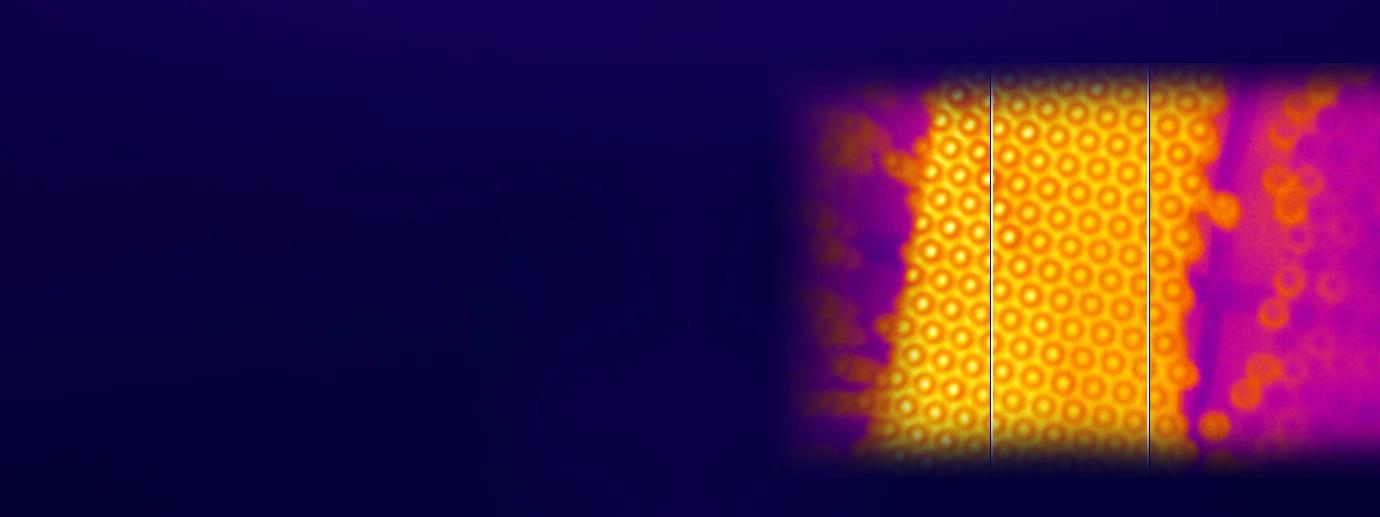
Non-contact Infrared Precision for Cold Chains within Medical Filling Process
Infrared Sensors for Pharmaceutical Products, Medications and Vaccine
The Need of Non-contact Temperature Control in Pharmaceutical Cold Chains
Pharmaceutical products must adhere to stringent production standards, requiring precise and reliable measurement methods. Monitoring the pharmaceutical cold chain involves maintaining specific temperature conditions throughout the journey of these products from origin to destination. This process is crucial for preserving the quality, effectiveness, and safety of temperature-sensitive medications, vaccines, and biologics, which can become ineffective or harmful if exposed to improper temperatures. The Medicines and Healthcare Products Regulatory Agency (MHRA) reports that nearly one-third of critical and major deficiencies in the storage and transport of medicines relate to temperature control and monitoring, with temperature issues accounting for 30% of deficiencies, surpassing other quality management and documentation failures. This concern applies to medicines requiring low-temperature storage (cold chain products) and those that must be stored below 25 °C (temperate chain products). Temperature monitoring enables companies to identify and manage shipments affected by temperature breaches.
Conventional temperature sensors are often used to monitor the ambient temperature in which biomedical products are processed, stored, or shipped. However, infrared imaging reveals that thermal gradients can exist between a temperature sensor and a product, even when not in contact. Monitoring each pharmaceutical product individually with contact temperature sensors is impractical due to the risk of contamination and the nature of the application. Non-contact infrared temperature sensors offer a solution by accurately measuring each pharmaceutical’s true temperature without the risk of contamination.
Deviations from recommended temperature ranges can compromise the chemical composition, stability, and efficacy of temperature-sensitive medications and vaccines. For safety and quality, in this application, vaccine vials must be cooled to a maximum of 25 °C after disinfection and before the filling process. If the glass temperature exceeds 25 °C, the vaccine becomes unusable due to its thermal sensitivity. Therefore, maintaining an ambient temperature below 25 °C is essential, as any pharmaceutical product filled into a glass container that has undergone high-temperature thermal disinfection will be destroyed if not adequately cooled.
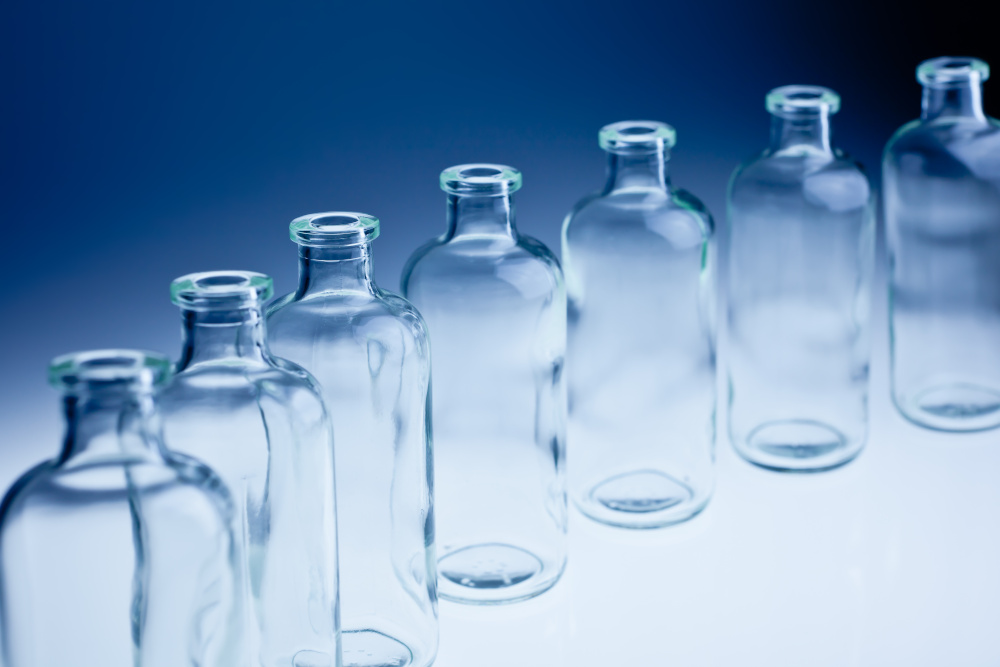
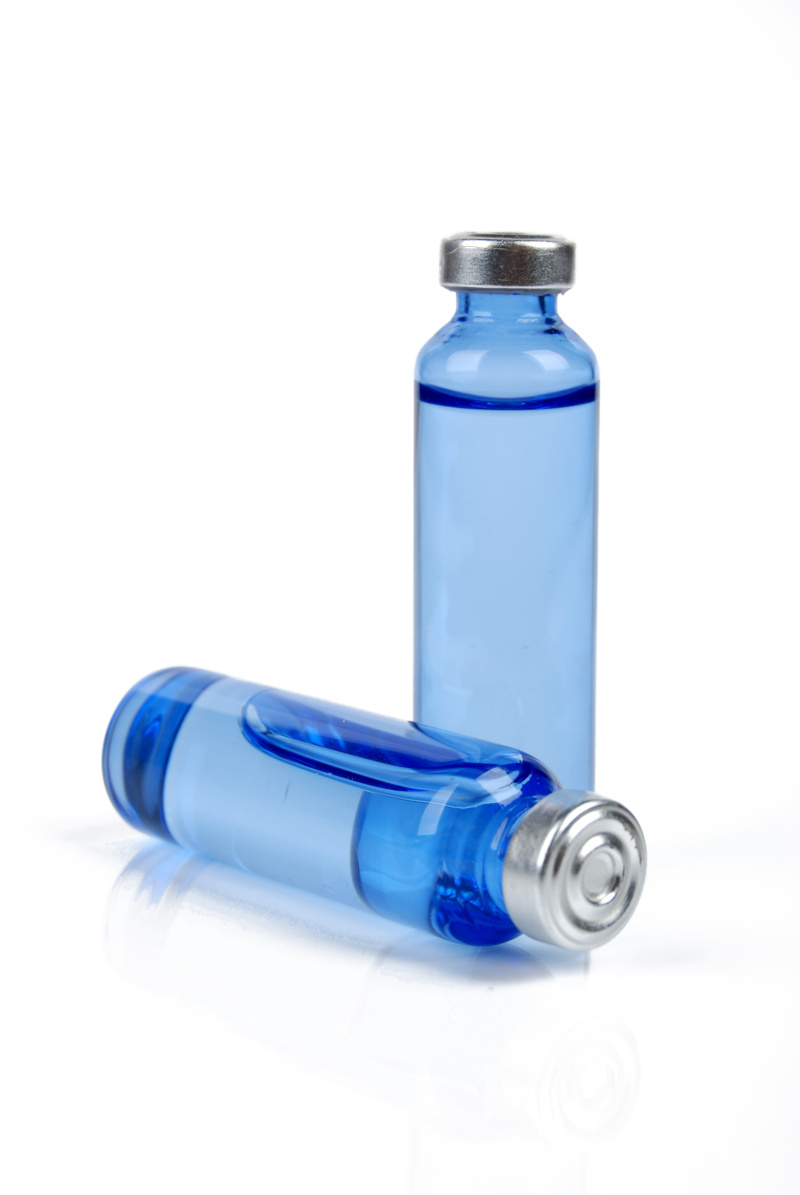
From Disinfection to Filling: Maintaining Safe Temperatures on Biomedical Products with Infrared
The filling containers are made of glass. After being thermally treated for disinfection, they are transported on a conveyor belt. Therefore, the temperature of the containers must be checked to ensure that a specific thermal threshold is reached and sufficient disinfection is achieved. After this disinfection, the glass containers are too hot to be filled directly with the temperature-sensitive biomedical product. The glass containers are cooling down on the conveyor belt while moving to the filling station. If the conveyor belt runs too fast or the thermal disinfection is set to very high temperatures, the glass container must be stopped to allow more time to cool down.
The temperature monitoring of the glass container is straightforward. The emissivity of the glass can be neglected in this case, as this application exhibits the cavity effect. The cavity effect in infrared sensing occurs when a small, enclosed space traps infrared radiation, causing it to bounce around and enhance heat detection. This effect improves the accuracy and sensitivity of temperature measurements by increasing the apparent emissivity of the surfaces within the glass container. Low temperatures in this application demand using sensors with a long wavelength (8 µm -14 µm). Optris’ portfolio includes the Xi camera series, which features long-wave infrared cameras and a compact design for stationary installations.
The installation site offers limited space. In addition, it is within a cleanroom, so a high standard of purity for the thermal camera is applied. The Xi cameras use stainless steel components, meeting the necessary purity requirements. The design is very compact and offers several permanently different optics, ranging from telephoto to wide-angle lenses, ensuring a suitable solution for different conveyor belt widths.
The included free PIX Connect software features a hotspot search function that automatically detects the hottest temperature value in the infrared image. This function monitors the complete conveyor belt. In case of an alarm, the conveyor belt is stopped, and an operator can identify a hot glass container with a thermal image. To do so, the temperature values are forwarded into a programmable logic controller (PLC), which controls the filling process via the infrared camera’s analog output as a 4-20 mA signal. The software allows video and image recordings during the process. This way, the event can be recorded if the temperature exceeds. In addition, recordings can be made regularly during production for quality assurance.
Next to the glass containers before filling, the glass containers containing the product can also be measured to ensure redundancy.
Ensuring Pharmaceutical Safety and Quality by Infrared Monitoring Temperature-Sensitive Medical Goods
In summary, infrared cameras can provide critical temperature information necessary to insure the safe processing of pharmaceutical products. Pharmaceutical companies can follow some basic guidelines in order to properly implement remote infrared temperature measurement in their manufacturing process. First, understand if the material to be measured efficiently emits its infrared radiation (emissivity). In this application example, the empty glass vessel was over 6 times deeper than the opening at the top of the vessel creating the perfect “cavity bounce effect” that greatly enhanced the emissivity of the interior of the vessel. A measurement on the outer surface of the glass vial could yield an error because the temperature measured by the remote IR device could be influenced by an adjacent heat source. In this case, a different wavelength sensor would be recommended that is optimized for measurement on glass surfaces. Metal caps or aluminized peel-off seals are highly reflective (poor emissivity) and will essentially reflect the background temperature. It is also important to understand the spot size limitations of any infrared device when measuring small targets or small openings. Some single spot sensors would not be capable of accurate measurements of the inside of the glass vial because the spot size limitation of the sensor would be larger than the diameter of the vial. Fortunately, infrared cameras produce images from thousands of infrared pixels enabling measurement of very small areas. Make sure to use the optics calculator (link here) that takes into consideration IR camera optics, the camera resolving power and the the distance from the target. Finally, make sure to understand how the thermal dynamics of the manufacturing process can impart temperature variations on different areas of any convenance system. Temperatures can vary depending on a wide variety of factors and a quick scan with an infrared camera can help to optimize the placement of measurement cursors that will deliver temperatures on the full range of values that vary depending on their physical location.
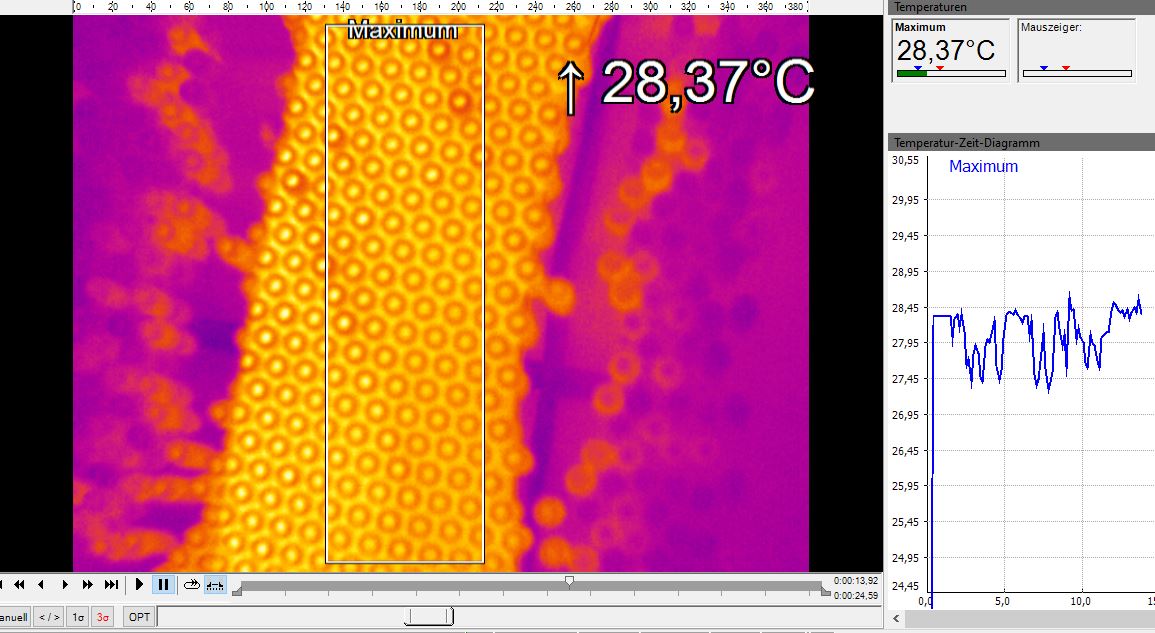
Recommended Products
Other Pharmaceutical & Medical Applications
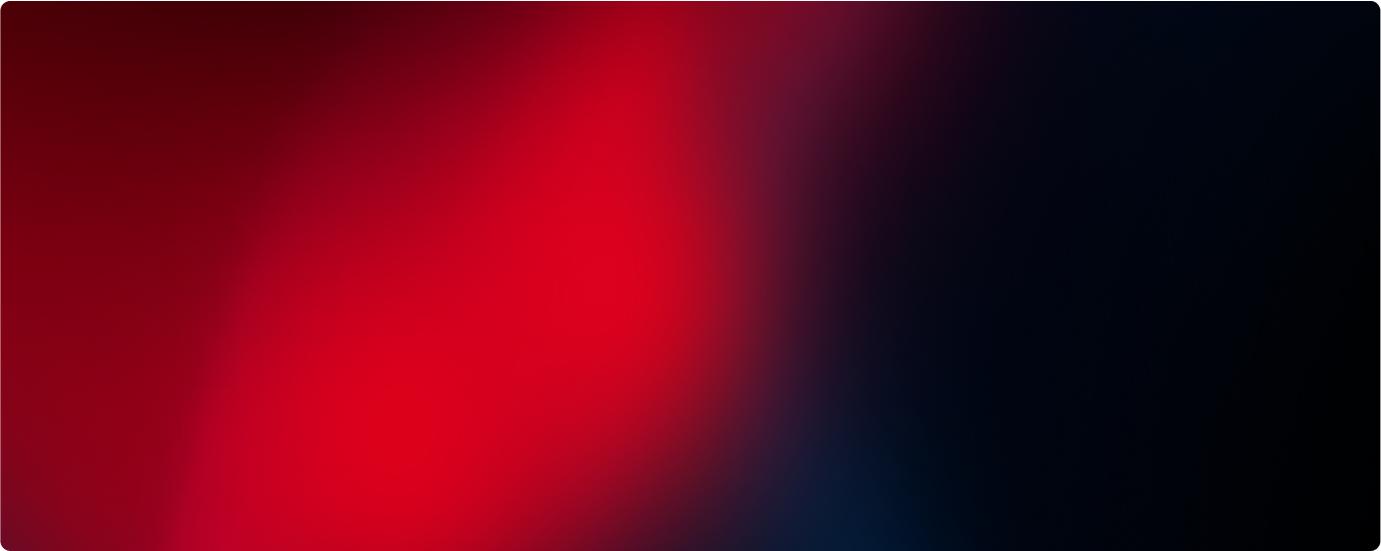
Talk to us about your IR Temperature Measurement Requirements
There are over 300 different pyrometer variants to choose from in the Optris infrared pyrometer portfolio each optimized for material, spot size, distance from the target, and environmental conditions. Fortunately, there is a trained engineer to phone or chat with to guide you through the process of choosing the perfect infrared sensor for your application.
The same support is available for the extensive IR camera product line.
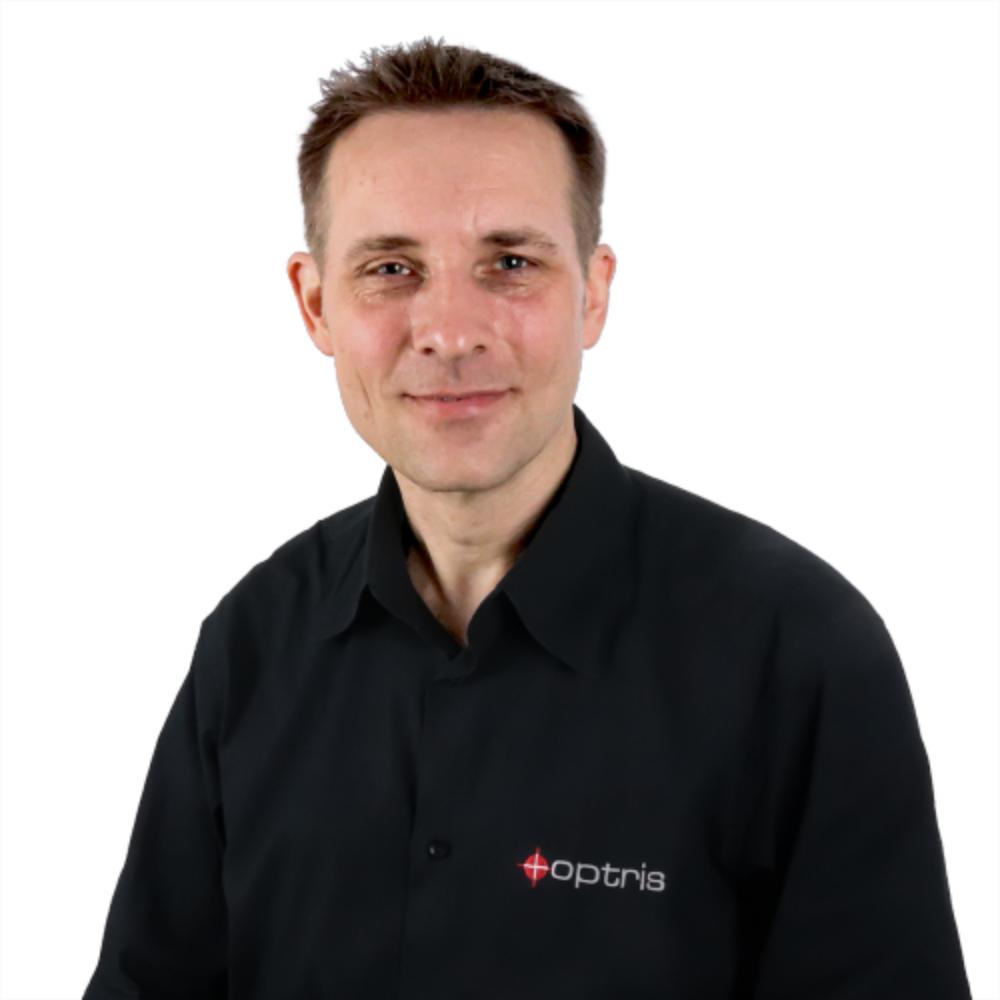