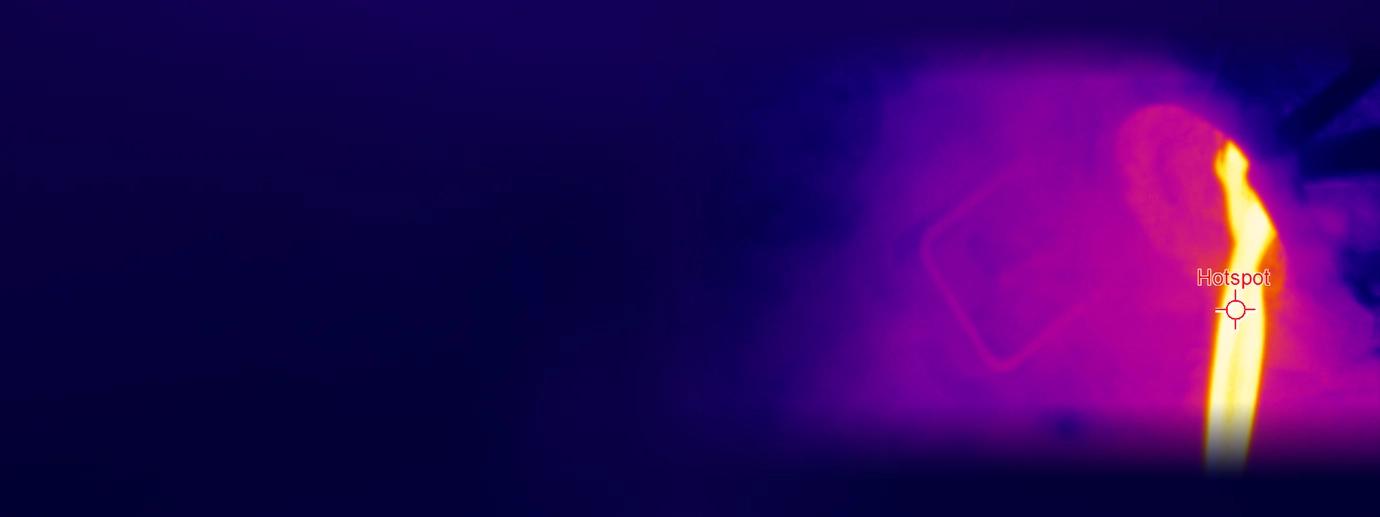
Automation and Accuracy: Infrared Technology in Enamel Manufacturing
Real-Time Data Integration into Process Control for Efficient Temperature Management
Precise Temperature Monitoring in Enamel Production to Ensure Product Quality
Enamel production, a material mix that includes glass and ceramics, requires precise temperature monitoring to ensure consistent product quality. During manufacturing, the material is heated in rotary kilns until it reaches a viscous consistency. This heated material is then poured out and later processed into granules, which are used in producing enamel for household appliances, glazes, and roof tiles, among other things.
A critical step in the process is the material pour, where the hot enamel flows from the kiln. Temperature measurement plays a central role here, as deviations in temperature can lead to quality variations in the final product. Temperatures during this process can range from approximately 1000°C to 1500°C. Until recently, many glass manufacturers measured the temperature sporadically with a handheld pyrometer. However, this method only captures snapshots, leading to significant measurement fluctuations between the start and end of the pour. This was one of the biggest challenges for glass manufacturers, as these temperature differences directly impacted product quality.
The motivation to implement more precise and continuous temperature measurement was clear: the previous solution needed to adequately monitor and document the temperature fluctuations in the production process. For enamel manufacturers, the focus is on an automated solution that monitors the temperature throughout the pour, ensuring consistent quality.
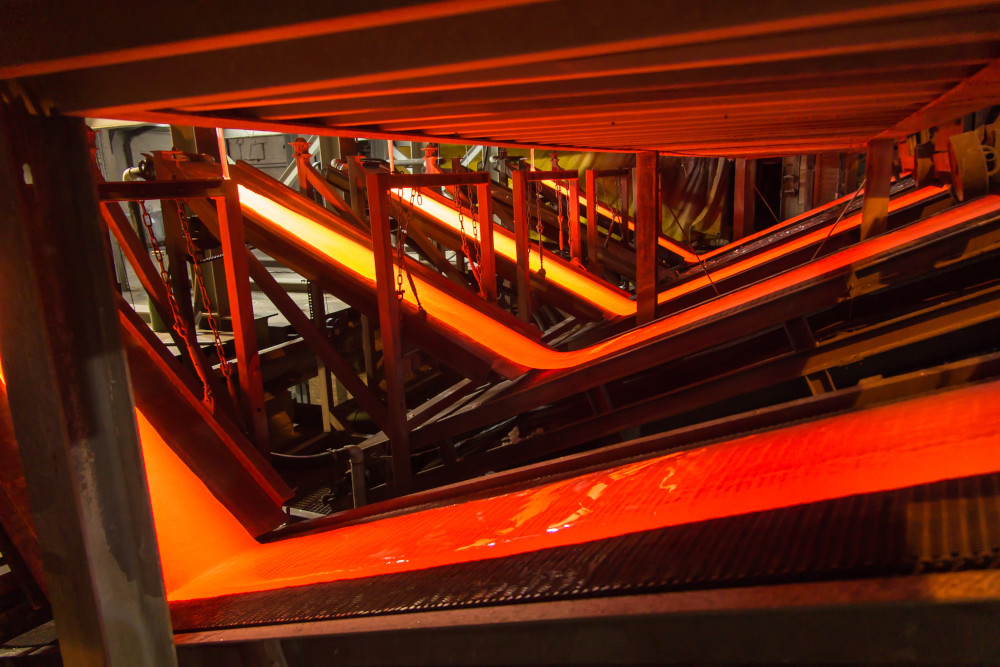
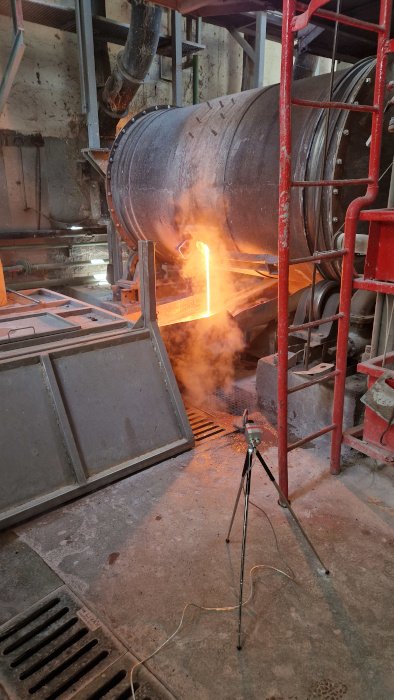
Infrared Temperature Measuring Camera An Ideal Solution for Enamel High-Temperature Application
The Optris solution is based on the highly precise PI 1M infrared camera designed for high-temperature applications like glass enamel production. With its wide measurement range of 450 °C to 1800 °C, the camera can reliably capture the high temperatures of the material. Thanks to its highly dynamic CMOS technology with a resolution of up to 764 x 480 pixels and a frame rate of up to 1 kHz, the PI 1M is particularly suitable for fast processes. This ensures that even the most minor temperature differences can be detected, which is crucial for measurement accuracy.
The Optris PI 1M offers excellent thermal sensitivity of less than 2 K below 900 °C and less than 4 K below 1400 °C. This enables precise temperature measurements, even in dynamic production environments. The camera is positioned in the material pour process to have an unobstructed view of the hot material stream during the pour. Enamel manufacturers typically opt for a fixed infrared camera installation to directly integrate the measured temperature data into the plant’s control architecture (PLC). This is achieved via the 0–10 V analog input and the camera’s digital input/output interfaces. Particularly noteworthy is the camera’s response time of just 1 ms, which allows for near real-time reactions to temperature fluctuations and adjustments to the production process.
Another essential feature is the 1 kHz line-scanning option, which allows for high-accuracy monitoring of fast processes. This helps the enamel manufacturer minimize temperature differences during the pour, ensuring consistent product quality. With an optional cooling housing and protective devices like the Laminar Air Purge to prevent dust accumulation on the lens, the camera can also be adapted to the harsh environmental conditions in production.
Automation and Efficiency in Enamel Production are Major Advantages for Glass Manufacturers
Implementing the Optris PI 1M provides enamel manufacturers with significant advantages in enamel production. Through continuous temperature monitoring, it can be identified that significant temperature fluctuations may occur at the beginning, middle, and end of the pour. These insights enabled fine adjustments to the process parameters, which led to consistent product quality. The ability to immediately detect temperature deviations means that the production process now runs much more efficiently and in a more controlled manner.
A major advantage of the Optris solution lies in automating the entire temperature measurement process. Whereas previously, an employee manually conducted sporadic measurements with a handheld pyrometer, the permanently installed PI 1M now ensures continuous monitoring. This led to a significant reduction in labor effort, as manual monitoring is no longer required. The camera’s fast analog output also allows for direct integration into process control, ensuring the entire temperature monitoring process is optimized without manual intervention.
The Optris PI 1M impresses with its robustness and versatility. Its IP67 rating makes it dust—and splash-proof, making it ideal for industrial environments. Additionally, the camera offers an impressive accuracy of ±1% for temperatures below 1400 °C and ±2% for higher temperatures. This precision and the ability to integrate the camera into existing systems easily make Optris a reliable partner for this application.
This advanced solution allows glass manufacturers to improve product quality, increase process stability, and reduce long-term costs. The Optris PI 1M is the ideal choice for glass enamel production, as it meets all the manufacturers’ accuracy, efficiency, and automation requirements.
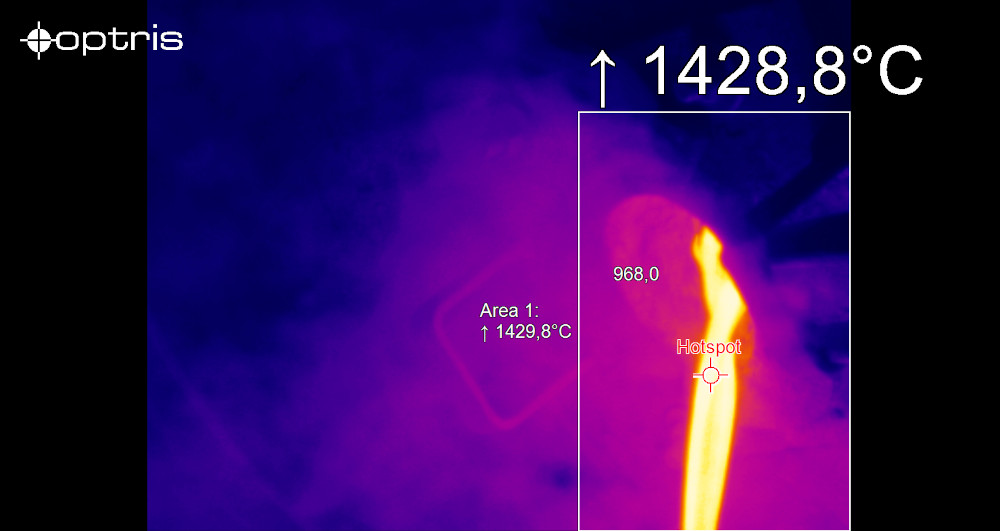
Recommended Products
Other Glass Applications
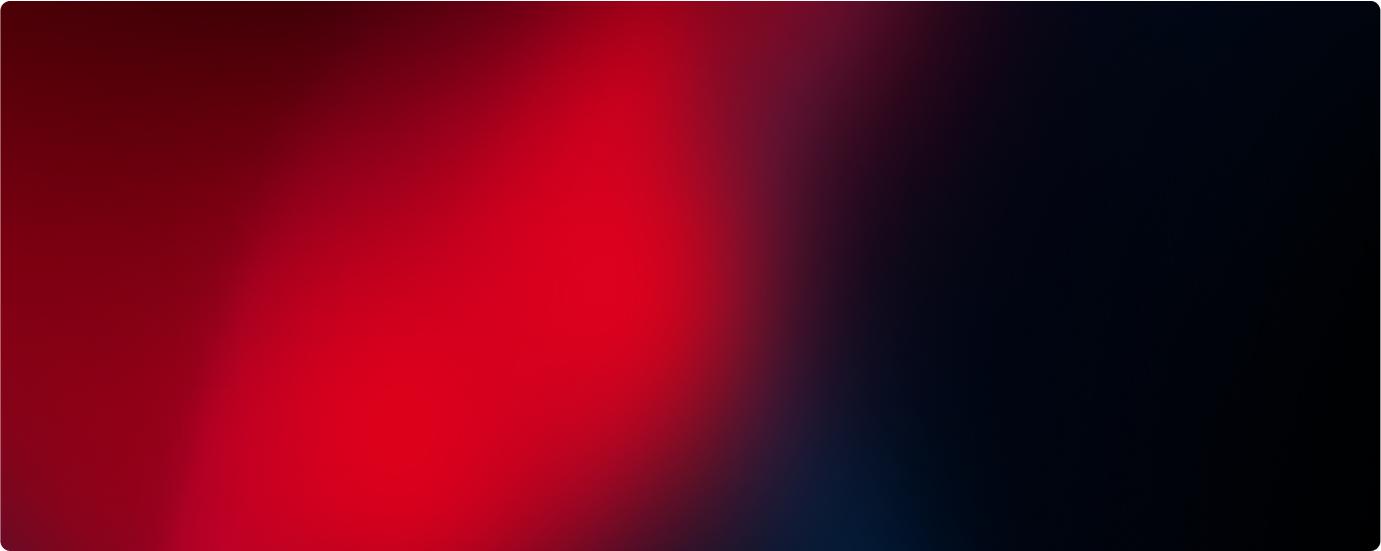
Talk to us about your IR Temperature Measurement Requirements
There are over 300 different pyrometer variants to choose from in the Optris infrared pyrometer portfolio each optimized for material, spot size, distance from the target, and environmental conditions. Fortunately, there is a trained engineer to phone or chat with to guide you through the process of choosing the perfect infrared sensor for your application.
The same support is available for the extensive IR camera product line.
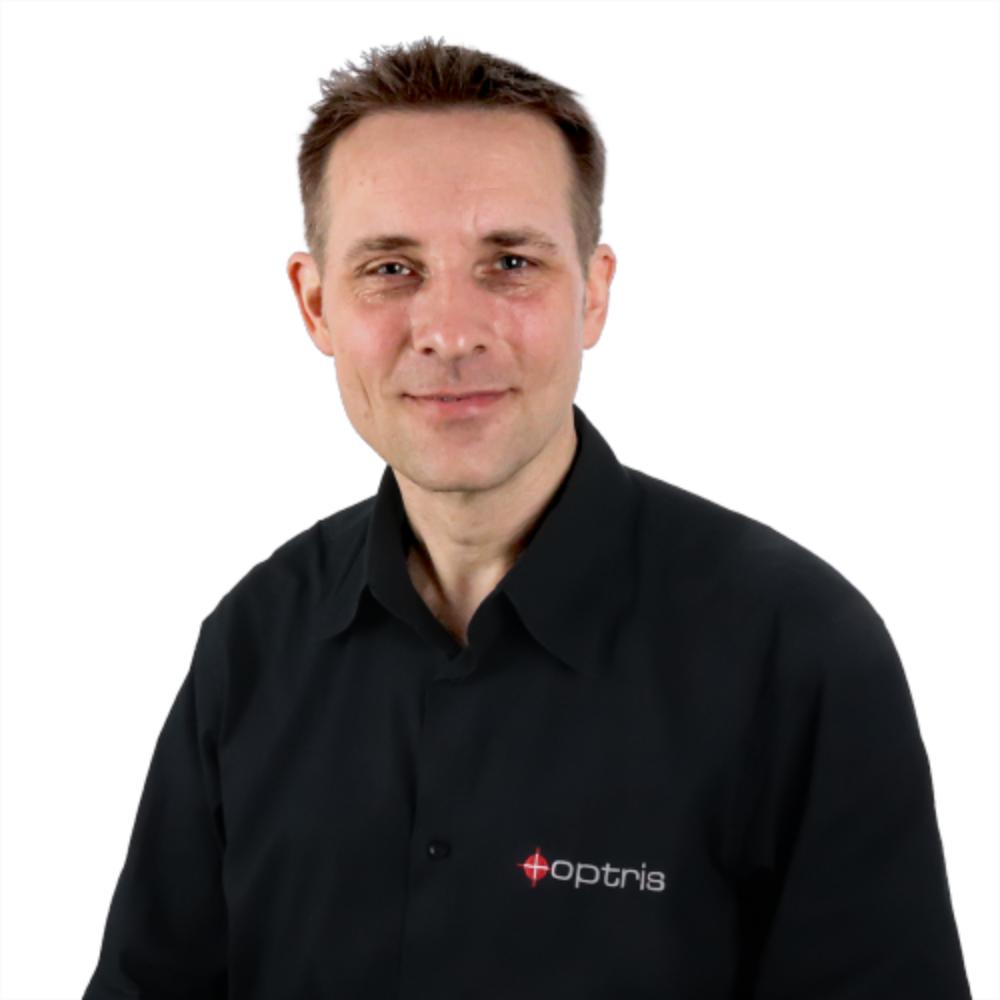