
Continuous Infrared Online Monitoring of Furnace Exit Gas Temperature
Continuous, Accurate Monitoring for Optimal Combustion Efficiency and Minimize Emissions of Boiler and Furnaces
Optimizing Combustion with Continuous Monitoring of Furnace Exit Gas Temperature
Industrial furnaces play a critical role in various applications, including metal production, chemical processing, and heat treatment. These furnaces are engineered to reach extremely high temperatures necessary to achieve specific process outcomes. The combustion process within these furnaces involves the precise mixing of fuel and air to generate heat, which is then transferred to the material being processed.
A key parameter in optimizing furnace performance and ensuring safety in industrial boilers is the Furnace Exit Gas Temperature (FEGT). FEGT directly impacts heat transfer within the furnace, influencing the efficiency of superheating and reheating processes. If FEGT is too high, it can lead to issues such as slagging, tube corrosion, and increased nitrogen oxide (NOx) emissions. Conversely, a low FEGT may indicate inefficient combustion. Therefore, accurate and reliable measurement of FEGT is essential to maintaining combustion efficiency and process balance. However, measuring FEGT accurately is challenging due to the harsh environmental conditions and the complex nature of the combustion process within industrial furnaces.
FEGT measurement provides a precise assessment of the heat transfer to the furnace water walls under specific load conditions and establishes expected performance for superheating and reheating operations. Elevated FEGT can cause fly ash to adhere to the tubes and pendants, leading to slag formation and reduced heat exchange efficiency, which may necessitate frequent soot blowing, cause tube corrosion, lower operational loads, and pose safety risks. On the other hand, a low FEGT could signal excessive radiative losses to the water walls or incomplete combustion, both of which reduce efficiency. Factors such as fuel quality, excess air, burner selection and tilt, low NOx operation, and heat transfer dynamics all influence the exit gas temperature.
Traditional FEGT measurement methods, such as thermocouples and thermal modeling, have notable limitations. These include sensitivity to local temperature variations and potential inaccuracies in extrapolating data across the furnace. This has led to the adoption of advanced infrared temperature measurement technologies, which offer a non-contact, precise solution. Unlike thermocouples, which only measure temperature at specific points—often near the furnace walls—and are susceptible to wear and damage from harsh conditions like soot and fly ash buildup, infrared pyrometers provide accurate, comprehensive measurements of gas temperature across the entire furnace. This advanced approach offers deeper insights into the overall combustion process, enhancing both accuracy and reliability.
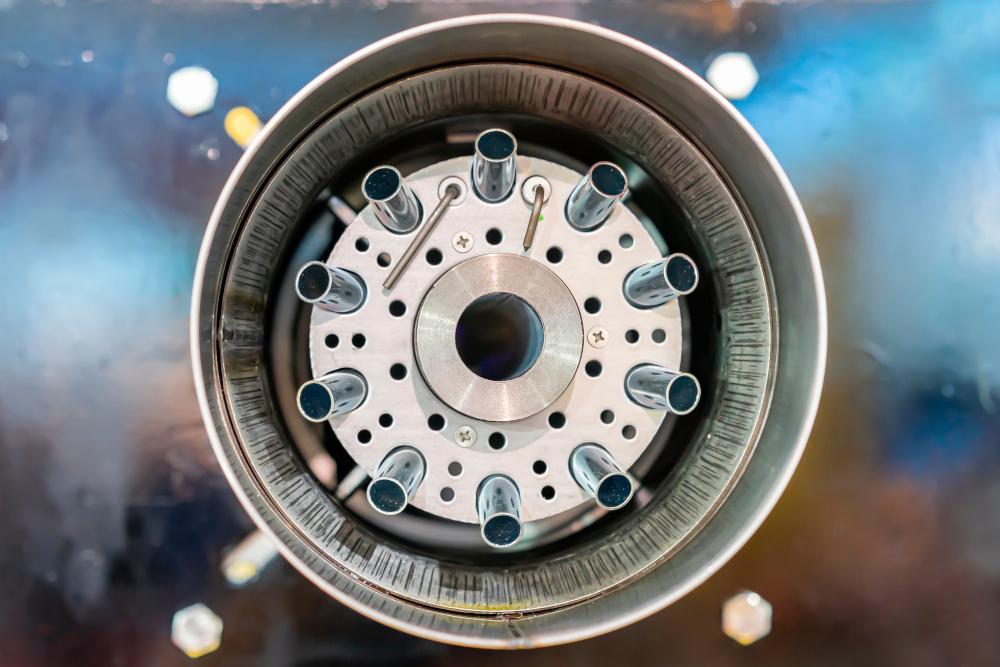
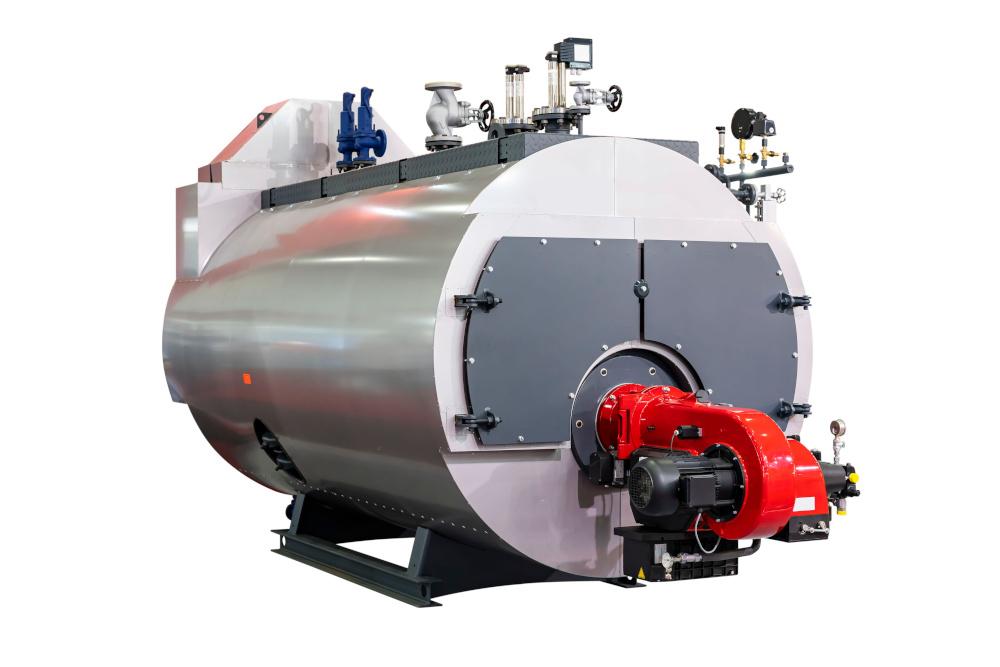
Optimizing Combustion with Infrared Pyrometry to Enhance Furnace and Boiler Efficiency
Non-contact temperature measurement methods utilize infrared radiation to assess the temperature of exhaust gases in industrial furnaces.
The Optris CTlaser F6 is a cutting-edge infrared temperature sensor specifically engineered for non-contact measurement of furnace exit gas temperature (FEGT) in industrial boilers. This advanced pyrometer is capable of measuring the temperature of carbon monoxide (CO) flame gases, which are critical indicators of combustion efficiency and potential hotspots within the furnace. It employs a thin-film thermopile and a spectral filter that selectively blocks other infrared emissions, enabling the sensor to detect CO infrared energy with high sensitivity. This capability allows for direct and precise temperature measurement of CO gas within the sensor’s field of view.
The CTlaser F6 operates within a spectral range of 4.6 μm, which is specifically optimized for CO gas detection. This wavelength corresponds to the absorption band of carbon monoxide in the infrared spectrum, making it ideal for measuring CO gas temperatures. Infrared pyrometers like the Optris CTlaser F6 are designed to detect specific gases by targeting these unique absorption bands. At the 4.6 μm wavelength, the sensor is highly sensitive to the thermal radiation emitted by CO molecules in combustion gases, allowing for accurate temperature readings that are crucial for determining FEGT.
The device features a compact sensor head, a dual-laser targeting system for precise alignment, and an optical resolution of 45:1, ensuring accurate measurements even in challenging environments. The pyrometer is housed in a robust enclosure capable of withstanding ambient temperatures up to 85 °C without the need for additional cooling. For harsher conditions, optional accessories such as water cooling and air purging systems are available to further enhance durability.
Integrating the Optris CTlaser F6 into a furnace monitoring system enables continuous, real-time FEGT measurement. The device’s rapid response time of just 10 ms ensures immediate detection of temperature fluctuations, allowing operators to quickly adjust settings to maintain optimal combustion conditions. The sensor’s output data can be seamlessly integrated into existing plant control systems via both analog and digital outputs, offering flexibility in monitoring and data management.
The Optris CTlaser F6 for Precise CO Gas Temperature Measurement
Implementing the Optris CTlaser F6 for FEGT measurement offers numerous advantages for industrial boiler operators. This advanced sensor provides precise furnace exit gas temperature readings, which are crucial for optimizing combustion processes, reducing fuel consumption, and minimizing the buildup of slag and soot deposits. By maintaining FEGT within the optimal range, operators can significantly decrease the risk of tube corrosion and NOx emissions, resulting in enhanced boiler efficiency and an extended operational lifespan.
Additionally, the non-contact measurement method of the CTlaser F6 eliminates the wear and tear common with traditional thermocouples, ensuring reliable and maintenance-free operation over long periods. Continuous FEGT monitoring also generates valuable data for predictive maintenance, enabling operators to address potential issues before they escalate into costly problems.
What further sets the Optris CTlaser F6 apart is its affordable price point, which allows for redundant instrumentation of critical assets. This affordability means that operators can deploy multiple sensors across key points within the system, ensuring comprehensive monitoring and added layers of safety. By having redundancy in place, operators can confidently maintain consistent and accurate temperature readings, even if one sensor requires maintenance or replacement. This not only enhances reliability but also supports uninterrupted operation, further contributing to the overall efficiency and longevity of the boiler system.
The Optris CTlaser F6 is the preferred solution due to its robust design, high accuracy, ease of integration, and cost-effectiveness. Its ability to perform reliably in harsh environments without the need for extensive cooling or frequent maintenance, combined with the option for redundant setup, makes it an ideal choice for continuous FEGT monitoring in demanding industrial settings.
Recommended Products
Other Condition Monitoring Applications
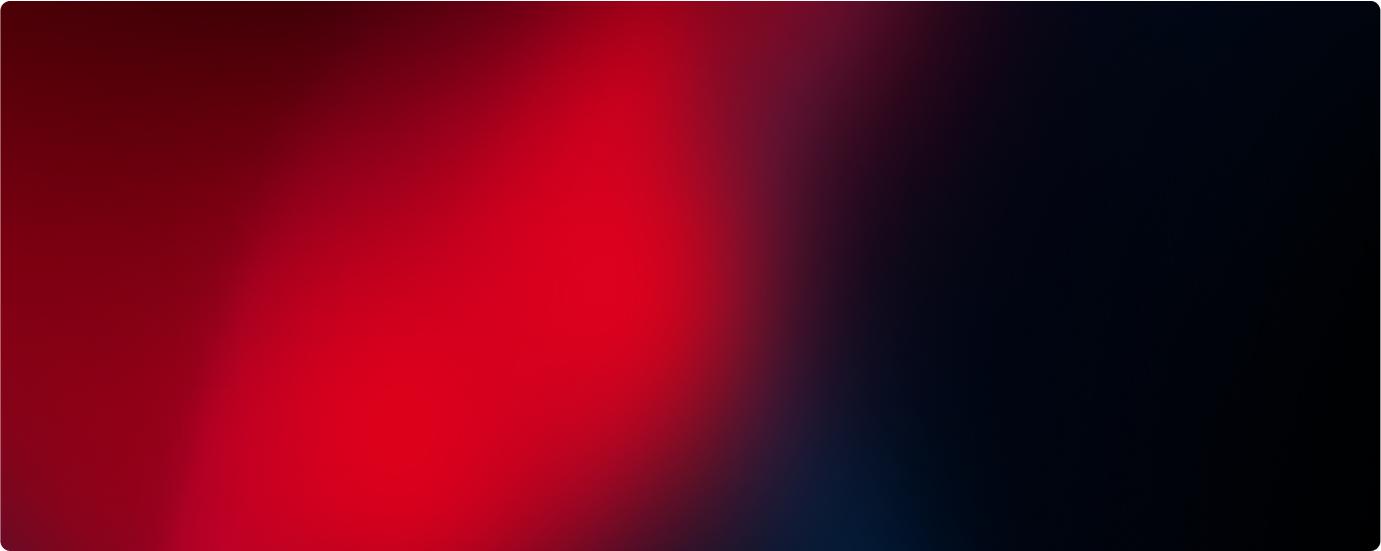
Talk to us about your IR Temperature Measurement Requirements
There are over 300 different pyrometer variants to choose from in the Optris infrared pyrometer portfolio each optimized for material, spot size, distance from the target, and environmental conditions. Fortunately, there is a trained engineer to phone or chat with to guide you through the process of choosing the perfect infrared sensor for your application.
The same support is available for the extensive IR camera product line.
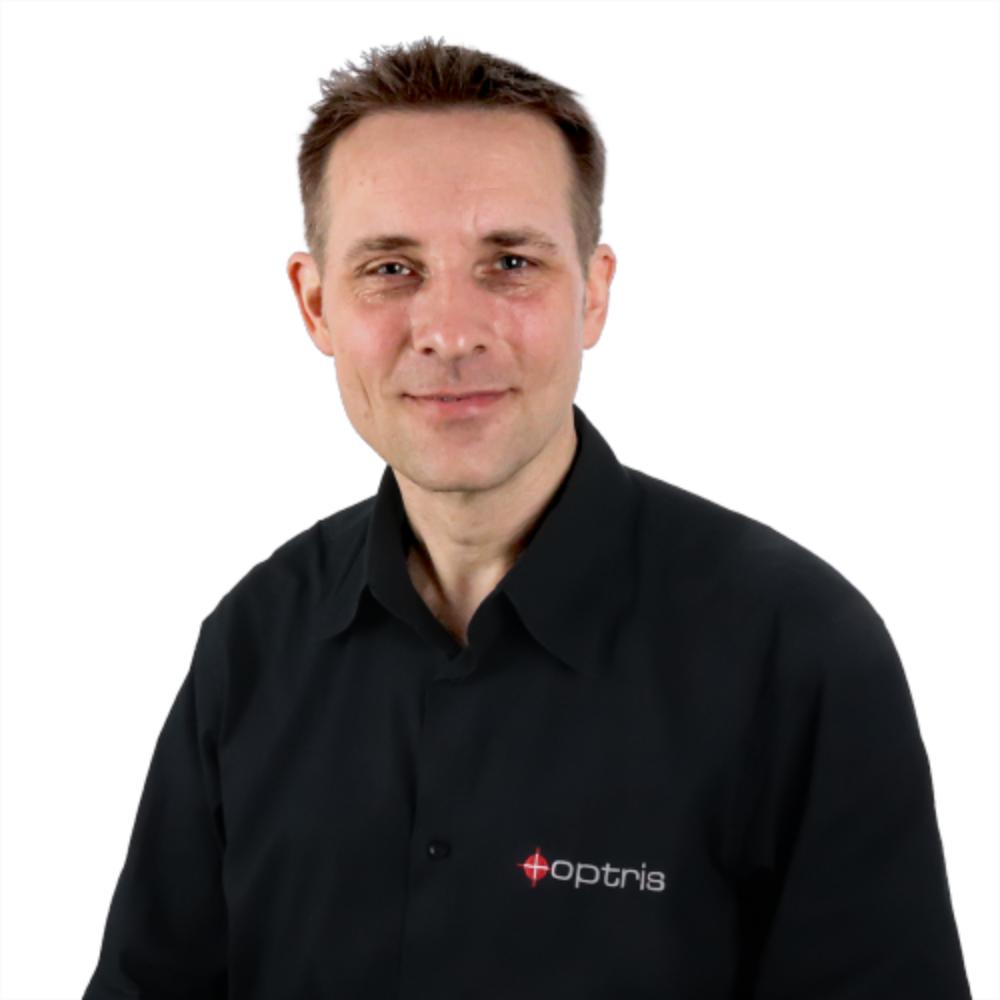