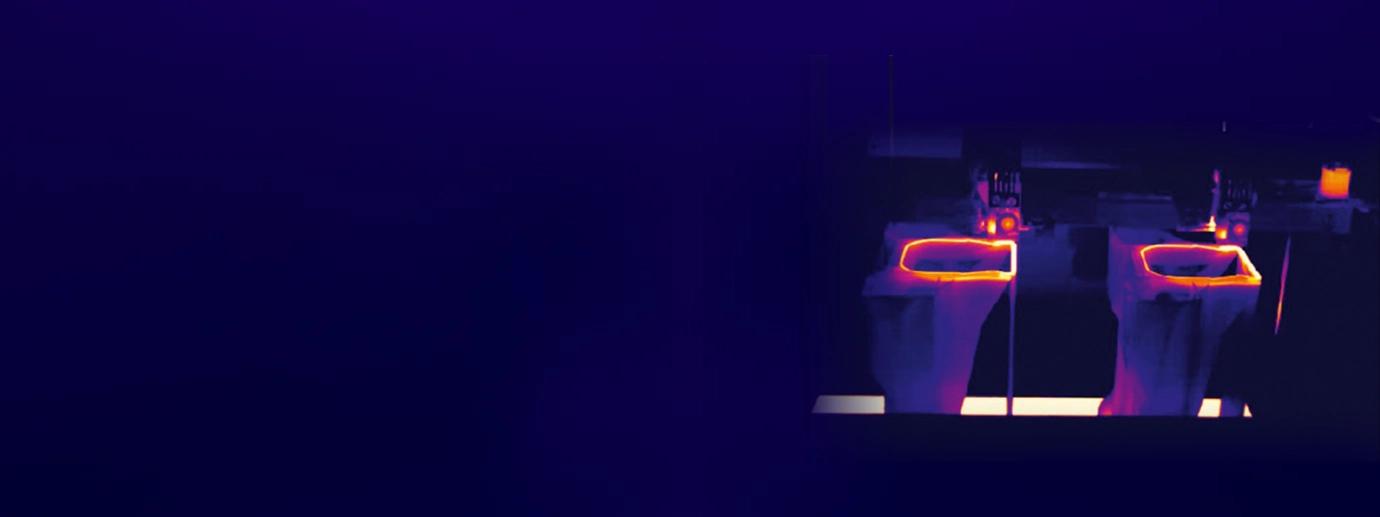
Innovative Infrared Temperature Measurement Technology for Wire Arc Additive Manufacturing
Temperature Process Control for Wire Arc Additive Manufacturing with Ratio Pyrometer and Short Wavelength Infrared Cameras
Enhancing Quality in Metal 3D Printing: Temperature Control in Metal Additive Manufacturing
Wire Arc Additive Manufacturing (WAAM) is an additive manufacturing process that has become more important in the 3D printing of metals in recent years. High build rates, wire as a cost-effective and easily available starting material and a highly controllable process are the main advantages.
In Wire Arc Additive Manufacturing, the material is applied to a base plate as a wire using arc welding, weld bead by weld bead. This has several advantages compared to powder-based processes:
A wire is a much cheaper starting material and most materials are available in wire form. In addition, both the complex powder handling and vacuum technology can be dispensed with. The biggest advantage, however, is the very high build-up rate that can be achieved with WAAM. Depending on the material used, this can be up to 650 cm^3 per hour.
The Berlin-based company GEFERTEC develops and builds machines that use the WAAM process for the 3D printing of metals. The arc machines, which are available as 3-axis and 5-axis variants in different sizes, integrate sophisticated arc welding technology, user-friendly CAM software, and a machine tool to create a ready-to-use additive manufacturing solution.
Temperatures play an important role in the WAAM process. This is because the temperature distribution in the workpiece and the cooling behavior are crucial for ensuring the quality of the finished component. During the operation of the machine, welding is only started when the underlying layer has cooled down to a certain temperature. If the intermediate layer is still too warm, this leads to uneven build-up behavior – the layer thickness would vary too much and the geometry of the component would not be maintained.
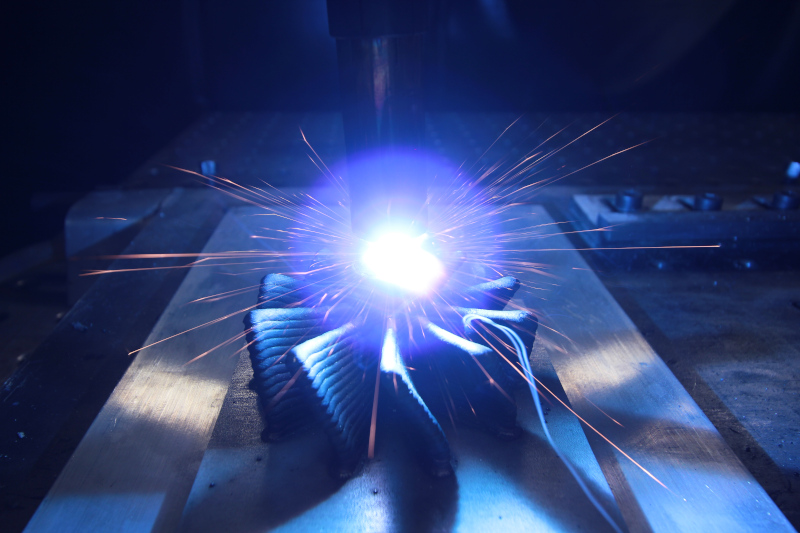
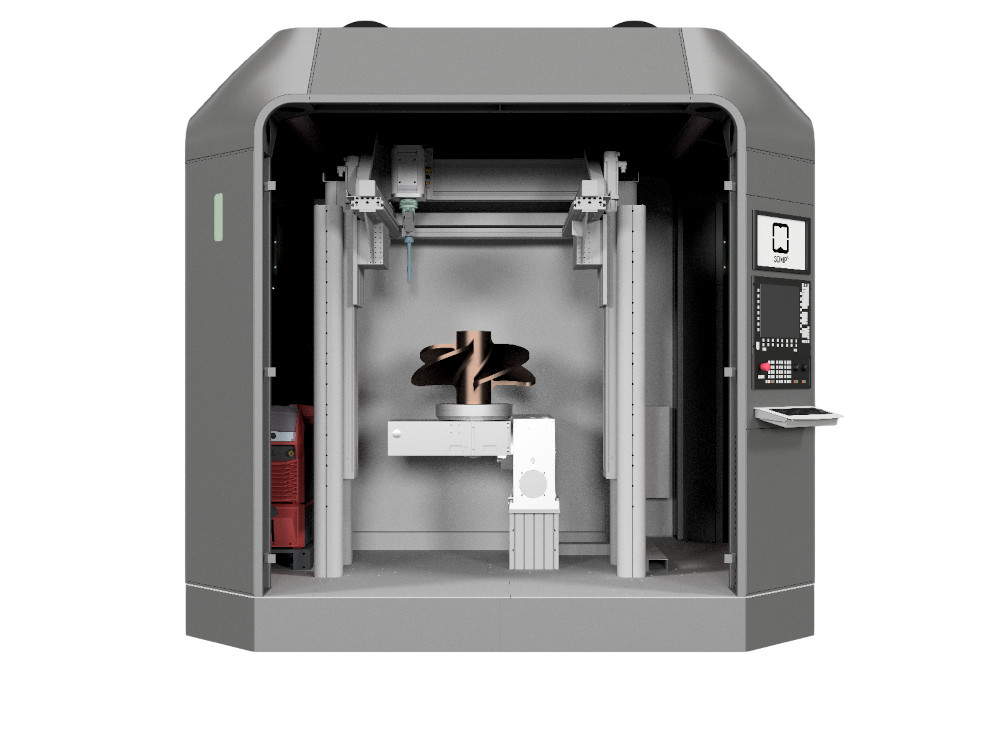
Pyrometry Control for Arc Machines: Optimal Interlayer Temperatures for Weld Seam Reproducibility
The corresponding temperature measurement technology is solved in the GEFERTEC arc machines with an Optris pyrometer from the CT series. In most applications, the set value for the interlayer temperature is between 150 °C and 200 °C, which is optimal for reproducibility of the weld seam height.
After completing a layer, the welding head moves to the starting point of the next layer, where the pyrometer measures the temperature of the component. And only when this has dropped to the preset value does the machine continue working.
The CT series pyrometers that are used have a very small measuring head that can be easily integrated into the application. The separate electronics box, which is housed in a control cabinet, has various outputs via which the value is transferred to the machine’s control system. In this way, the interlayer temperature is set perfectly to the right value during operation. The emissivity must be known exactly to determine the temperature accurately with a pyrometer. If the view of the measuring surface is disturbed, the measurement can be falsified. GEFERTEC’s arc machines can also be used to print titanium components, although this results in the development of heavy smoke.
In this case, ratio pyrometers, such as those from the CTratio series from Optris, are recommended. As the ratio of the intensities at two wavelengths is formed here, the measurement can be carried out reliably despite disturbed vision. CT ratio pyrometers are planned to be used in arc machines in which the user plans to print titanium components.
Thermographic Imaging in Arc Machines: Benefits of Optris PI 1M Thermal Imagers
In addition, the Optris infrared camera model PI 1M is used in the development of arc machines and especially in process qualification.
This thermal camera model has a highly dynamic CMOS detector, which offers an optical resolution of up to 764 x 480 pixels.
In the context of GEFERTEC’s investigations, it is advantageous to record an overall image and thus visualize a spatial distribution of temperatures.
This allows for the examination of these distributions and cooling processes, which is required for their qualification.
The PI 1M model, with its ideal spectral range for measuring metal surfaces, delivers high-quality results and actual temperature values in the molten bath and its surroundings. The spot finder function, a practical feature for this type of application, further enhances its utility.
The infrared cameras from Optris can be easily connected to a PC via a USB interface for image transfer. The PIX Connect analysis software, supplied with the cameras, allows for real-time evaluation of the thermographic images, making it a practical tool for process qualification. The software also simplifies the archiving of images, enhancing the overall user experience.
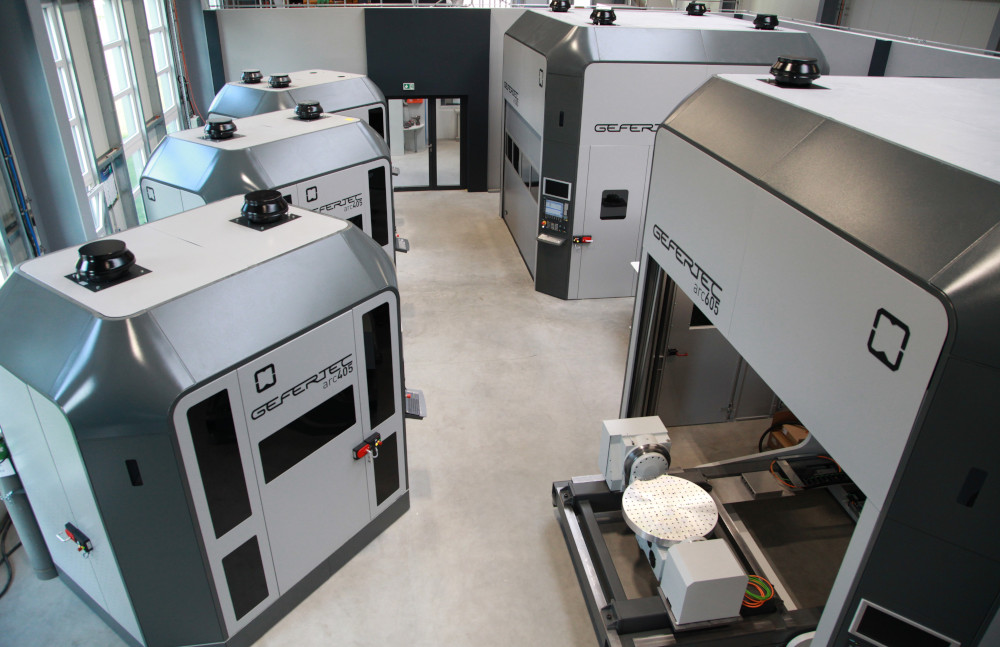
Recommended Products
Other 3D Printing & Additive Manufacturing Applications
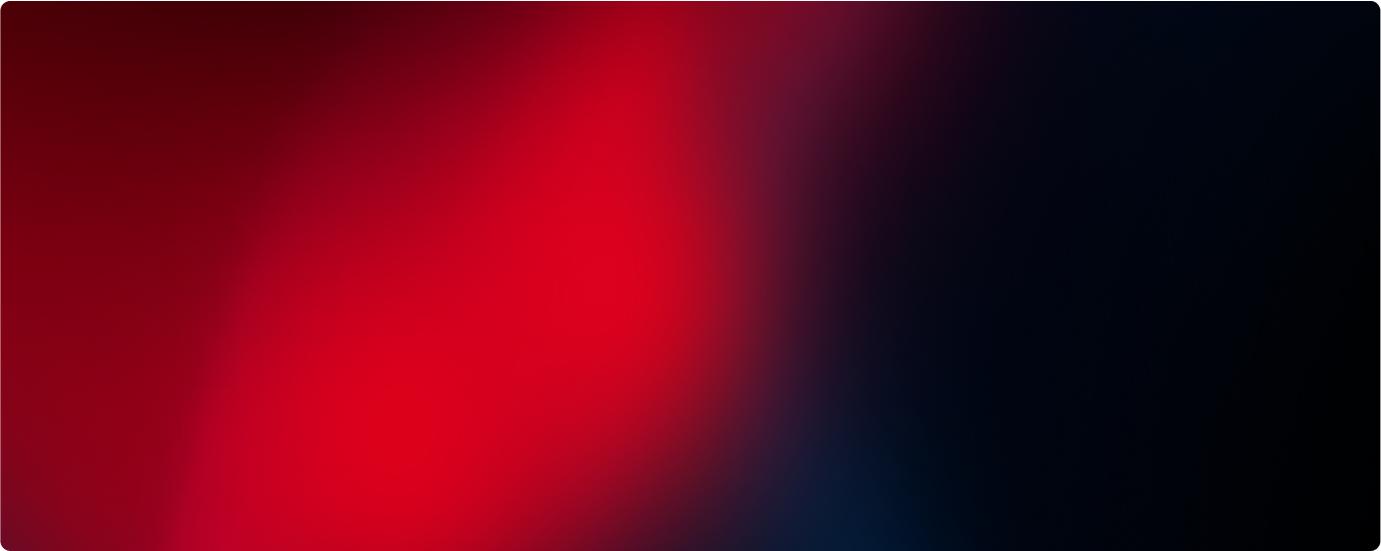
Talk to us about your IR Temperature Measurement Requirements
There are over 300 different pyrometer variants to choose from in the Optris infrared pyrometer portfolio each optimized for material, spot size, distance from the target, and environmental conditions. Fortunately, there is a trained engineer to phone or chat with to guide you through the process of choosing the perfect infrared sensor for your application.
The same support is available for the extensive IR camera product line.
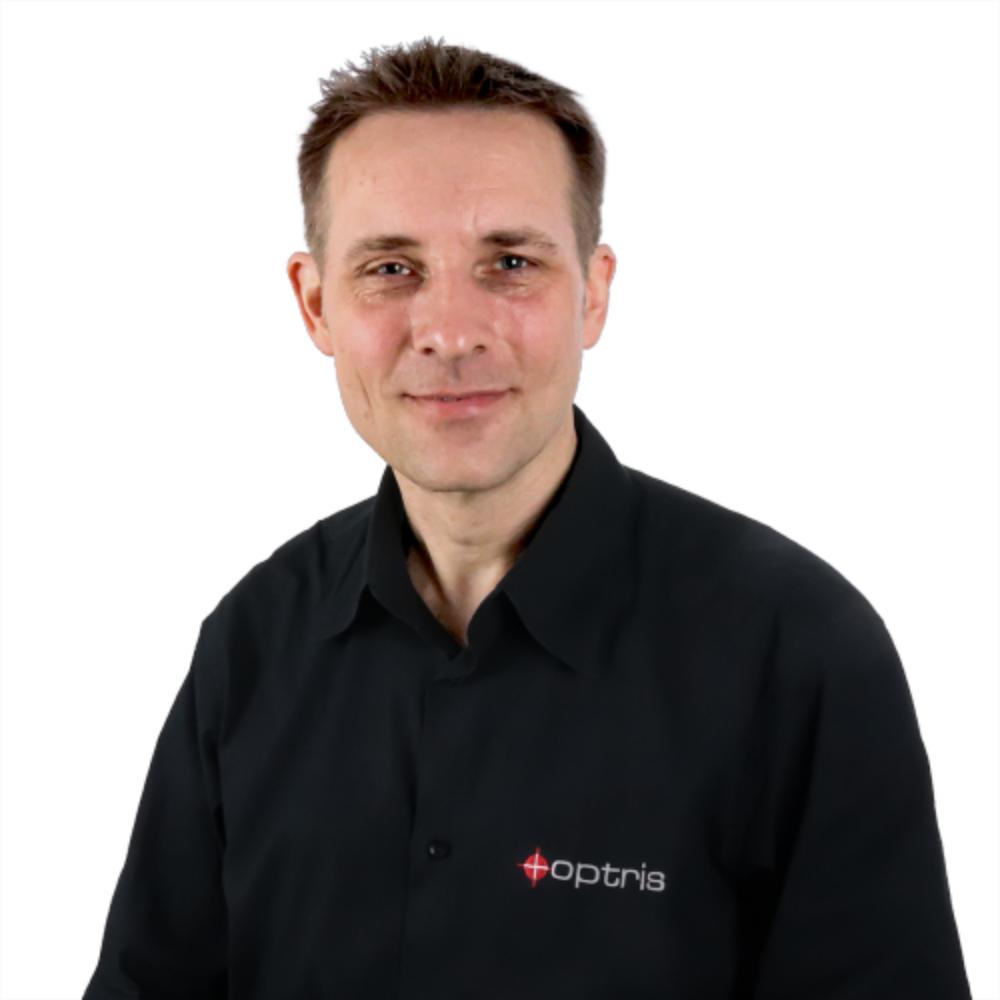