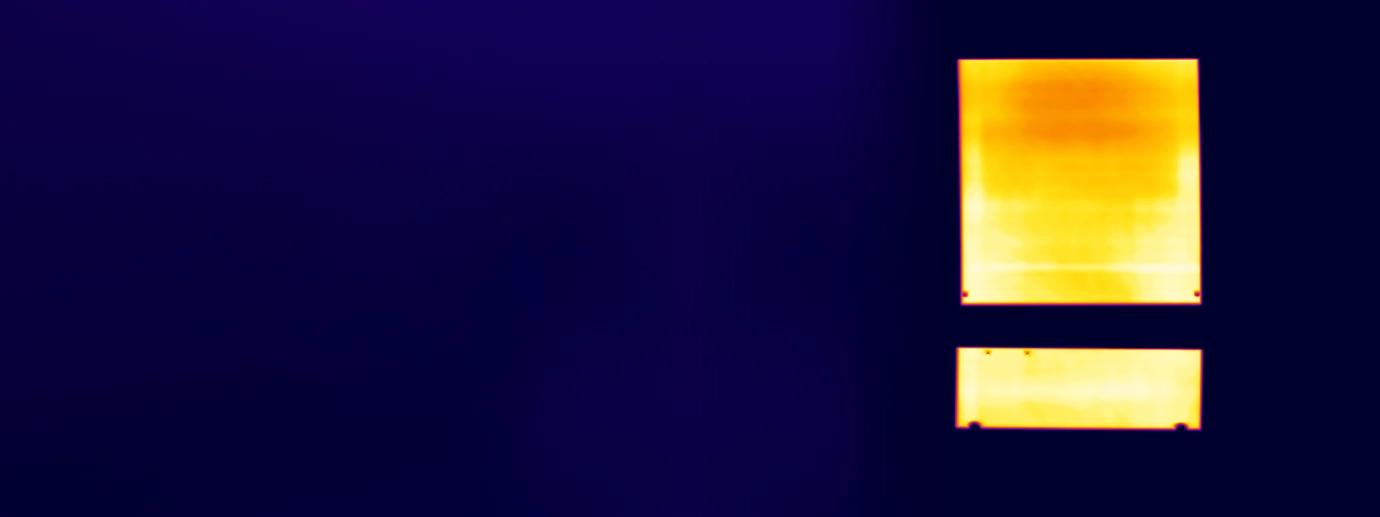
Accurate Infrared Cameras in the Float Glass Manufacturing Process
Enhancing Float Glass Production Efficiency with Infrared Technology
The Risks of Uneven Temperature Distribution
The float glass process is used to create large sheets of flat glass by floating molten glass over a bath of molten tin, resulting in a smooth and uniform surface. After leaving the tin bath at around 265°C, the glass moves through controlled cooling zones, where its temperature gradually drops to about 55°C. This step is crucial for preventing thermal stress, which can lead to defects such as cracks or spontaneous breakage.
One of the main challenges in the process is ensuring uniform temperature distribution across the entire glass surface during cooling. Uneven cooling can cause internal stress points that weaken the glass and compromise its quality. Traditionally, pyrometers were used to measure temperature at specific points, but they only provide localized readings, which may not capture the full thermal profile of the glass.
Additionally, the harsh environment of the cooling zones, with high temperatures and dust, can affect the accuracy and durability of conventional measurement tools. The accumulation of dust on sensors can reduce their effectiveness, leading to inaccurate readings.
The need for precise, real-time temperature monitoring is essential not only for improving product quality but also for enhancing production efficiency. Advanced infrared temperature measurement systems provide a more comprehensive solution, allowing manufacturers to monitor the entire glass surface and make timely adjustments to the cooling process, ensuring consistent results and reducing waste.
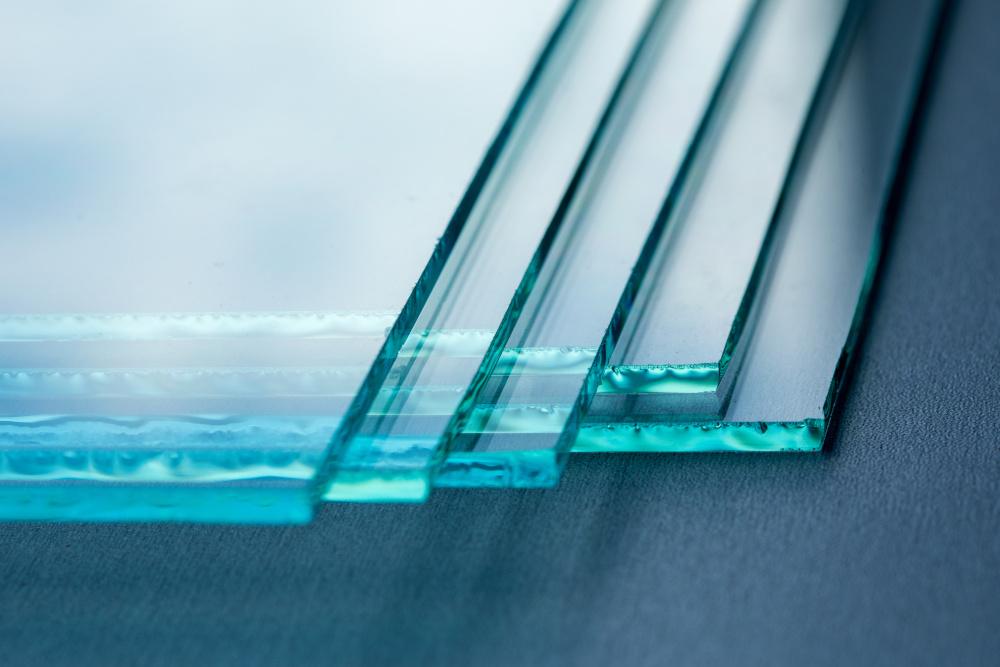
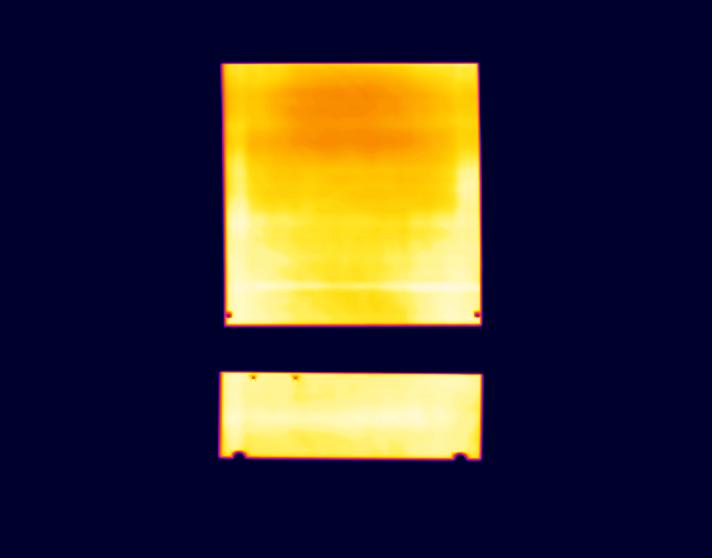
Line Scanning Technology for Comprehensive Surface Temperature Mapping
The integration of Optris PI 400 infrared cameras in the float glass manufacturing process, offers a precise and effective solution to the challenges of temperature monitoring. The PI 400 is a compact infrared camera, measuring just 46 x 56 x 68 mm, making it ideal for industrial environments where space and positioning are critical. With a high optical resolution of 382 x 288 pixels, the PI 400 provides detailed thermal images that cover the entire glass surface during the cooling phase. This high resolution ensures that manufacturers can detect even minor temperature fluctuations that could affect the quality of the glass.
The infrared camera operates within a spectral range of 8-14 µm, suitable for glass surface temperature measurement. With its customizable temperature ranges, from -20°C to 1500°C, the PI 400 is versatile enough to monitor various stages of the float glass cooling process. At the critical point where the glass exits the molten tin bath at around 265°C and cools down through different zones, the PI 400 continuously captures thermal data. By utilizing interchangeable lenses with fields of view up to 80°, manufacturers can select the most appropriate setup to monitor large areas efficiently.
A key advantage of the PI 400 is its integration with line scanning technology. As the glass moves through the cooling zones, the camera captures a series of thermal images merged to create a comprehensive temperature map. This enables operators to monitor the entire glass surface in real-time, ensuring the cooling process is uniform across all areas. The camera also offers an impressive frame rate of 80 Hz, providing fast and accurate measurements crucial in maintaining product quality.
The PI 400 is housed in an advanced cooling jacket to ensure reliable operation in the high-temperature environments typical of glass production. This protective casing allows the camera to operate in ambient temperatures up to 250°C, with water cooling and air purge systems in place. Combined with the infrared camera’s Ethernet interface and optional GigE support, these features allow seamless integration into the factory’s control systems. The cooling jacket also includes a laminar air purge device, which prevents dust and debris from accumulating on the camera’s lens, ensuring consistent performance over extended periods.
Automating the Cooling Process for Improved Efficiency and Cost Savings
Implementing Optris PI 400 infrared cameras in the float glass process provides significant benefits for manufacturers. The temperature measurement system ensures the glass cools uniformly by monitoring continuously, real-time temperature., reducing the risk of stress-related defects. This leads to fewer rejected products and higher overall efficiency in the production line. The PI 400’s high optical resolution and wide field of view allow it to capture thermal data from the entire glass surface, providing a more comprehensive understanding of temperature distribution than traditional pyrometers, which only measure at specific points.
One of the most essential advantages of using the PI 400 is its ability to automate the cooling process. The thermal imaging system can be integrated directly into the factory’s control system, allowing operators to set temperature thresholds and alarms. If the glass deviates from the set temperature range, the system can automatically adjust the cooling settings to ensure optimal conditions. This enhances product quality and reduces energy consumption by optimizing the cooling process.
The Optris PI 400 stands out due to its robust design and flexible integration options. With features like Power over Ethernet (PoE) and USB to GigE connectivity, the camera can transmit data over long distances without additional power supplies or complicated setups. This is particularly useful in large-scale float glass production facilities, where the control room may be far from the manufacturing line. Additionally, the camera’s software, PIX Connect, allows for the simultaneous monitoring of multiple cooling zones. This license-free software provides advanced analytics, including temperature profiling and alarm management, making it a valuable tool for process optimization.
The PI 400 offers high precision and reliability for temperature monitoring in float glass production. Its mid-resolution, wide field of view, and robust protective features make it the preferred choice for manufacturers looking to enhance product quality while reducing waste and operational costs. By combining advanced infrared imaging technology with intuitive software and flexible integration options, the PI 400 provides a comprehensive solution for optimizing the float glass process.
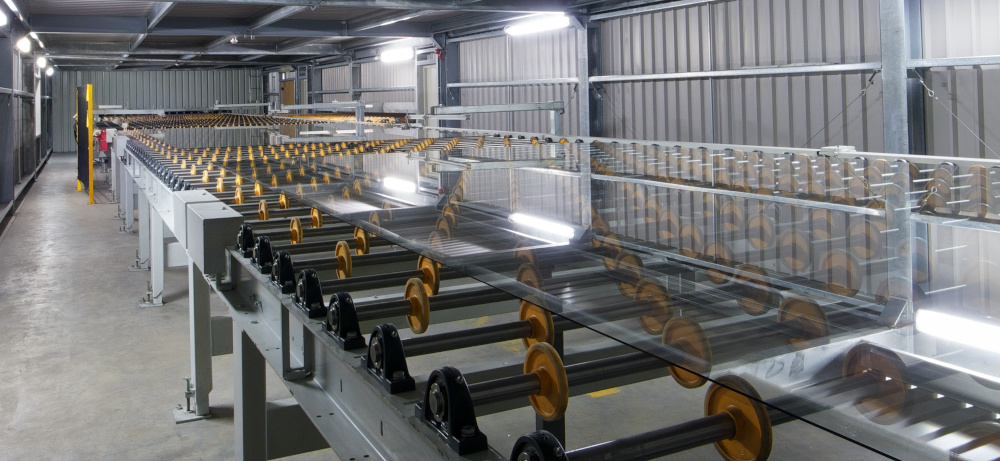
Recommended Products
Other Glass Applications
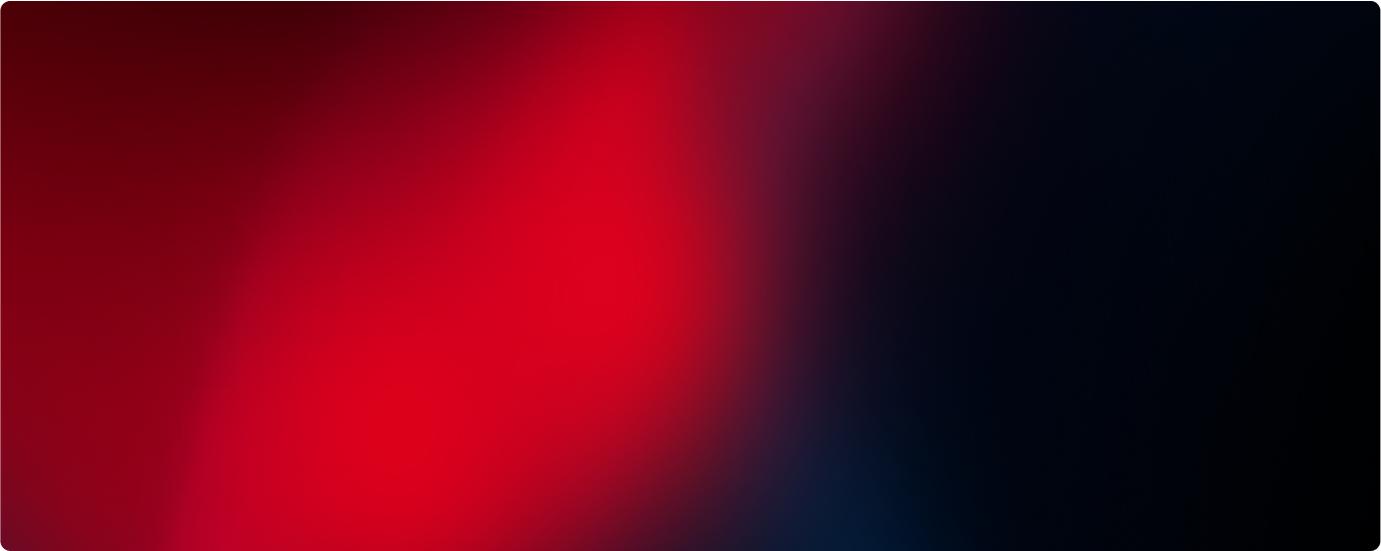
Talk to us about your IR Temperature Measurement Requirements
There are over 300 different pyrometer variants to choose from in the Optris infrared pyrometer portfolio each optimized for material, spot size, distance from the target, and environmental conditions. Fortunately, there is a trained engineer to phone or chat with to guide you through the process of choosing the perfect infrared sensor for your application.
The same support is available for the extensive IR camera product line.
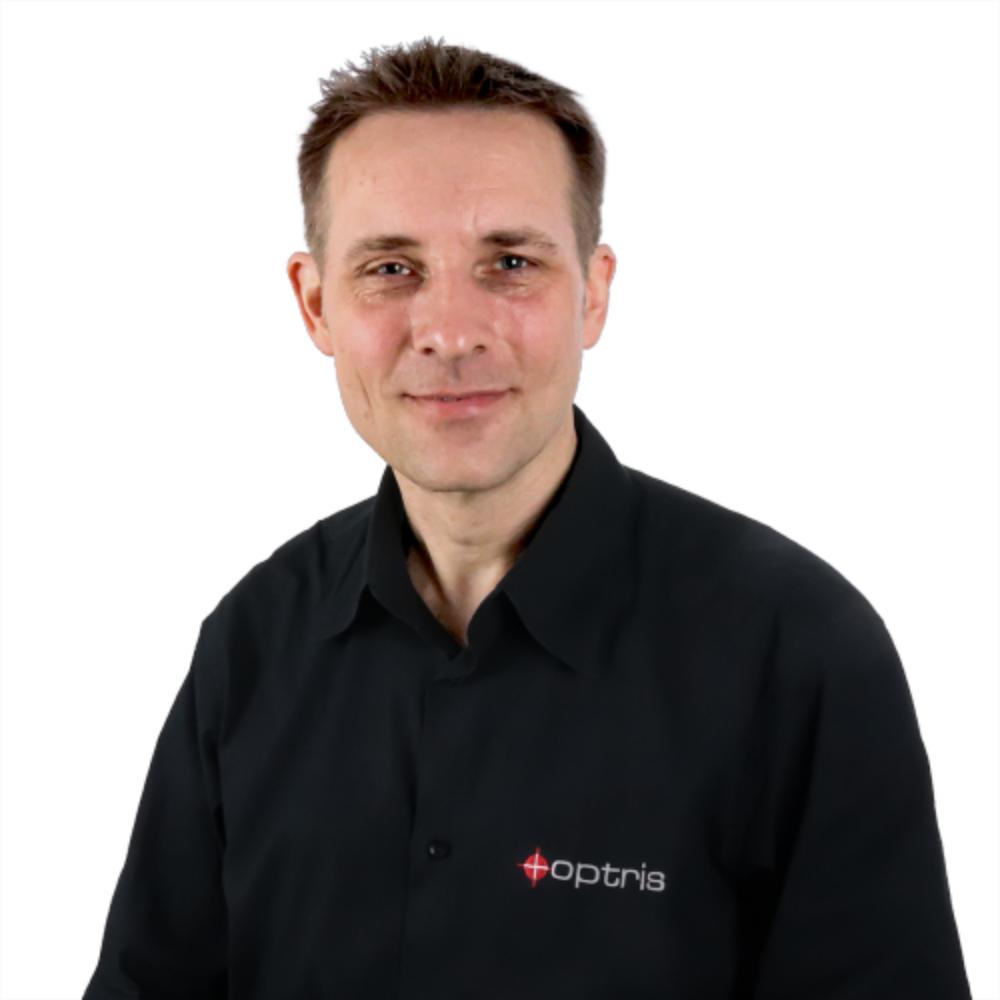