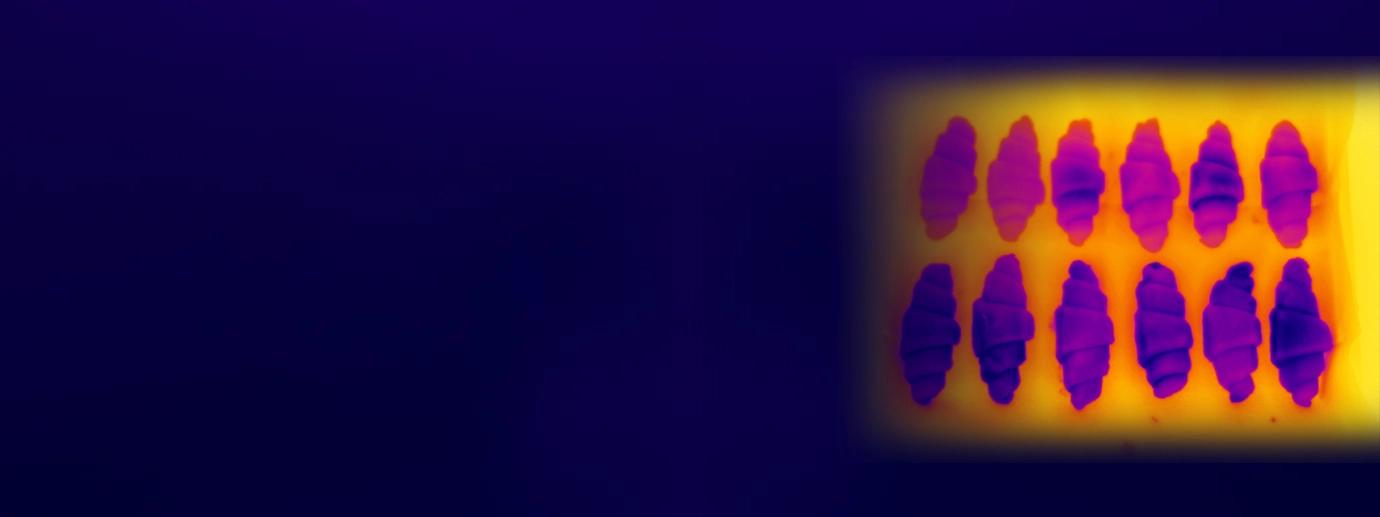
Ensuring Complete Packaging and Cold Chain Temperature of Croissants
Challenges in Measuring Packaged Food Through Plastic Packaging
Ensuring consistent quality in croissant packaging is a critical task in the food industry, especially when dealing with temperature-sensitive products. Croissants, typically packaged in plastic, require careful monitoring within the cold chain to guarantee freshness and safety. The packaging process involves placing the cooled croissants into plastic bags, and it is essential to ensure that the correct number of croissants is present in each package. However, maintaining the appropriate temperature, which is crucial to prevent spoilage and to ensure that the croissants reach consumers in optimal condition, presents a significant challenge.
The process takes place at temperatures ranging from -5 °C to 10 °C, depending on the specific setup of the packaging line. The challenge lies in accurately measuring the temperature of the croissants through the plastic packaging. Traditional methods, such as the use of contact temperature sensors, will damage the packaging, require manual inspection, and are time-consuming and labor-intensive. Additionally, weight-based checks are unreliable for lightweight products like croissants, which can vary slightly in size and shape, to detect the presence of food products.
The motivation behind this application’s noncontact temperature sensing approach is to improve quality control accuracy, ensuring that only properly packaged and cooled croissants are dispatched for distribution.
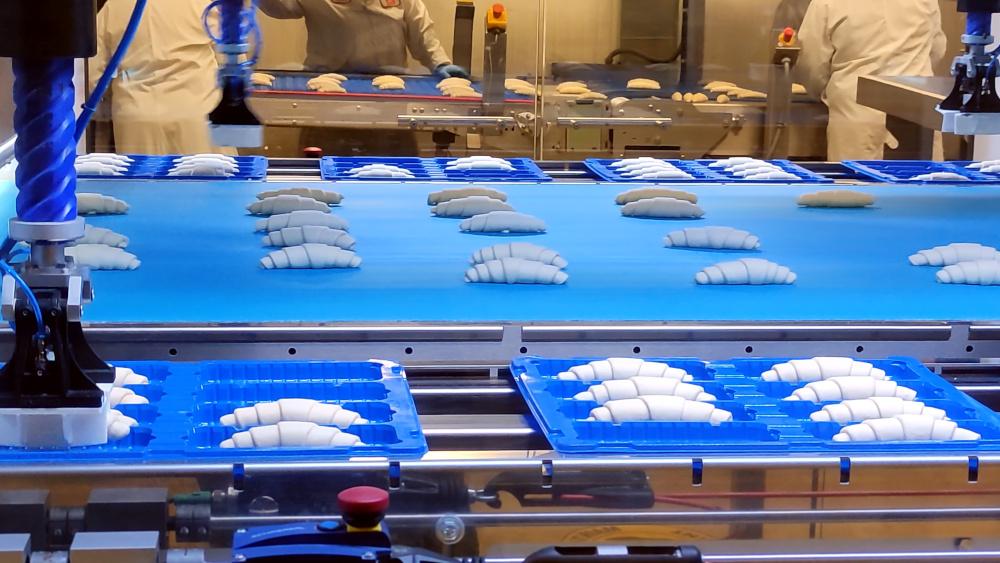
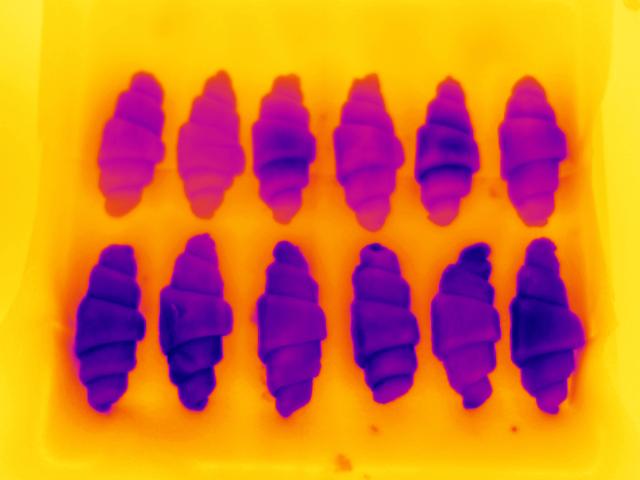
Automated Inspection Through Plastic Packaging of Food with Infrared Imaging Solutions
To address these challenges, temperature measurement through thermal imaging is required. This approach not only ensures that the croissants are sufficiently cold but also verifies their presence in the packaging. Optris infrared cameras, with their ability to measure temperature distribution through thin plastic films, offer a solution that meets these requirements.
The Optris PI 400 infrared camera, with its superior temperature resolution in the low-temperature range, is the perfect fit for this application. Its precision enables it to detect even minor temperature variations that could indicate issues in the packaging process. Positioned above the conveyor belt, it provides continuous monitoring of the croissants as they progress through the packaging line, ensuring the highest level of quality and safety.
The thermal camera is connected to a process interface linked to the system’s control unit. When a package of croissants passes through the light barrier, a trigger signal is sent, and the infrared camera captures an image. This image is analyzed to assess the temperature distribution across the croissants, allowing the system to determine whether the croissants are sufficiently cold and whether the correct number of croissants is present in the package.
Optris’s thermal imaging solution is particularly advantageous because it can penetrate the plastic packaging to measure the temperature of the contents accurately, regardless of the packaging’s opacity. The process interface then converts the temperature data into a signal that the control system can use to make real-time decisions, such as rejecting packages that do not meet the required standards. This setup ensures that the entire process is automated, eliminating the need for manual inspection and significantly improving efficiency.
Cost Savings Through Automation and Improved Quality Control in Food Packaging
Implementing Optris infrared cameras in the croissant packaging process has resulted in significant improvements in both quality control and operational efficiency. The ability to monitor temperature distribution accurately ensures that only packages containing sufficiently cooled croissants are approved for distribution. This reduces the risk of spoilage and enhances the overall quality of the product, leading to greater customer satisfaction.
The automation of the temperature measurement process also brings considerable cost savings. By eliminating the need for manual inspection, companies can reduce labor costs and minimize the potential for human error. The compact design of the Optris PI 400 camera allows for easy integration into existing packaging lines without requiring significant modifications, making it a practical solution for food manufacturers.
Optris’s thermal imaging technology stands out due to its reliability, precision, and ease of integration. The PI 400 infrared camera’s high resolution and sensitivity make it ideal for applications in cold chain management, where maintaining precise temperature control is essential. Additionally, Optris’s expertise in infrared technology and their commitment to customer support make them the preferred partner for companies looking to enhance their packaging processes with advanced thermal imaging solutions.
By choosing Optris, companies benefit from a proven solution that not only improves product quality but also optimizes the packaging process, making it more efficient and cost-effective. The unique selling points of Optris’s solution include its ability to measure temperature through plastic packaging, its integration capabilities, and its contribution to automating and streamlining the packaging process.
Recommended Products
Other Food Applications
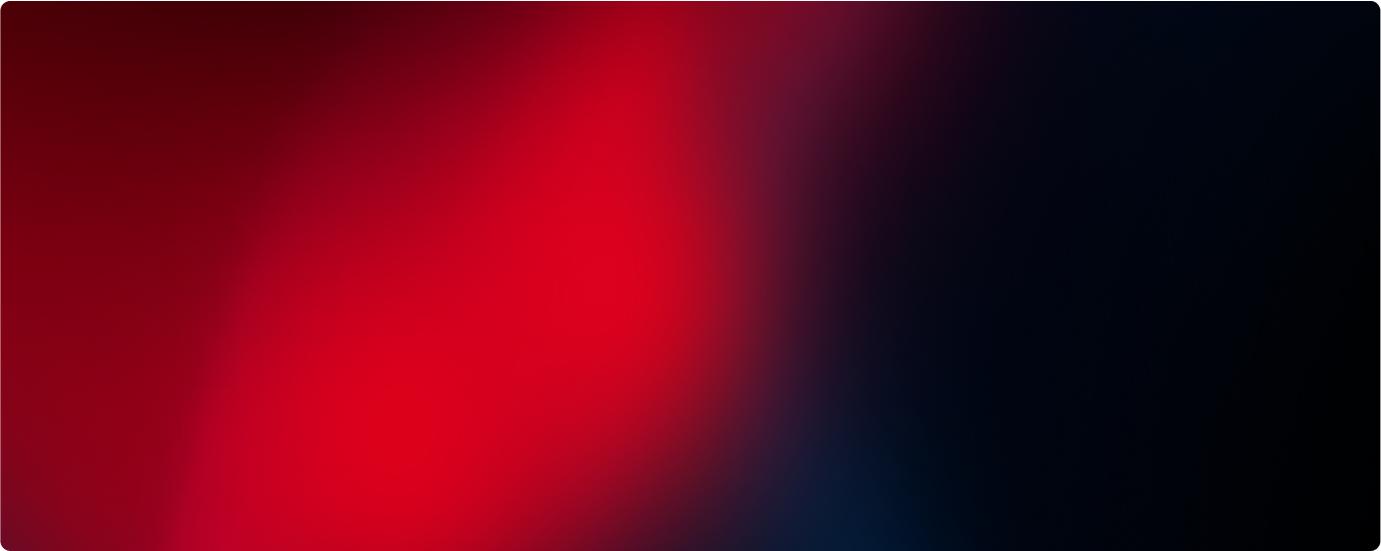
Talk to us about your IR Temperature Measurement Requirements
There are over 300 different pyrometer variants to choose from in the Optris infrared pyrometer portfolio each optimized for material, spot size, distance from the target, and environmental conditions. Fortunately, there is a trained engineer to phone or chat with to guide you through the process of choosing the perfect infrared sensor for your application.
The same support is available for the extensive IR camera product line.
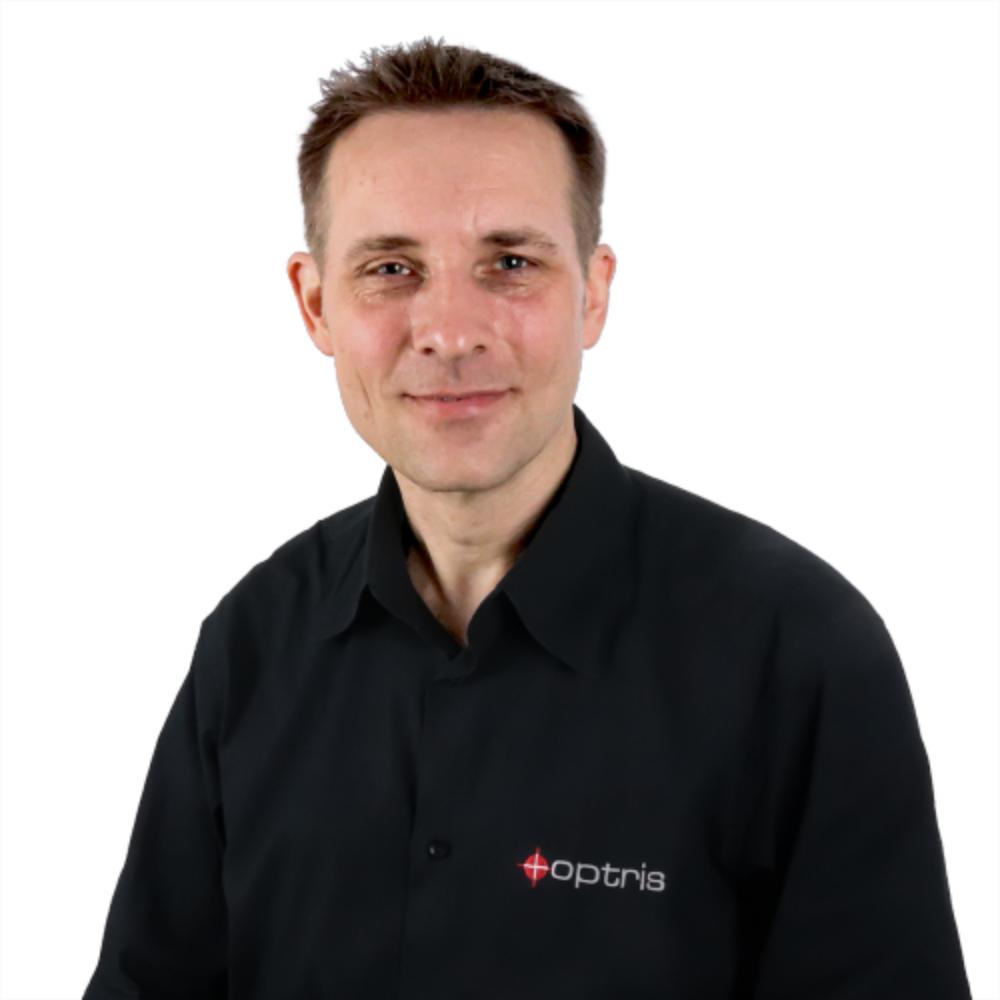