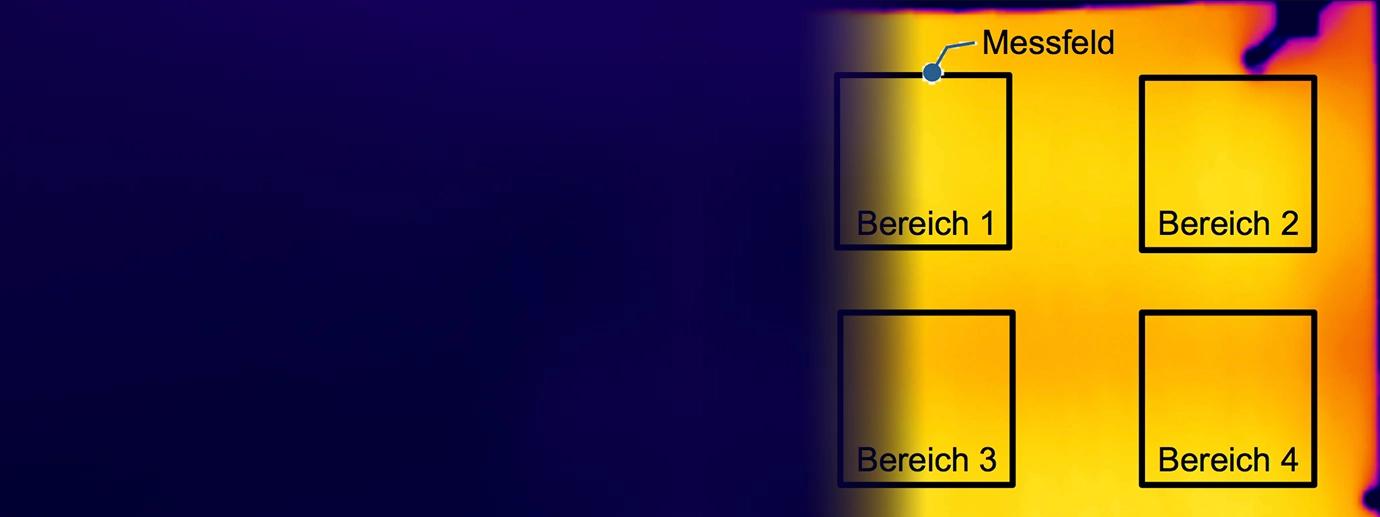
Overcoming Manufacturing Challenges with Continuous Fiber-Reinforced Thermoplastics in Automotive Engineering
Precision Temperature Control with Pyrometers in Combined Thermoforming and Injection Molding of Thermoplastics
Manufacturing Challenges with Continuous Fiber-Reinforced Thermoplastics
Plastic components are integral to numerous industries, and there have been ongoing advancements in manufacturing techniques and material combinations, particularly in demanding fields like automotive engineering. A standout innovation in this area is continuous fiber-reinforced thermoplastics, which offer a unique combination of exceptional strength and lightweight properties.
These materials provide superior mechanical performance while allowing for the creation of complex geometries. Injection molding technology further enhances this by giving manufacturers significant flexibility in designing precise workpieces, including the integration of metal components when necessary. Additionally, the technology’s ability to support short cycle times is crucial for efficient large-scale production. However, these materials also present challenges, particularly in the manufacturing processes required to optimize their performance.
KraussMaffei has addressed these challenges by developing the FiberForm process, a technique that enables the production of high-quality parts from continuous fiber-reinforced thermoplastics. The process begins with semi-finished products known as organo sheets—large-format materials composed of layers of glass, carbon, aramid, or composite fibers embedded in a thermoplastic matrix such as polyamide or polypropylene. These sheets undergo a multi-step transformation, including heating, thermoforming into the desired shape, and final back-injection molding. By integrating the thermoforming of organo sheets with injection molding into a single, streamlined process, KraussMaffei produces fiber-reinforced plastic components that are both exceptionally lightweight and highly durable, making them particularly well-suited for vehicle manufacturing.
The initial heating phase in the FiberForm process is critical to its success. For optimal results, the temperature must be uniformly distributed across the entire surface of the organo sheets. This is achieved by heating the sheets in specialized ovens with infrared radiators. Two key conditions must be met: the organo sheets must be heated rapidly, and the temperature must be distributed as evenly as possible across their entire surface.
One of the main issues is the precise temperature control required during the thermoforming process. Uneven heating can lead to defects in the final product, such as warping or inconsistent mechanical properties. This need for precise temperature control adds complexity to the manufacturing process, requiring advanced infrared heating technologies and sophisticated temperature controllers to ensure consistency and reliability in production.
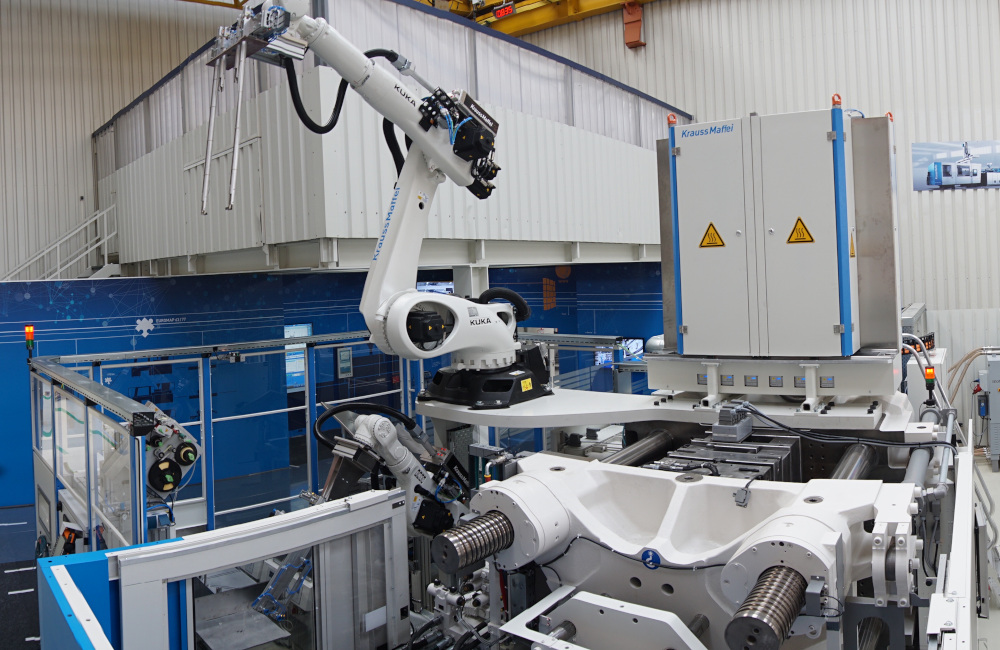
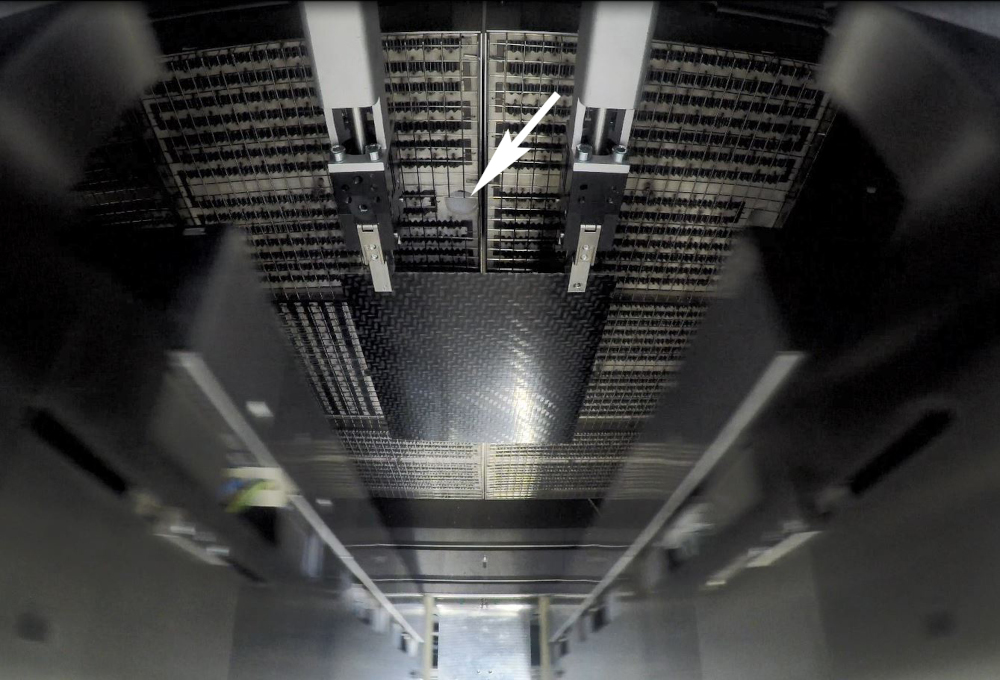
Optris Pyrometer Optimizes Temperature Control in KrausMaffei’s Infrared Heating of Thermoplastics
To ensure homogeneous and rapid heating of the organo sheets, KraussMaffei developed a custom infrared heating system that integrates up to 72 infrared radiators. However, the real breakthrough in maintaining consistent quality across the sheets was achieved through the use of Optris CT LT20 pyrometers. These rugged, compact sensors are strategically placed behind the infrared radiators, where they accurately measure the surface temperature of the semi-finished products.
The pyrometers are connected to an intelligent control system that continuously monitors and adjusts the heating zones to maintain a uniform temperature distribution across the entire sheet. This setup is further enhanced by the integration. The pyrometers’ durability and ability to operate at high ambient temperatures without cooling make them an ideal choice for this demanding application.
The pyrometers are two-piece units consisting of the compact sensor head, which measures just 14 mm in diameter and can operate at ambient temperatures of up to 180 °C without the need for cooling, and the electronic box, which is where the operational parameters are configured. This box is installed at a considerable distance from the sensor head. In this application, the electronic system is located outside the infrared heating system. The sensor head is fitted with an optional air purge collar to protect the optics from contamination by dust or spray mist, a common concern in the plastics industry.
The manufacturer’s software controls the temperature of the heating system through one external and several internal closed-loop systems. Each heating zone is assigned a pyrometer, and the external closed-loop system monitors the overall temperature while considering the interactions between different zones. Industrial PCs provide the necessary temperature control hardware, with the pyrometers connected via a 4 to 20 mA current output.
Benefits of Infrared Thermometers for Thermoforming and Injection Molding of Organo Sheets
The infrared heating technology is designed to heat the organo sheets both quickly and uniformly, a critical factor in large-scale production. Reliability is paramount, as the ovens must function consistently to avoid interruptions in the manufacturing process. A single pyrometer failure could potentially halt production entirely, making the dependability of every component essential. To ensure optimal performance, the results are continuously verified using Optris infrared cameras. KraussMaffei’s new process regulation system further enhances the uniform distribution of surface temperature across the organo sheets. Since the implementation of this system, KraussMaffei has not encountered a single device failure, underscoring the reliability and effectiveness of this advanced solution in demanding production environments.
The compact infrared thermometers offer an industrial design, which separates the electronics from the sensor head and allows them to operate effectively in high ambient temperatures. Additionally, the optional air purge collar provides protection against harsh conditions, such as dust or spray mist, ensuring reliable performance even in challenging settings. The infared thermometers are equipped with fail-safe sensors that guarantee homogeneous surface temperature measurements, crucial for maintaining consistent quality in production processes. Furthermore, the devices are designed for easy integration, allowing for seamless implementation into existing systems.
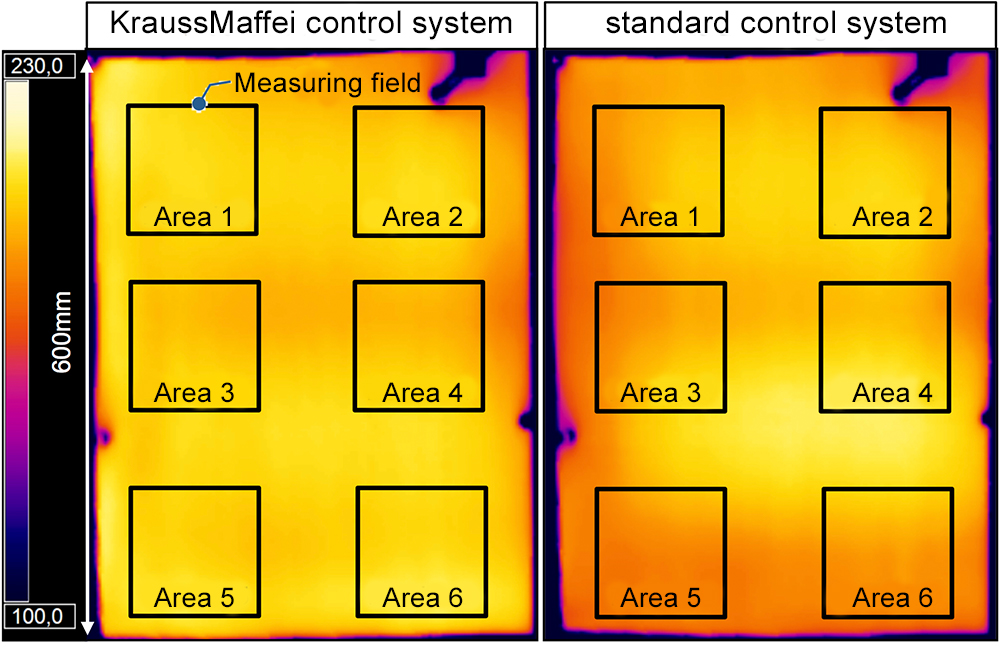
Recommended Products
Other Automotive Applications
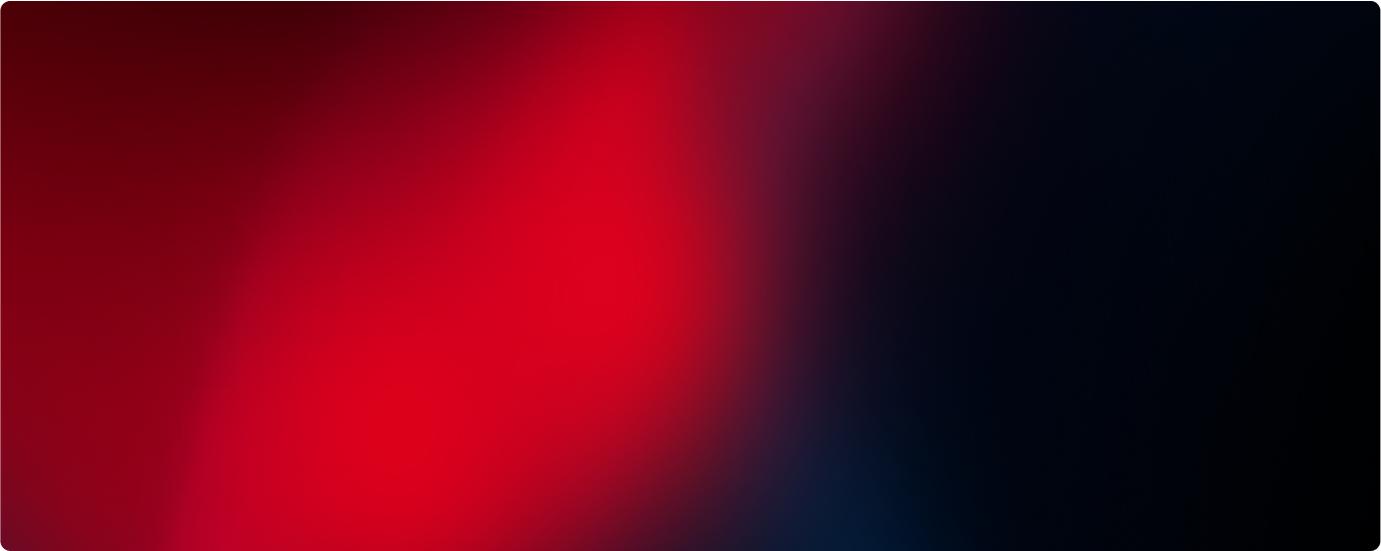
Talk to us about your IR Temperature Measurement Requirements
There are over 300 different pyrometer variants to choose from in the Optris infrared pyrometer portfolio each optimized for material, spot size, distance from the target, and environmental conditions. Fortunately, there is a trained engineer to phone or chat with to guide you through the process of choosing the perfect infrared sensor for your application.
The same support is available for the extensive IR camera product line.
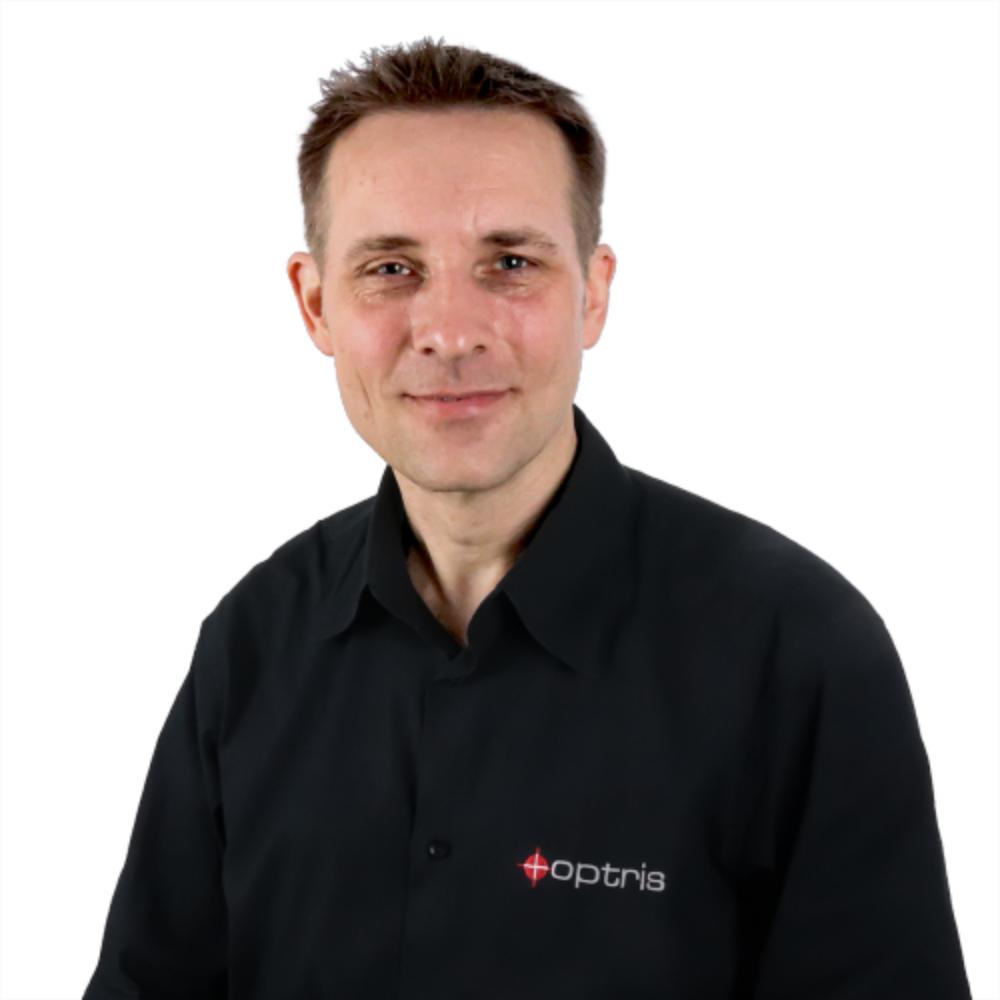