
Improving Mouthguard Production with Infrared Temperature Sensors
Optimizing Dental Thermoforming with Non-Contact Temperature Sensing
Temperature Control for Perfect Fit and Durability in Dental Thermoforming
Dental thermoforming machines are essential for creating custom dental appliances like retainers, mouthguards, and aligners. These machines use heat and vacuum pressure to mold thermoplastic sheets precisely to the contours of a dental model, replicating the patient’s teeth.
The process starts with a dental model, often produced using a 3D printer, which serves as a template for shaping the thermoplastic material. A sheet of thermoplastic, typically made from materials like polycarbonate or EVA (ethylene vinyl acetate), is selected for its thickness and flexibility. The sheet is then clamped into the thermoforming machine.
The machine heats the thermoplastic sheet to a precise temperature, making it soft and malleable. This step is critical: if the material is overheated, it can degrade or become too soft, compromising the appliance’s fit and mechanical properties. If underheated, the material may not conform well to the dental model, resulting in a poor fit.
Temperature control is, therefore, vital to the thermoforming process. Consistent heating ensures uniform quality across production cycles, preventing issues like local burning, crack formation, and material degradation. Accurate temperature sensing helps preserve the thermoplastic’s intended characteristics—flexibility, strength, and transparency—ensuring that the final dental appliance is both durable and comfortable for the patient.
This precision in temperature management directly influences the effectiveness and comfort of the dental appliances, making it a key factor in the success of the thermoforming process.
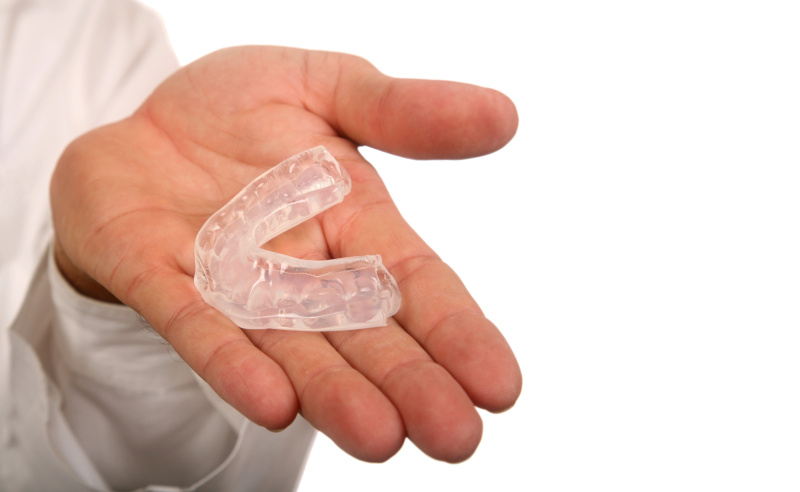
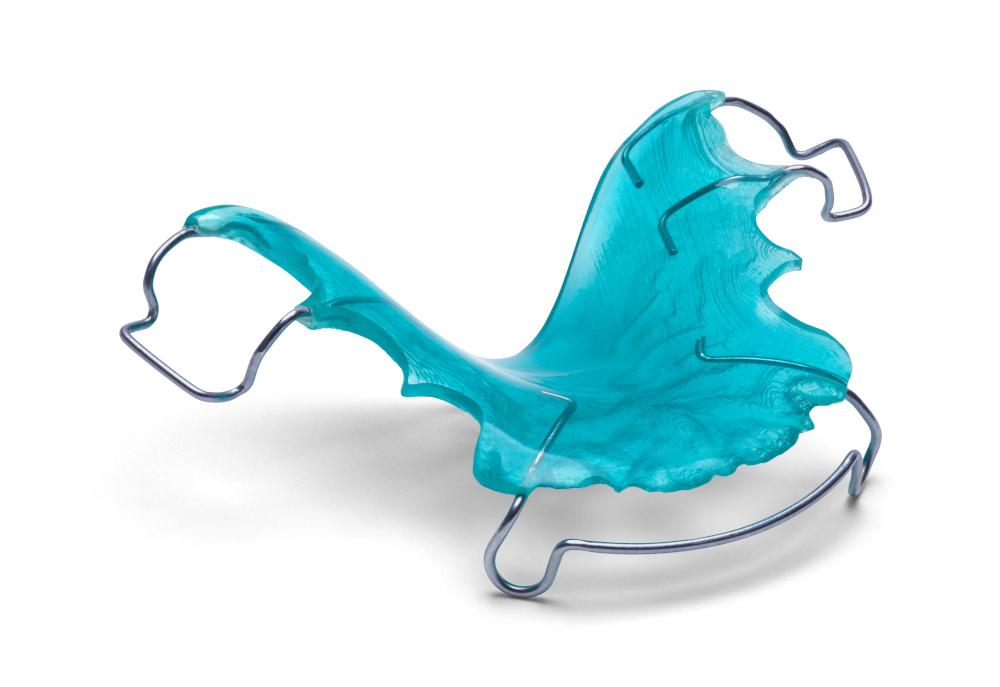
How Infrared Technology Improves Dental Mouthguard Production to Achieve Perfect Fit
A manufacturer specializing in thermoforming units for dental laboratories produces custom-fitted mouthpieces, commonly used for sports protection. These units utilize infrared radiators to heat plastic foil to a precise temperature before forming the mouthpiece, ensuring thermal uniformity. Consistent temperature distribution across the surface and accurate control of the reforming temperature are essential for achieving high-quality results.
Infrared non-contact temperature sensors are highly advantageous in medical equipment, particularly in dental thermoforming devices. Traditionally, these devices relied on contact sensors placed near the infrared radiator to measure temperature, often leading to discrepancies between the radiator’s temperature and that of the plastic sheet. To improve the accuracy of mouthguard fittings, a medical company has adopted non-contact temperature measurement techniques. The Optris CS LT pyrometer, positioned beneath the infrared heater, directly measures the temperature of the foil during heating. This precise measurement allows the heating process to stop exactly when the desired temperature is reached, initiating the thermoforming process.
In this application, the infrared heater operates in the short-wavelength infrared spectrum, while the Optris CS LT pyrometer measures in a different spectral band, preventing interference and ensuring accurate temperature readings.
The ideal heating temperature for fabricating mouthguards from ethylene vinyl acetate sheets ranges between 110 °C and 230 °C. Once the sheet reaches the appropriate temperature, it is vacuum-formed on dental models, ensuring a secure and comfortable fit.
Optris Infrared Pyrometer for Medical Machinery Offers Superior Precision and Affordability
The Optris CS LT pyrometer delivers precise temperature readings without direct contact with the material, making it ideal for measuring thermoplastic sheets while eliminating the risk of contamination. Its compact and robust design ensures easy integration into various setups, including space-constrained environments. With a fast response time, the CS LT swiftly captures temperature changes, which is critical for processes requiring real-time monitoring and control, such as the heating phase in thermoforming. The pyrometer’s compatibility with both analog and digital outputs allows seamless integration into any machinery, enhancing flexibility across different applications. Additionally, the CS LT can operate in environments up to 80 °C (176 °F) without additional cooling, a vital feature when dealing with the high heat generated by infrared radiators.
The CS LT pyrometer is not only reliable but also offers an exceptional price-performance ratio, making it an ideal choice for serial integration in medical and industrial equipment. Its affordability does not compromise its quality, as it consistently delivers accurate, non-contact temperature measurements. This cost-effective solution is particularly advantageous for production lines requiring multiple units, balancing high performance with budget constraints. Furthermore, the CS LT comes fully calibrated, ensuring accurate readings immediately upon installation, simplifying the integration process, and reducing setup time. This combination of quality, value, and ease of use makes the CS LT a top choice for manufacturers.
Recommended Products
Other Pharmaceutical & Medical Applications
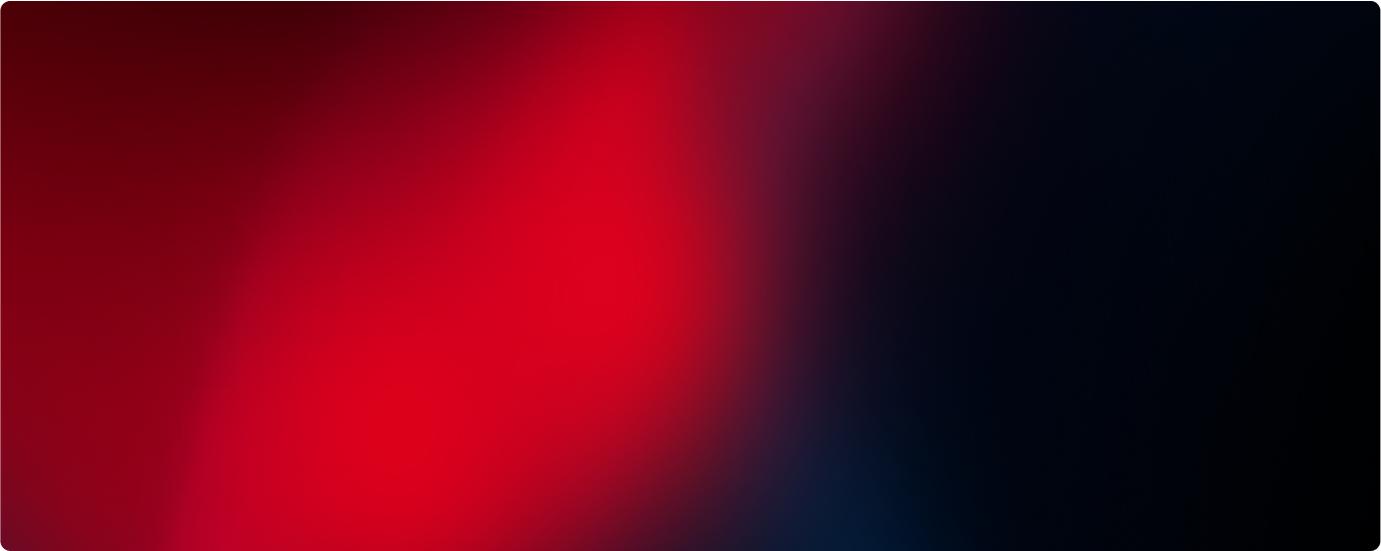
Talk to us about your IR Temperature Measurement Requirements
There are over 300 different pyrometer variants to choose from in the Optris infrared pyrometer portfolio each optimized for material, spot size, distance from the target, and environmental conditions. Fortunately, there is a trained engineer to phone or chat with to guide you through the process of choosing the perfect infrared sensor for your application.
The same support is available for the extensive IR camera product line.
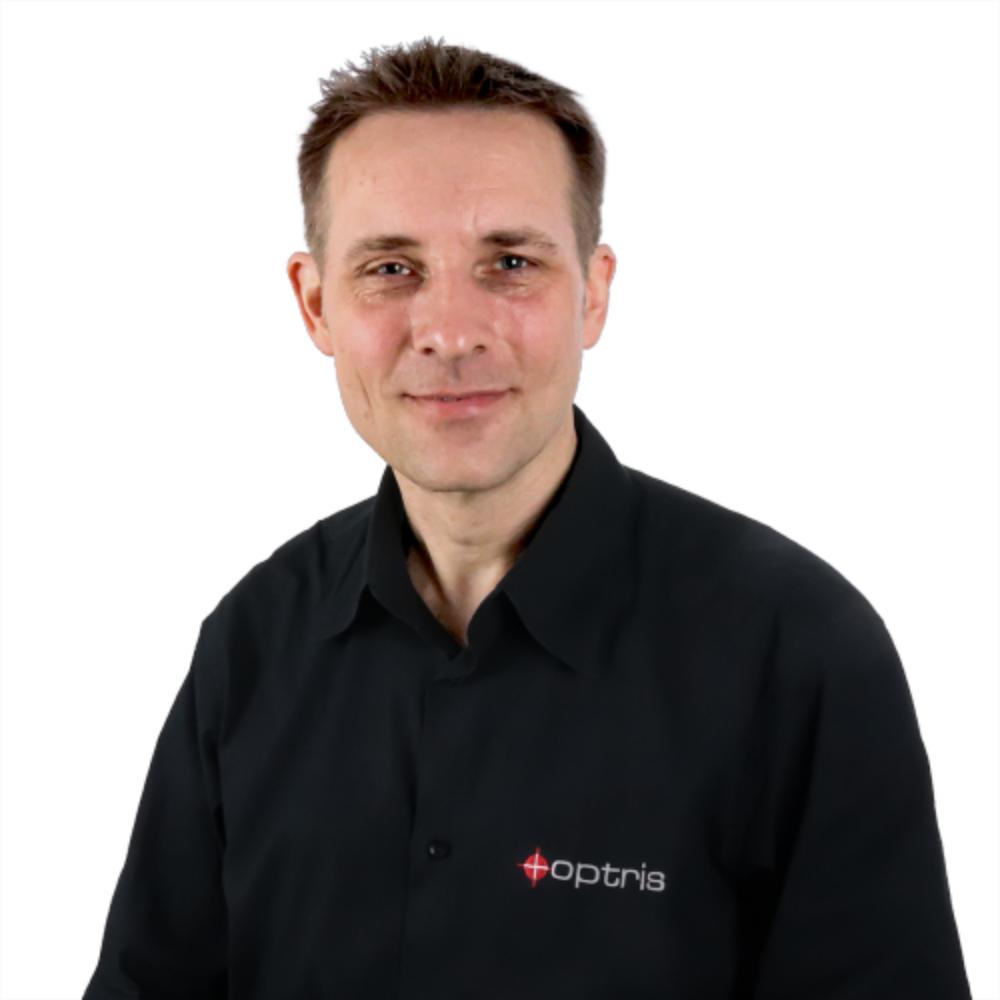