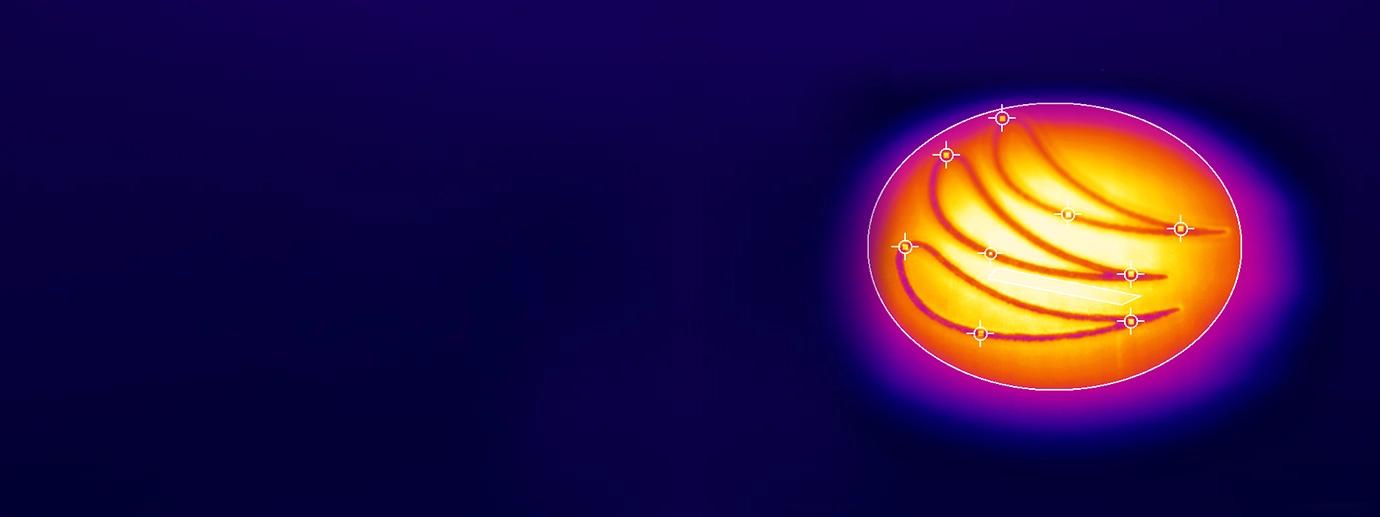
From Powder to Precision: Infrared Measurement Technology in 3D Metal Printing
Laser Powder Bed Fusion: Ensuring Print Quality Through Accurate Process Temperature and Infrared Measurement
Navigating the Challenges with Temperature Regulation and Quality in Metal 3D Printing
The 3D printing of metals has seen significant growth in recent years. For over 25 years, powder bed-based laser beam fusion (LPBF) has stood out as one of the most promising methods for additive manufacturing of metals. Developed and patented by the Fraunhofer Institute for Laser Technology ILT in 1996, the LPBF process is particularly suited for creating components with complex and intricate geometries. This precise 3D printing technique enables the production of parts that are impossible to manufacture using subtractive methods, continuously unlocking new industrial applications.
In LPBF, the starting material is a powder applied in a thin layer to a base plate. A laser beam then selectively melts areas of the powder to form the desired component. Upon solidification, a solid material layer is created. The base plate is subsequently lowered, and another layer of powder is applied. This iterative process is repeated layer by layer, resulting in a three-dimensional component that requires only the removal of excess powder.
At Fraunhofer ILT, the LPBF process is continuously refined through various research projects. The institute operates several LPBF laboratory facilities to advance this work. The quality of the LPBF process is highly dependent on maintaining correct process temperatures. The laser beam heats the material extremely rapidly, with rates reaching up to 1 million Kelvin per second. The melted material then cools quickly, posing risks of stresses, shrinkage, phase transformations, and other physical effects that can compromise quality. Issues such as cracking or plastic deformation can ultimately lead to defective components.
To prevent these faults, the base plate is heated to better regulate the component’s temperature, minimizing stresses caused by excessive temperature gradients. However, the parameters influencing the component’s temperature vary throughout the process. The distance to the heated base plate increases with each layer, the powder bed conducts heat poorly, radiation impacts the process, and the laser introduces additional heat. Therefore, continuous adjustments to the heating are necessary throughout the process.
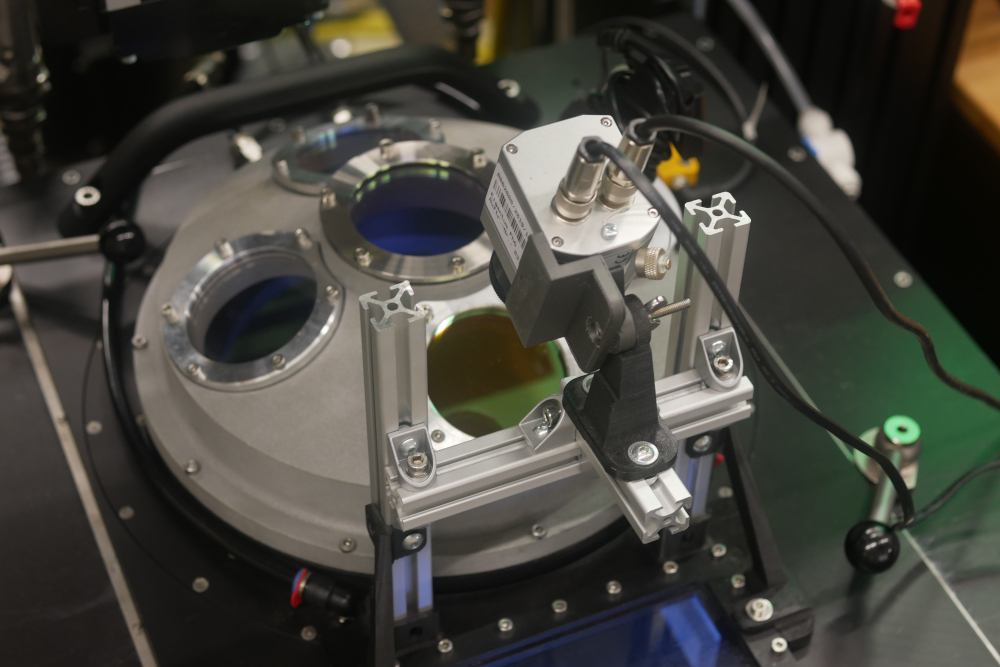
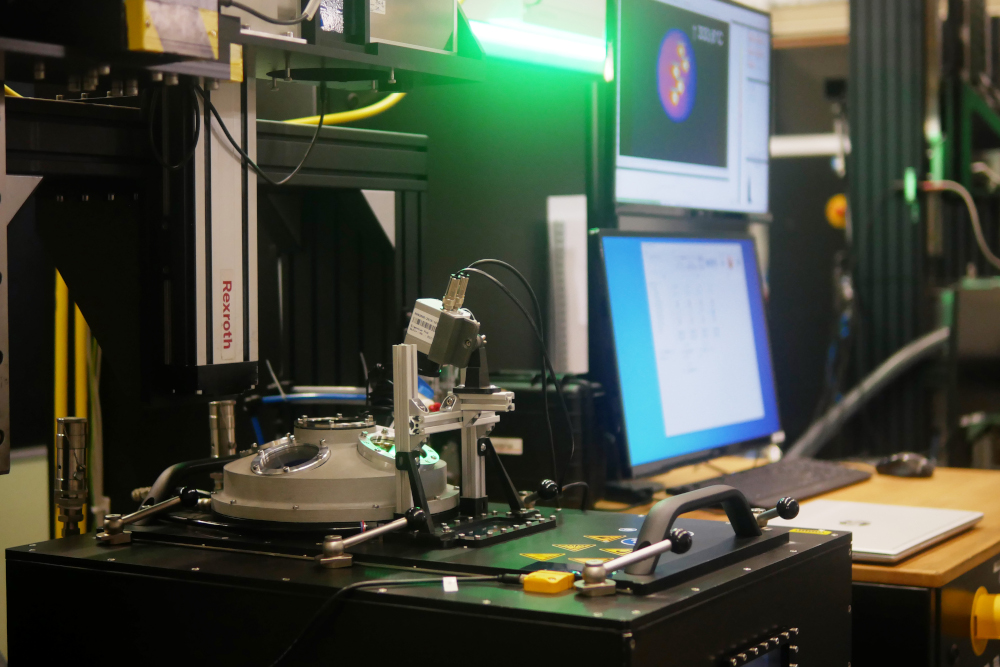
Infrared Temperature Measurement and Visualization During the 3D Printing Process
An Optris PI 640i infrared camera, capable of measuring temperatures up to 1500 °C, is used to optimize the temperature regulation process. This infrared camera is mounted outside the process chamber, with a zinc selenide window integrated into the chamber for this purpose. One challenge in infrared temperature measurement is dealing with the emissivity of metallic surfaces. For instance, the emissivities of metal powders and solid bodies vary and are also influenced by surface conditions. While measuring metallic surfaces with a long-wavelength infrared camera can be difficult, the surface roughness, in this case, provides sufficient emissivity.
Another challenge involves optical interference with the powerful laser and interacting with it. Fortunately, most commercial lasers for this process operate in a different spectral range, typically using standard continuous-wave lasers at 1.064 µm. This wavelength differs from that of the long-wavelength infrared camera used here.
During the build-up process, the infrared camera then measures the temperature of the component after the molten bath has solidified again. The system’s controller triggers the infrared camera via a digital interface for capturing thermal images. This can happen shortly after the laser has been switched off and before the next layer of powder is applied. This allows various effects to be investigated. Typical measurements determine, for example, the cooling behavior after remelting or the dissipation of heat via the powder bed. In this way, the heating of the component can then be adjusted in such a way that defective components are avoided.
Simple Evaluation of the Thermographic Images allows Optimization of 3D Printing Quality
The PI 640i infrared camera is very compact and can be easily mounted above the window. With a resolution of 640 x 480 pixels, it can also resolve smaller component structures due to the emphasis on MFOV characteristics.
The infrared camera is connected via a USB interface to a PC on which the PIX Connect analysis software is installed, which is supplied by Optris together with the infrared cameras.
The software analyzes thermographic images and offers comprehensive recording and analysis options. The system used by the Fraunhofer ILT also allows for the archiving and saving of images in an open format, which is an important advantage. Another important aspect is the very easy analysis of the thermographic images within the PIX Connect software.
The Fraunhofer ILT has been using the PI series for several years. Previously, in many cases, only pyrometers were used, where the temperature could only be measured at one point at a time. Overall, the Optris infrared camera is very well suited for this process at the ILT. Its compactness makes it mechanically easy to integrate and simple to operate.
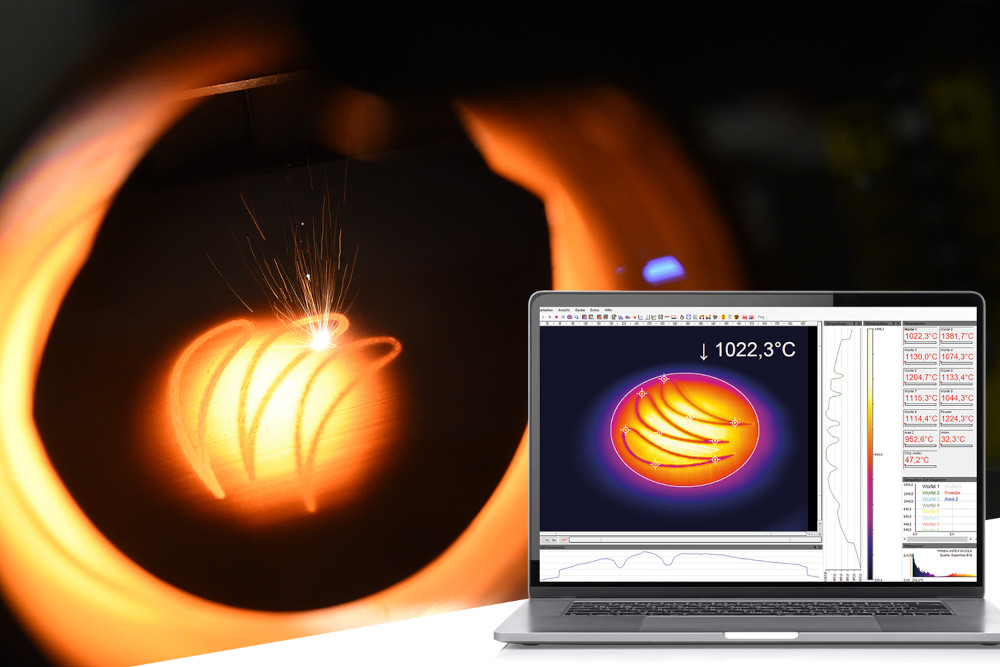
Recommended Products
Other 3D Printing & Additive Manufacturing Applications
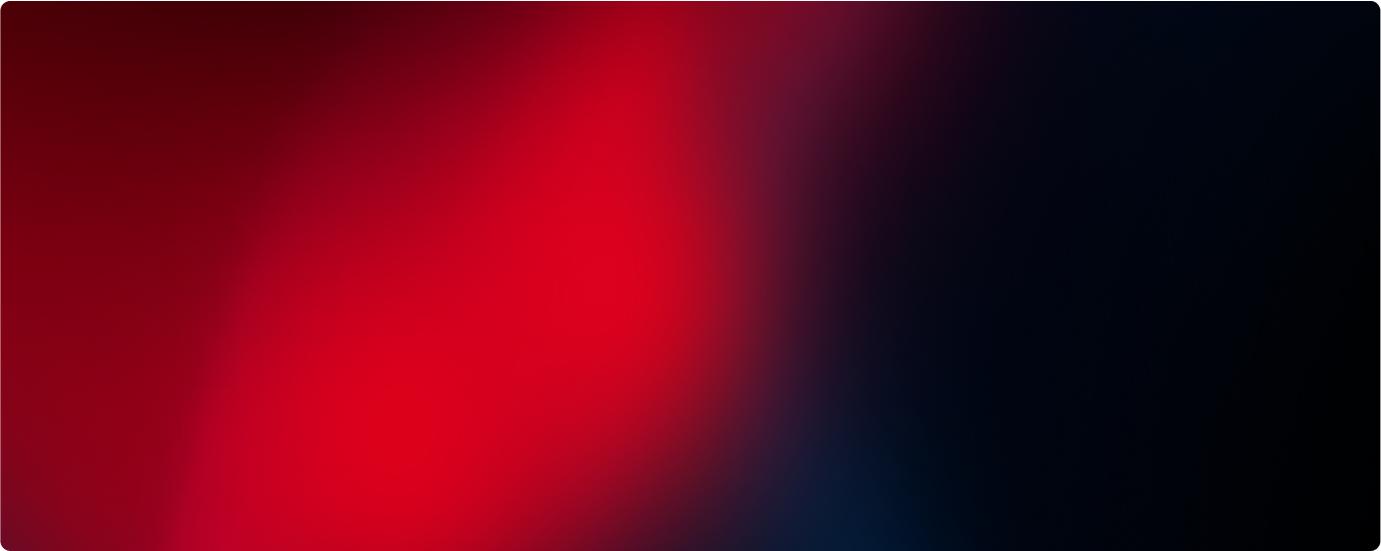
Talk to us about your IR Temperature Measurement Requirements
There are over 300 different pyrometer variants to choose from in the Optris infrared pyrometer portfolio each optimized for material, spot size, distance from the target, and environmental conditions. Fortunately, there is a trained engineer to phone or chat with to guide you through the process of choosing the perfect infrared sensor for your application.
The same support is available for the extensive IR camera product line.
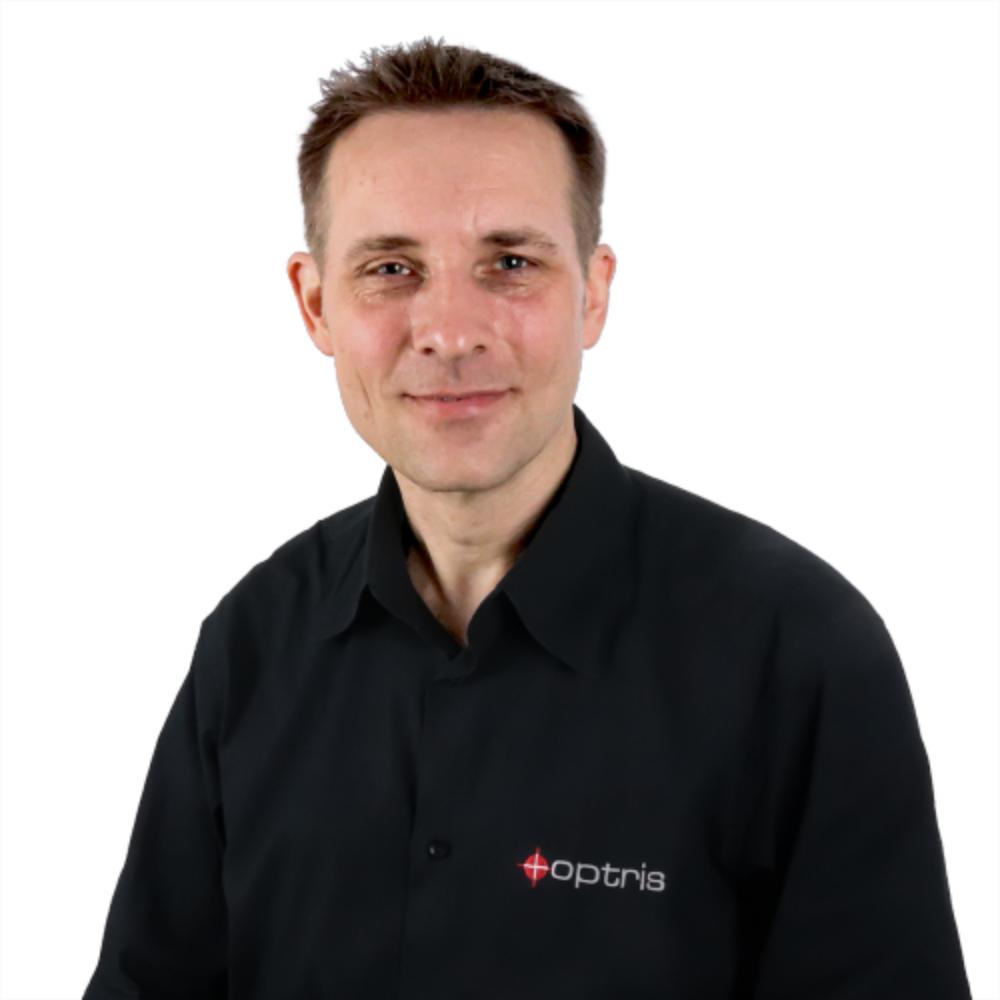