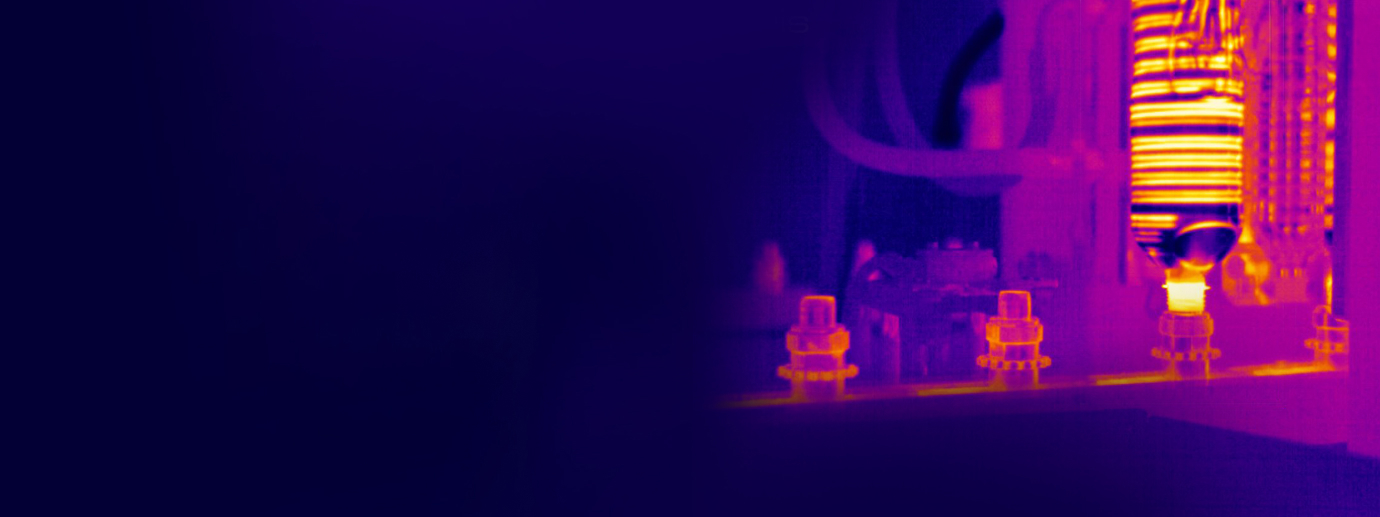
Advanced Thermal Measurement Solutions for Fast Plastic Molding Processes
Ensuring Consistent Plastic Thickness with Infrared Pyrometer Technology
High-Speed Manufacturing and the Risk of Temperature Deviations
The Injection Stretch Blow Molding process is a widely used method for manufacturing plastic containers, especially PET bottles. This process typically involves two stages. In the first stage, called injection molding, plastic preforms are created. These preforms resemble thick-walled plastic tubes with one open end that usually already includes the bottle’s threaded neck for the cap. In the second stage, known as stretch blow molding, the preform is heated and then stretched and blown into its final shape inside a mold using compressed air.
Temperature control is critical during the heating of the preform. The preform must reach a specific temperature to soften appropriately, allowing it to be blown evenly into the mold. If the temperature is too low, the material may not stretch correctly, resulting in uneven wall thickness or incomplete formation. Conversely, if the preform is overheated, the material may become too thin, leading to weak spots in the bottle. Both scenarios can lead to quality issues, such as bottles that fail to meet structural standards or are prone to leakage during use.
Given the high speed of modern production lines, where hundreds or thousands of bottles are produced in a short period, precise and fast temperature measurement is essential to ensure product consistency and quality. Infrared temperature sensors provide a reliable solution for monitoring and controlling the preform heating process, ensuring uniform temperature distribution and reducing the risk of production defects.
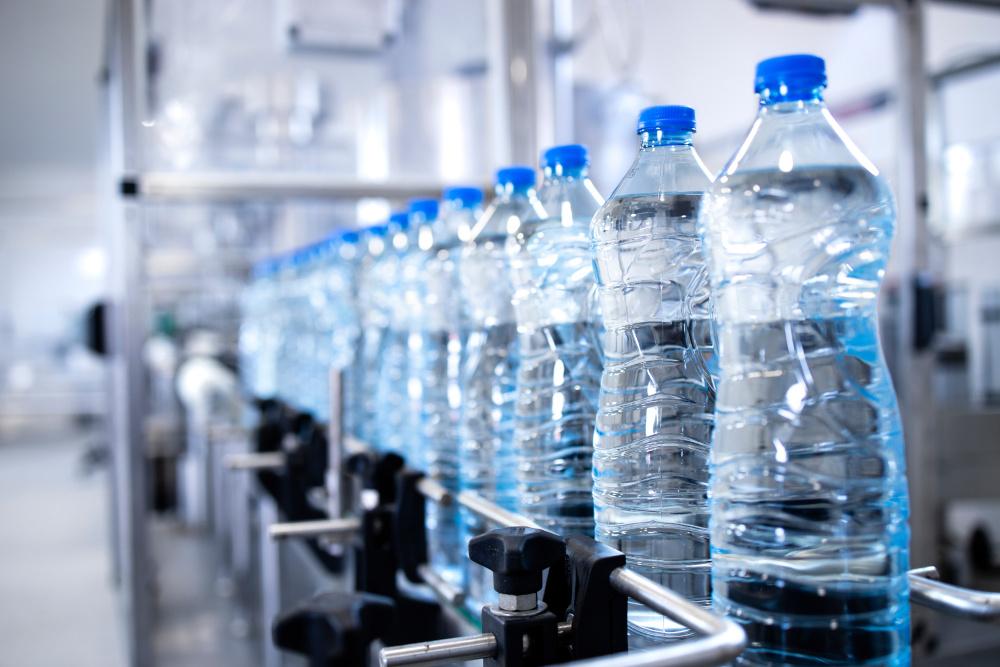
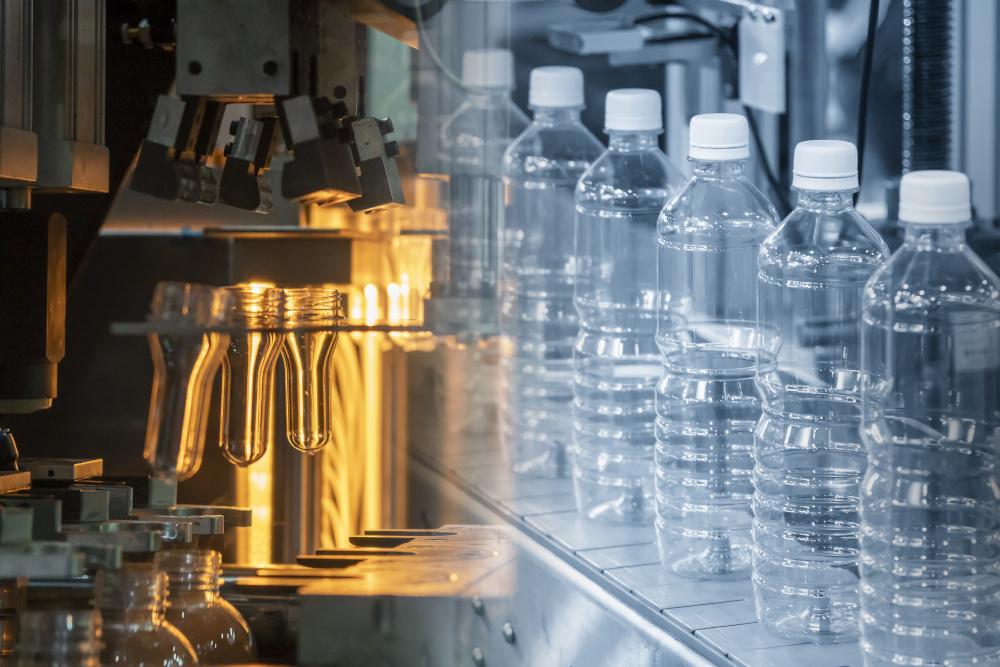
Integrating Infrared Sensors into High-Speed Molding Machines
In the Injection Stretch Blow Molding process, the infrared pyrometers CTfast and CT 4M are essential for precise temperature control. These sensors are strategically mounted to monitor the temperature of preforms as they are heated before entering the mold. The CTfast offers an ultra-fast response time of just 6 milliseconds, which is crucial for high-speed production lines. With a temperature range from –50 °C to 975 °C, the CTfast can detect even the slightest temperature deviations, ensuring consistency in bottle production.
The CT 4M provides an even faster response time of 90 microseconds and measures temperatures from 0 °C to 500 °C. Its compact design, with a sensing head only 14 mm in diameter, allows it to fit into tight spaces within the machine. Its spectral range of 2.2 to 6 µm makes it ideal for materials like plastic, which may have varying emissivity, ensuring accurate temperature readings.
Both pyrometers deliver real-time data that can be integrated directly into the machine’s control system via interfaces such as Modbus TCP or Ethernet IP. This allows for automatic adjustments in the heating process when temperatures deviate from the optimal range. Their high-speed measurement capabilities and reliability help maximize production output while maintaining the quality of the plastic bottles being manufactured.
The Advantages of Compact, Fast-Response Infrared Sensors
The integration of Optris pyrometers, particularly the CTfast and CT 4M models, into the Injection Stretch Blow Molding process yields substantial benefits for manufacturers. One of the most significant advantages is the improvement in product quality. With the real-time monitoring of preform temperatures, manufacturers can ensure that each preform is heated uniformly and accurately. This reduces the occurrence of defects such as inconsistent wall thickness or weak spots, leading to more robust plastic bottles that meet both aesthetic and functional standards.
Another key benefit is the increase in production efficiency. The high-speed response times of the CTfast and CT 4M allow for precise temperature measurements even in fast-moving production lines. This capability minimizes the risk of temperature-related issues causing production delays or leading to high levels of defective products. By maintaining optimal temperatures throughout the molding process, manufacturers can maximize their output while minimizing waste. In particular, the CTfast’s ability to respond within 6 milliseconds ensures that even the slightest temperature fluctuations can be detected and corrected immediately. Similarly, the CT 4M’s rapid 90 ms response time ensures that no temperature variation goes unnoticed, allowing for swift adjustments that keep the production process running smoothly.
In addition to improving quality and efficiency, the compact design of these pyrometers is a significant advantage for manufacturers. The small size of the CTfast and CT 4M sensing heads allows them to be installed in tight spaces within the molding machines, ensuring that they do not interfere with other machine components. This flexibility in installation is complemented by the robust construction of the pyrometers, which can withstand the demanding conditions of a high-temperature, high-speed production environment.
Optris infrared pyrometers also offer a high degree of customization and adaptability. With features like adjustable emissivity and multiple interface options, these devices can be easily integrated into various control systems, making them versatile tools for a wide range of industrial applications. Their ability to measure temperature without direct contact ensures that they remain reliable and accurate over time, reducing maintenance costs and extending the lifespan of the equipment.

Recommended Products
Other Plastic Applications
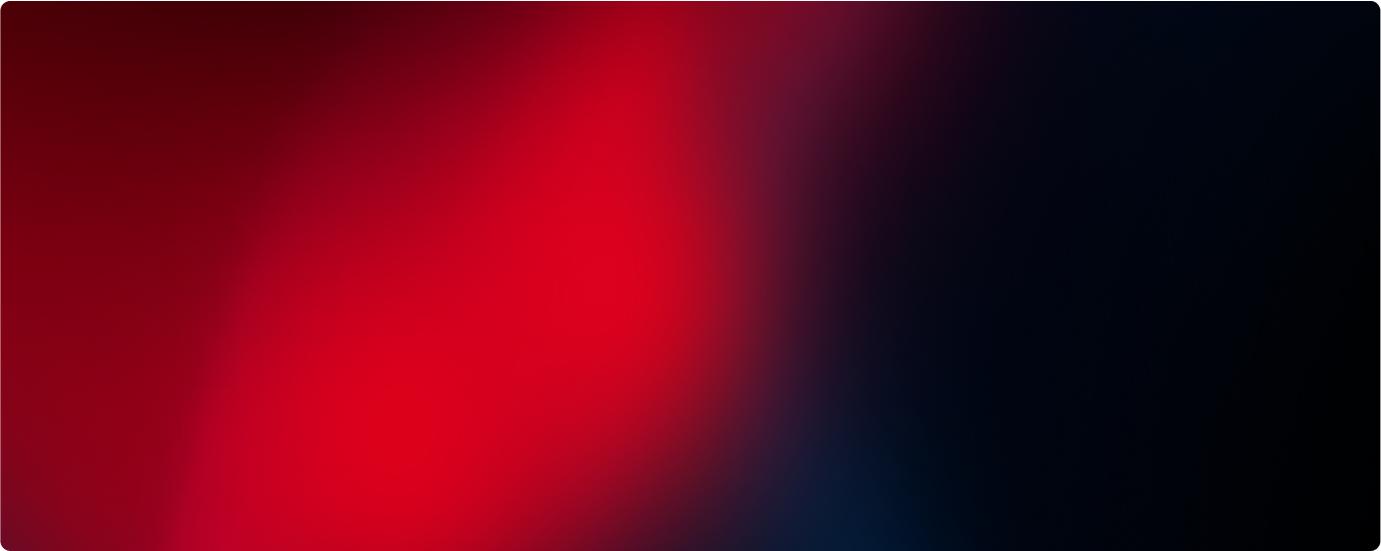
Talk to us about your IR Temperature Measurement Requirements
There are over 300 different pyrometer variants to choose from in the Optris infrared pyrometer portfolio each optimized for material, spot size, distance from the target, and environmental conditions. Fortunately, there is a trained engineer to phone or chat with to guide you through the process of choosing the perfect infrared sensor for your application.
The same support is available for the extensive IR camera product line.
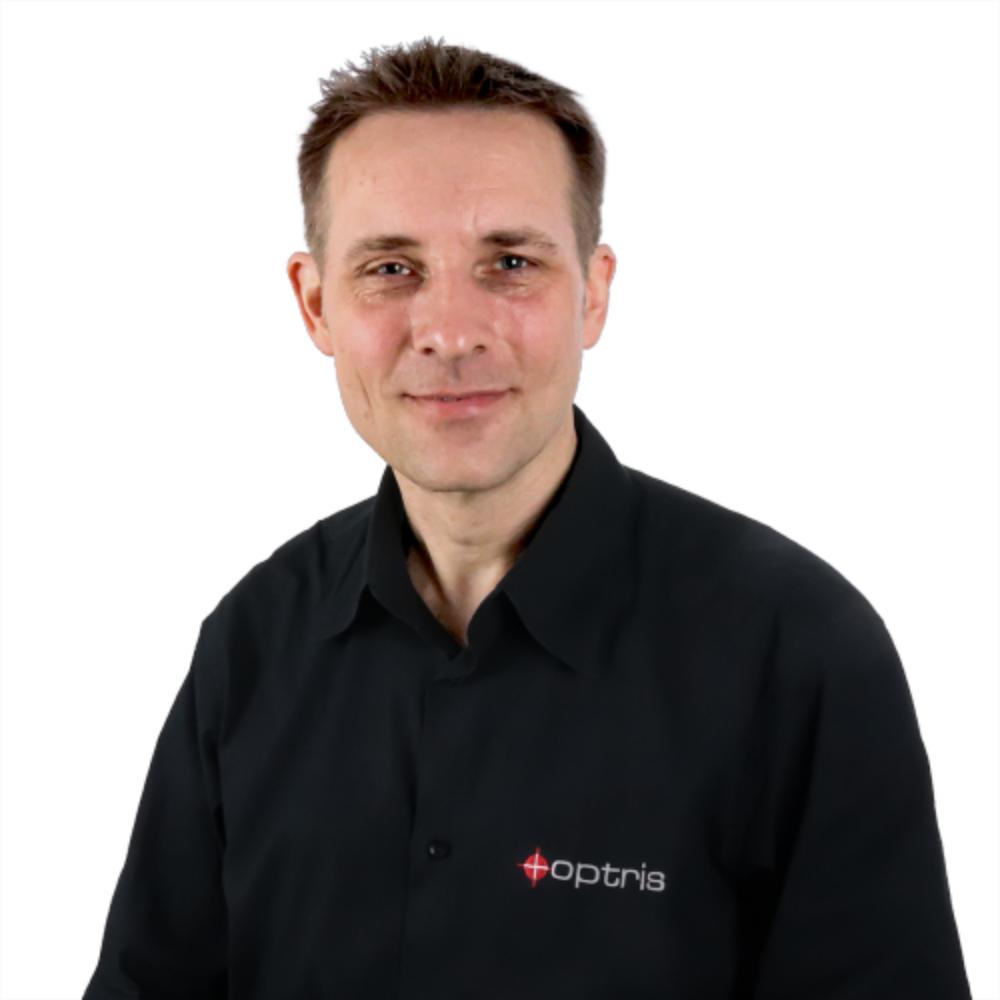