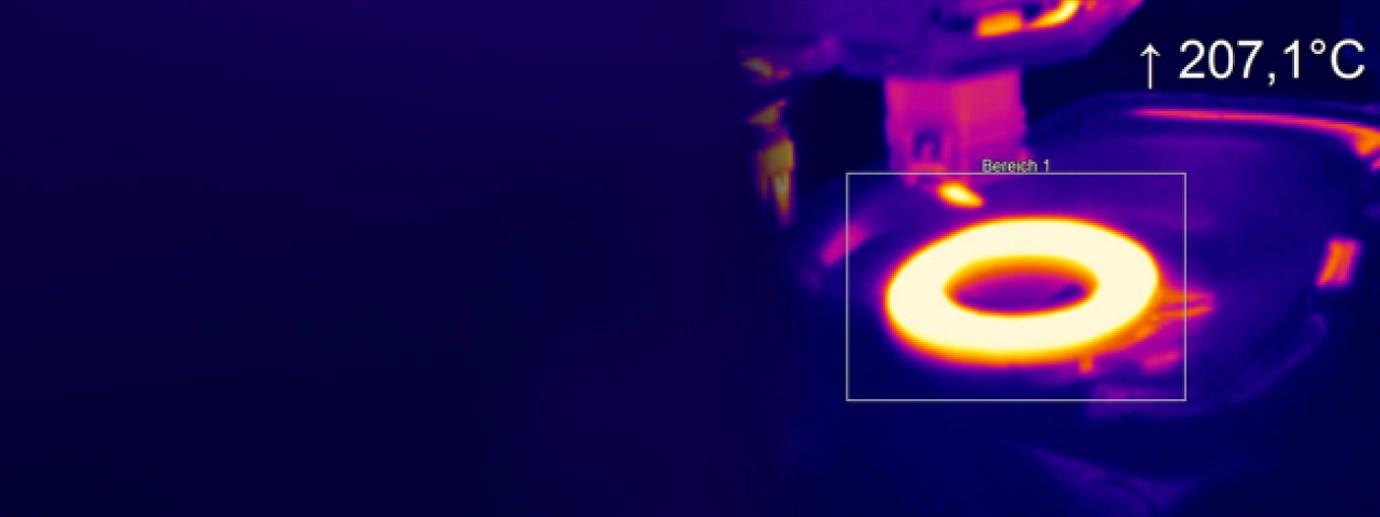
Ensuring Leak-Free Fuel Tanks through Accurate Infrared Monitoring
Ensuring Uniform Heat Distribution in Fuel Tank Welding of Plastic Fuel Tank
The Complexity of Plastic Welding in Automotive Manufacturing
In the automotive industry, the welding of plastic fuel tanks presents a unique set of challenges. The process involves attaching the tank neck to the main body of the tank through plastic welding, where the surfaces are heated using a metal contact until they reach approximately 200°C, allowing the plastic to soften and bond effectively. Achieving a seamless and strong weld is crucial to prevent leaks, which can lead to serious safety and quality issues.
Plastic welding problems often arise from issues like poor weld strength, which can be caused by improper surface preparation, incorrect welding temperature, or inadequate pressure. Warping or distortion may occur due to uneven heating or excessive pressure, while cracking or splitting often results from improper temperature control or poor surface preparation. Discoloration is another issue, typically caused by using too high a welding temperature or exposure to heat and UV radiation.
Traditional methods involving spot contact temperature sensors for temperature control during the welding process often fail to ensure uniform heating across the entire welding area, leading to potential weak spots and the risk of leakage. The plastic welding method requires precise temperature management to avoid underheating the bonding area, as otherwise, rework is necessary or the parts need to be scraped.
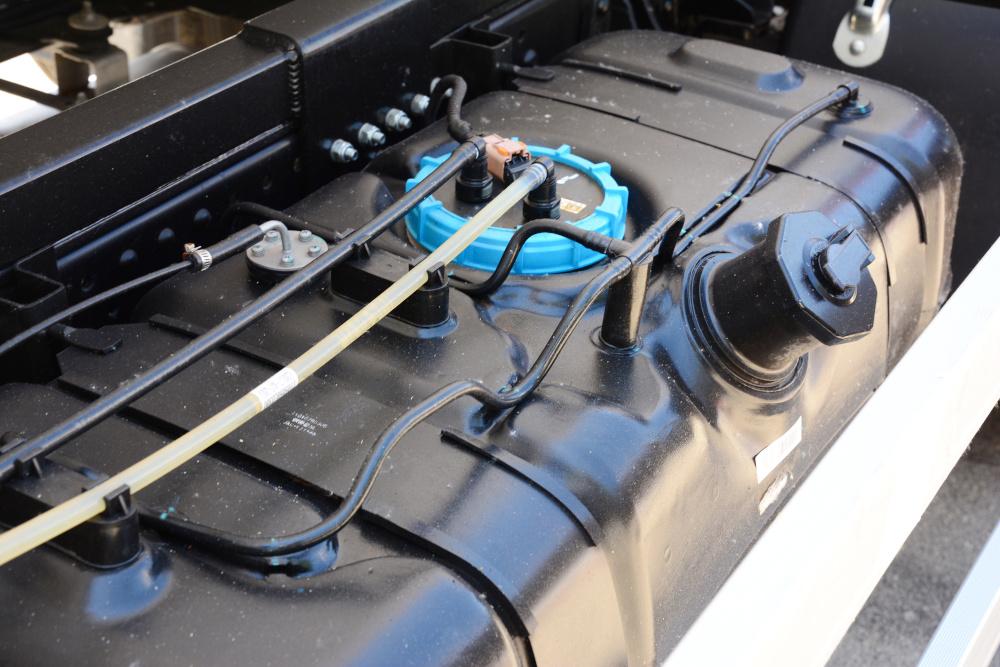
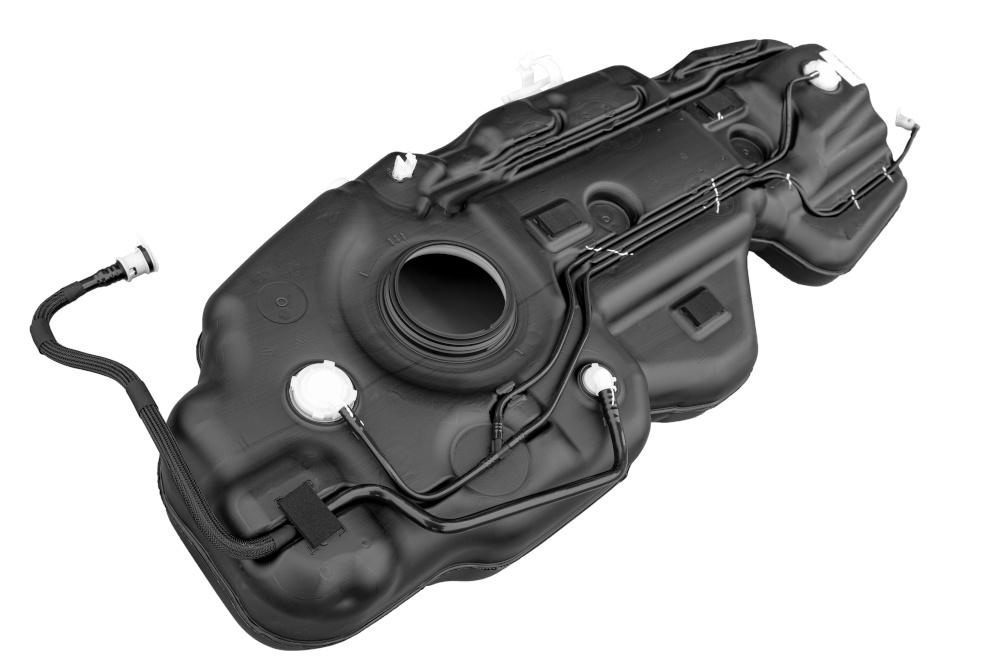
Integrating Infrared Measurement Systems into Automotive Welding Lines
The key motivation for employing infrared temperature measurement lies in its ability to monitor the entire welding surface, ensuring the necessary temperature is uniformly achieved across the bond area.
Infrared cameras provide a significant advantage in this context by allowing real-time, non-contact temperature monitoring of the welding process. Unlike traditional point measurement systems like pyrometers, which can only measure specific spots, infrared cameras capture the temperature distribution across the entire welding surface. This ensures that every part of the weld is heated to the correct temperature, thus minimizing the risk of defects.
Optris offers advanced infrared camera solutions to address the challenges associated with plastic welding in fuel tank manufacturing.
In application with a car manufacturer, these thermal cameras are integrated into an assembly line. They are strategically positioned to monitor the critical areas of the welding process, particularly the circular opening where the tank neck is attached. The process is managed by integrating Optris thermal imaging technology into the existing production line, ensuring precise and real-time monitoring of temperature distribution.
One of the key advantages of Optris infrared cameras is their high accuracy and ability to cover the entire welding surface, a capability that traditional pyrometers lack. Operating within the optimal spectral range of 8 to 14 micrometers, these infrared cameras are ideal for capturing the temperature of plastic surfaces. They are seamlessly integrated into the production line’s control system via the Optris SDK, enabling smooth data communication and precise process control.
The system triggers temperature measurement at the precise moment when the heating tool is retracted from the tank surface, ensuring that the welding temperature is both adequate and uniform. This integration is crucial for automating the quality assurance process, reducing manual intervention, and ensuring that the welding process consistently meets the required standards.
Unique Advantages of Optris Infrared Technology
The implementation of Optris infrared cameras in plastic fuel tank welding has resulted in significant benefits for the customer. The primary advantage is the substantial reduction in welding defects, which translates directly into fewer product recalls and a lower rate of rejected parts. By ensuring that the entire welding surface reaches the correct temperature, the risk of leaks is minimized, leading to higher overall product quality.
Moreover, the use of thermal imaging allows for a more efficient manufacturing process, as it reduces the need for rework and manual inspection. This not only saves time and resources but also increases the reliability of the welding process. The customer has also appreciated the ease of integration of Optris solutions, which require minimal modifications to the existing production line.
Optris stands out as the preferred partner in this application due to its reliable infrared technology, ease of integration, and cost-effectiveness. The unique selling points of the Optris solution include the comprehensive coverage provided by the infrared cameras, the precision of temperature measurement, and the robustness of the system in demanding industrial environments. These factors make Optris the ideal choice for manufacturers looking to enhance the quality and reliability of their plastic welding processes.
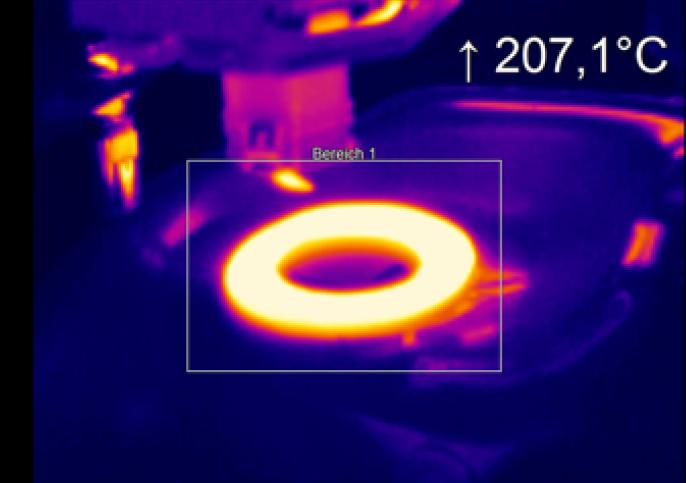
Recommended Products
Other Automotive Applications
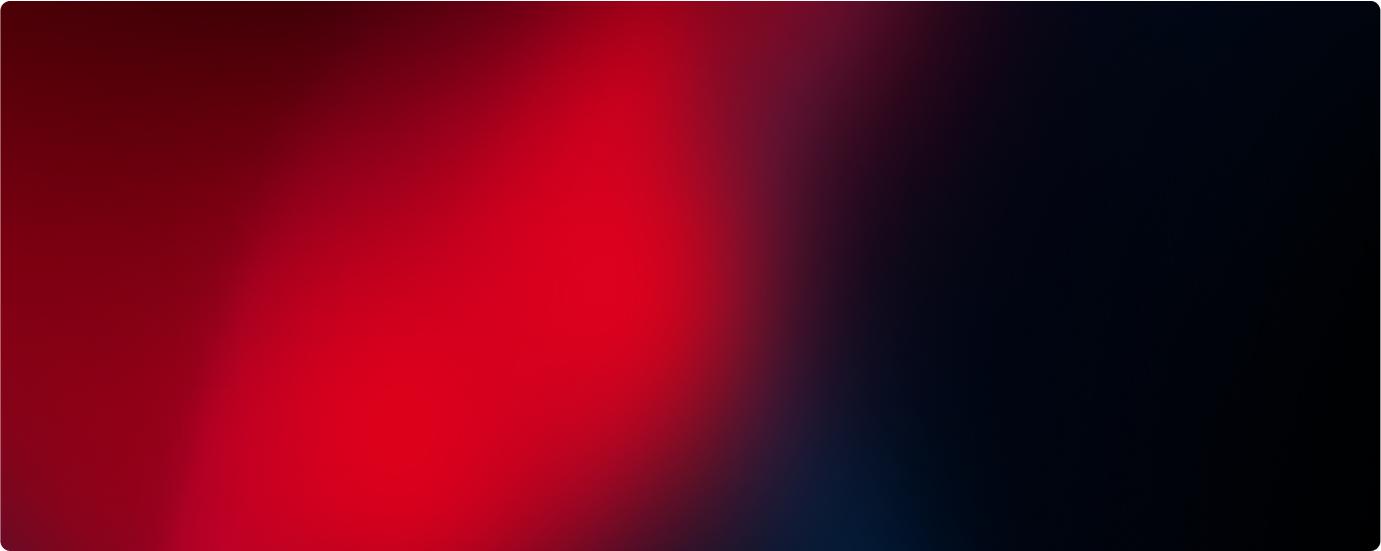
Talk to us about your IR Temperature Measurement Requirements
There are over 300 different pyrometer variants to choose from in the Optris infrared pyrometer portfolio each optimized for material, spot size, distance from the target, and environmental conditions. Fortunately, there is a trained engineer to phone or chat with to guide you through the process of choosing the perfect infrared sensor for your application.
The same support is available for the extensive IR camera product line.
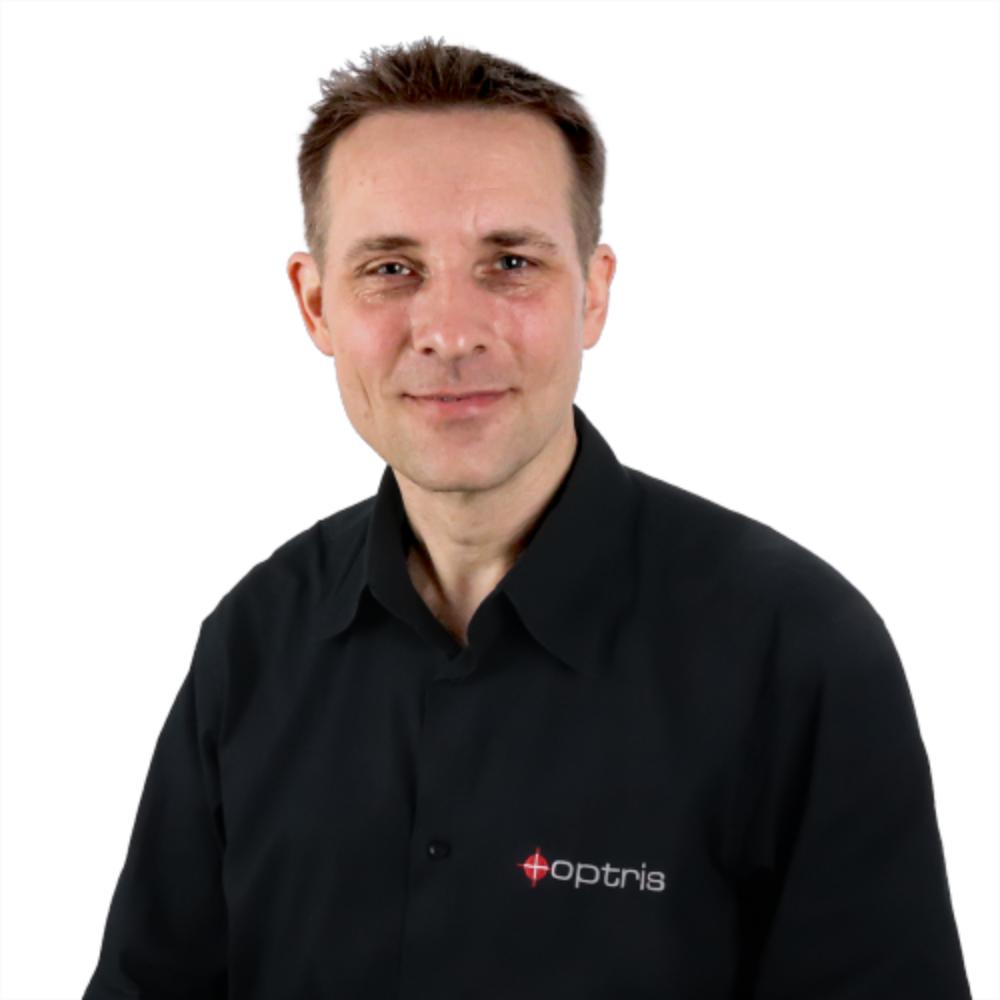