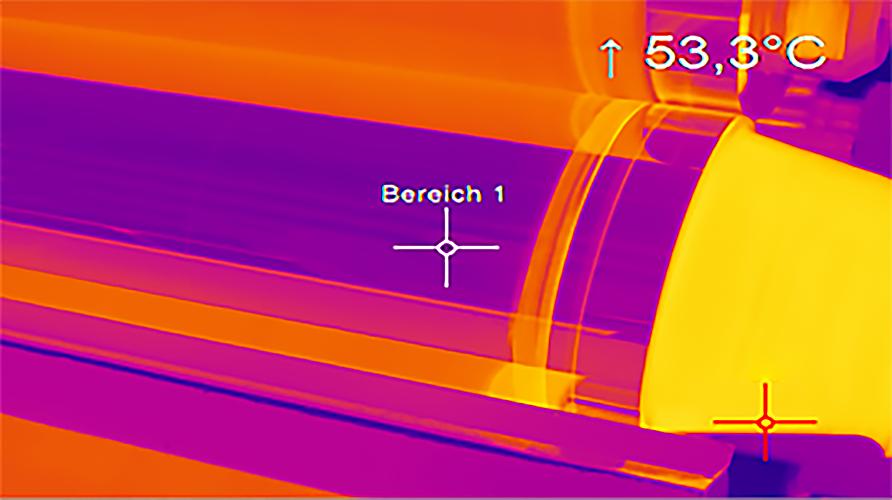
Recommended Products
Other Plastic Applications
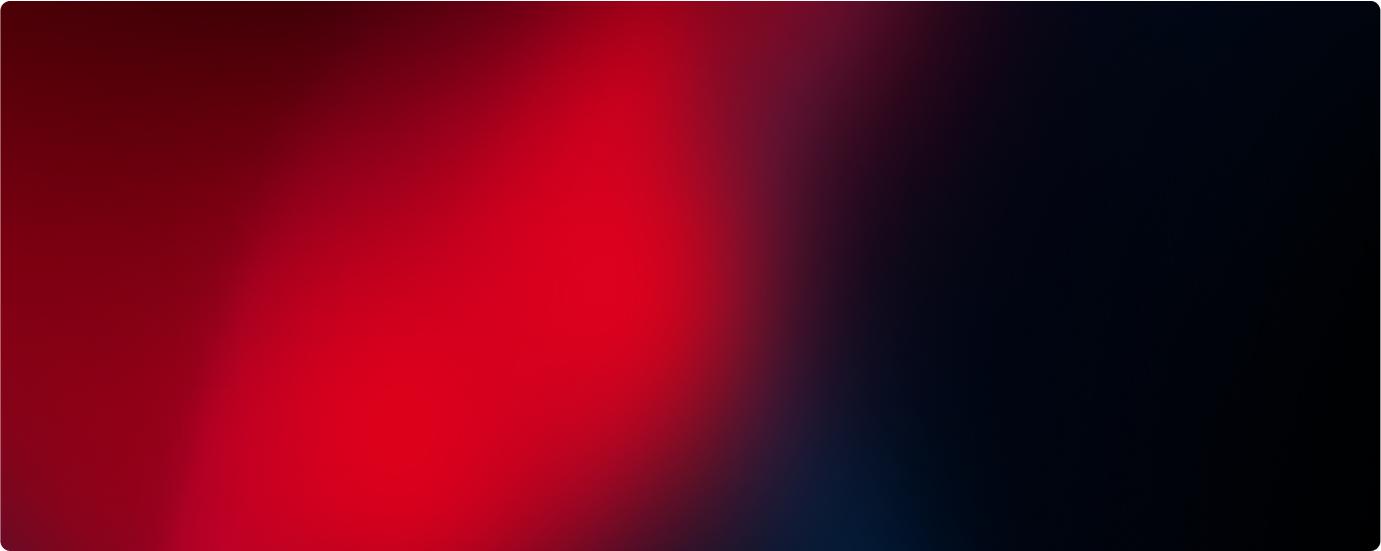
Talk to us about your IR Temperature Measurement Requirements
There are over 300 different pyrometer variants to choose from in the Optris infrared pyrometer portfolio each optimized for material, spot size, distance from the target, and environmental conditions. Fortunately, there is a trained engineer to phone or chat with to guide you through the process of choosing the perfect infrared sensor for your application.
The same support is available for the extensive IR camera product line.
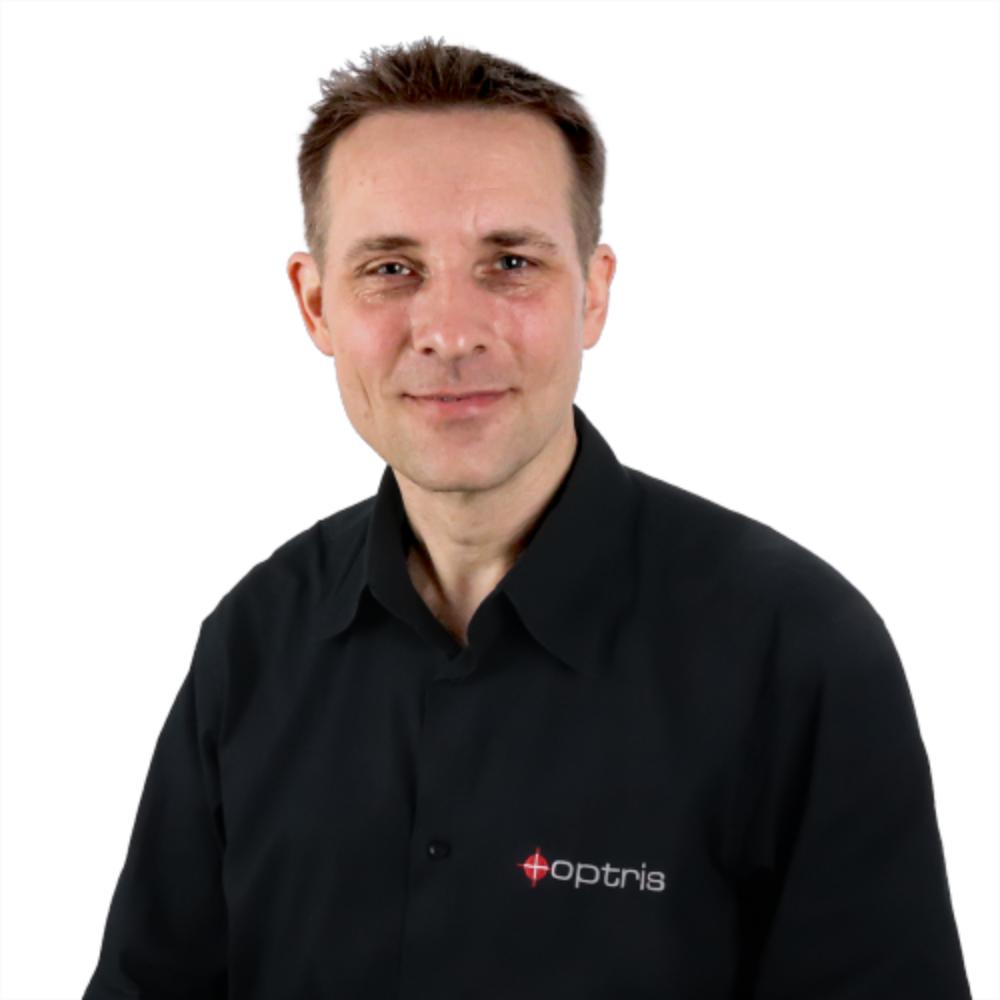