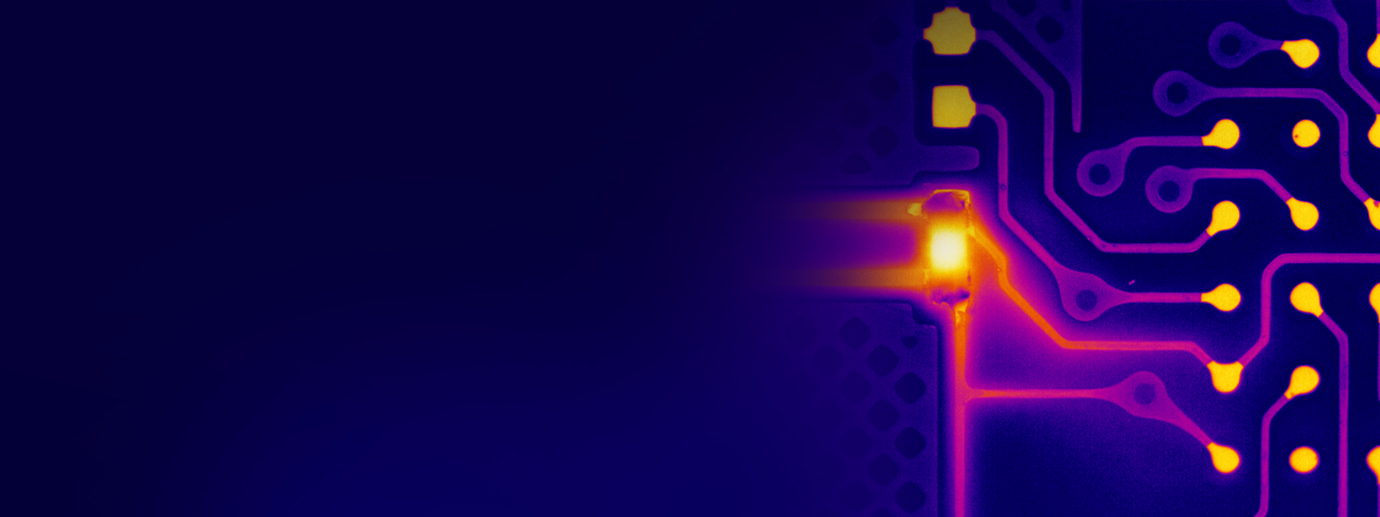
IR Cameras & Pyrometers for Electronics Industry
Temperature Control for Optimizing Electronics Manufacturing Processes
The Importance of IR Temperature Measurement in the Electronics Industry
Infrared (IR) temperature measurement is essential in the electronics industry, playing a crucial role in optimizing manufacturing processes and ensuring component reliability. Accurate temperature control is vital for component inspection and PCB manufacturing. IR thermometers and cameras offer non-contact measurement, which is ideal for these high-precision applications.
Component inspection benefits significantly from IR technology. In electronics manufacturing, maintaining precise thermal conditions prevents overheating and ensures the integrity of sensitive components. IR sensors detect temperature variations in real-time, allowing for immediate adjustments and reducing the risk of component failure.
For printed circuit boards (PCB), IR measurement ensures consistent thermal profiles during soldering and assembly. Proper temperature management prevents issues such as thermal damage, warping, and solder joint defects, which can compromise board performance and reliability.
Additionally, IR temperature measurement enhances process efficiency and energy savings. By accurately monitoring and controlling temperatures, manufacturers can optimize heating and cooling processes, reducing energy consumption and operational costs. Integrating IR technology into electronics production not only improves product quality but also supports more sustainable and cost-effective manufacturing practices, making it indispensable in the industry.
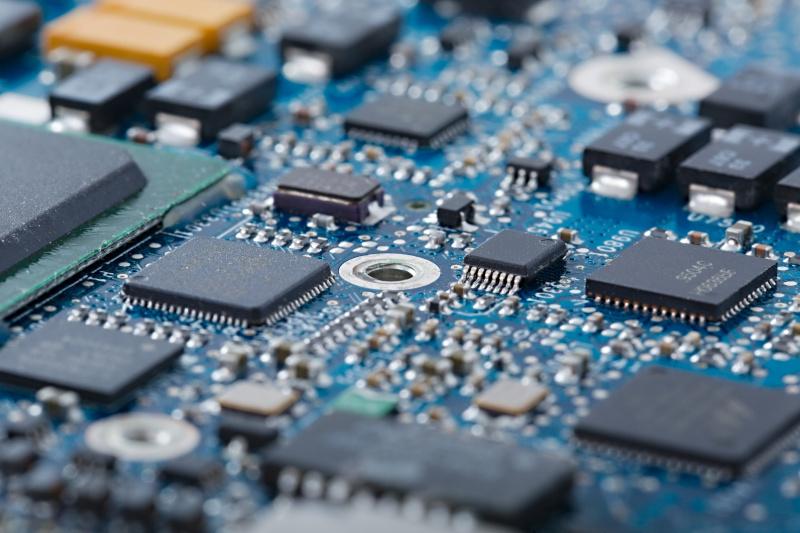
Electronics Applications
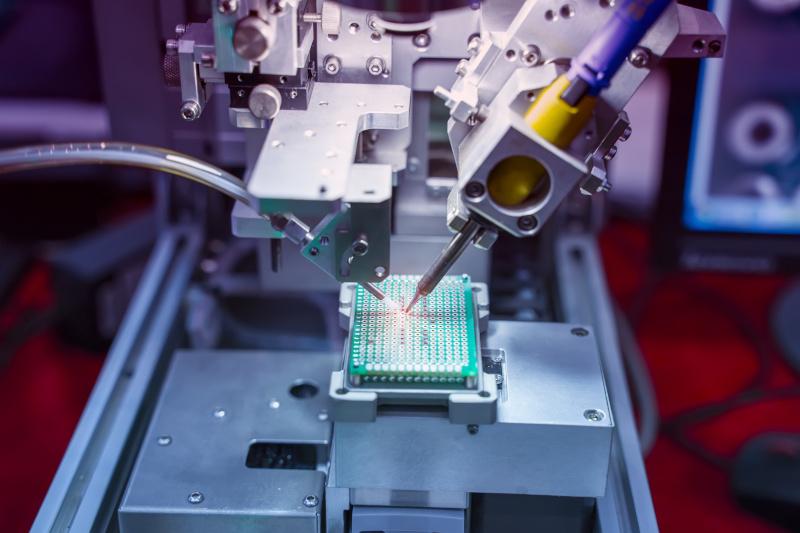
Challenges of Infrared Non-Contact Temperature Measurement in the Electronics Industry
Infrared (IR) non-contact temperature measurement presents specific challenges in the electronics industry. One primary issue is emissivity variation. Electronic components, including PCBs (Printed Circuit Boards) and circuit boards, often have diverse surface finishes and materials, each with different emissivity values. This variability requires precise calibration of IR sensors to ensure accurate temperature readings. Incorrect emissivity settings can lead to measurement errors, impacting quality control.
Thermal gradients within PCBs and circuit boards can also complicate temperature measurement. Electronic assemblies frequently experience uneven heating during soldering and component placement, leading to localized temperature differences. IR cameras must be calibrated to account for these gradients, which can be complex and require advanced technology to maintain measurement accuracy across the board.
Additionally, reflections and ambient heat from surrounding equipment can affect IR sensor performance. High ambient temperatures or reflective surfaces from nearby components can disrupt accurate readings, necessitating careful placement and shielding of IR devices to ensure reliable measurements.
Benefits of Infrared Non-Contact Temperature Measurement
Despite these challenges, IR non-contact temperature measurement offers significant benefits, particularly in enhancing quality in the electronics industry. One of the major advantages is precise component inspection. IR cameras and pyrometers provide real-time temperature monitoring during critical processes such as soldering and reflow. Accurate temperature control helps prevent defects like thermal damage, solder joint failures, and warping, ensuring the reliability and longevity of electronic components.
In PCB manufacturing, IR measurement improves quality control by allowing for detailed thermal profiling during the assembly and soldering stages. Proper temperature management helps achieve optimal solder flow and prevents issues such as cold solder joints or overheating of sensitive components, thus maintaining the integrity of the circuit boards.
Enhanced process efficiency is another benefit. IR technology enables manufacturers to monitor and adjust heating and cooling processes in real-time, reducing energy consumption and operational costs. By optimizing temperature profiles, manufacturers can minimize waste and improve overall production efficiency, leading to more consistent and high-quality electronics.
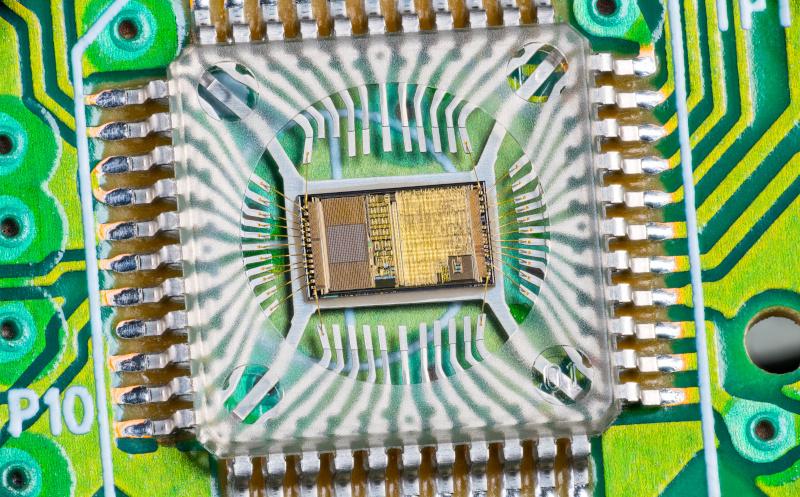
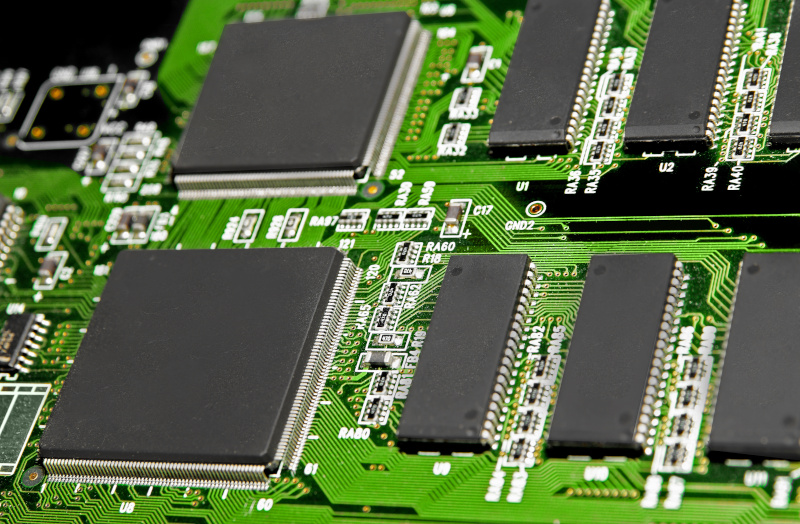
Applications and Efficiency Gains
The application of IR non-contact temperature measurement in the electronics industry leads to substantial efficiency gains. In component inspection, IR sensors help detect overheating or temperature anomalies, which can cause early failures or reduced performance. This proactive approach to thermal management ensures that components meet stringent quality standards and function reliably in their end-use applications.
For circuit boards, IR technology enhances thermal management by providing accurate temperature readings during the assembly process. This capability helps in identifying and addressing thermal issues promptly, leading to better quality control and fewer defects in finished products.
Overall, integrating IR temperature measurement into electronics production processes results in improved product quality, process optimization, and cost savings. By leveraging advanced IR technology, manufacturers can achieve more precise temperature control, enhance the reliability of their products, and support more efficient and sustainable manufacturing practices.
What Is the Right Solution for My Needs?
Click here to find the product that suits your demands.
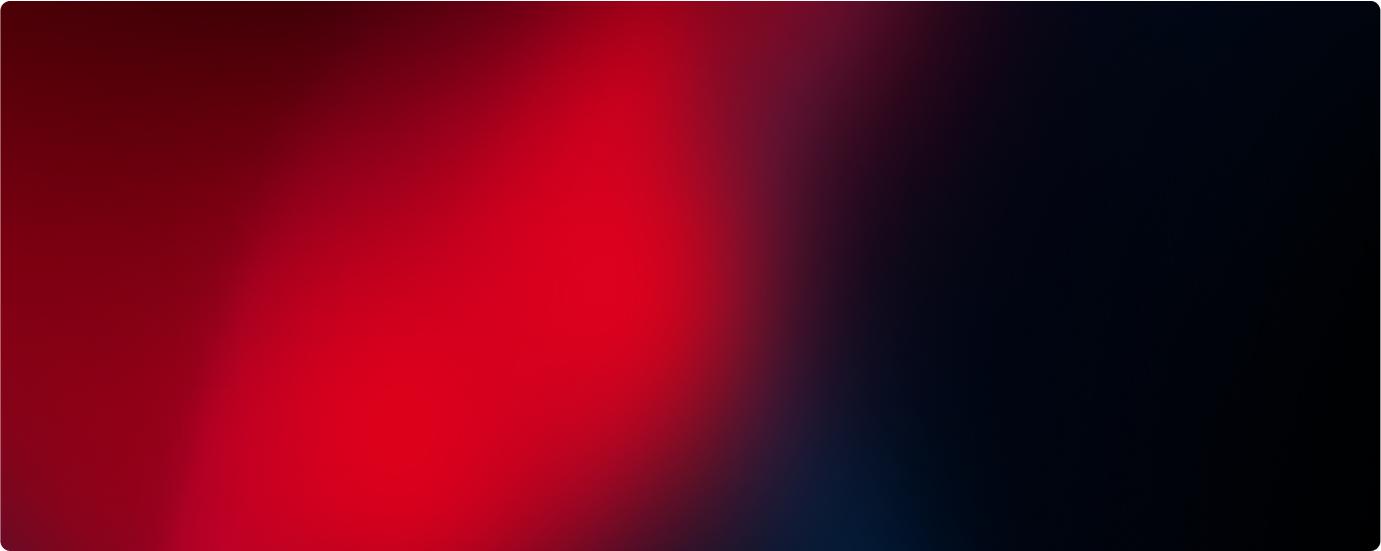
Talk to us about your IR Temperature Measurement Requirements
There are over 300 different pyrometer variants to choose from in the Optris infrared pyrometer portfolio each optimized for material, spot size, distance from the target, and environmental conditions. Fortunately, there is a trained engineer to phone or chat with to guide you through the process of choosing the perfect infrared sensor for your application.
The same support is available for the extensive IR camera product line.
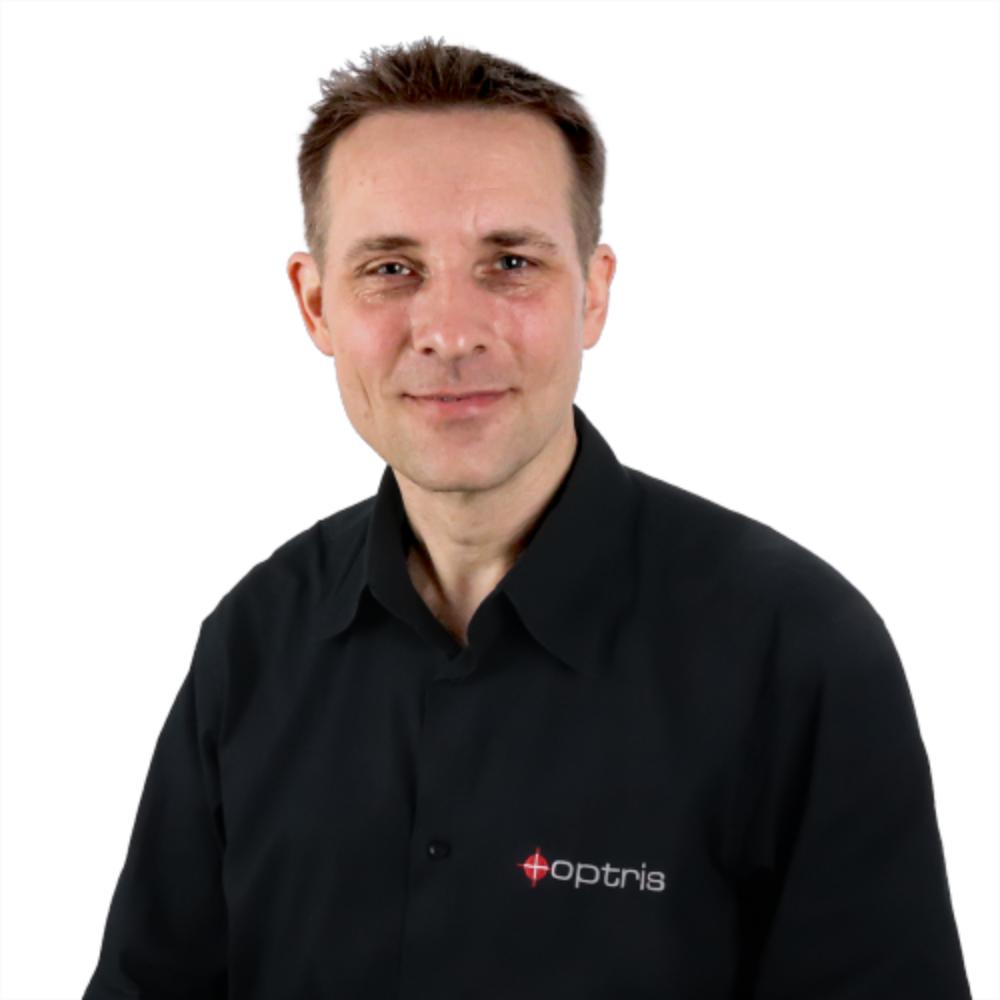