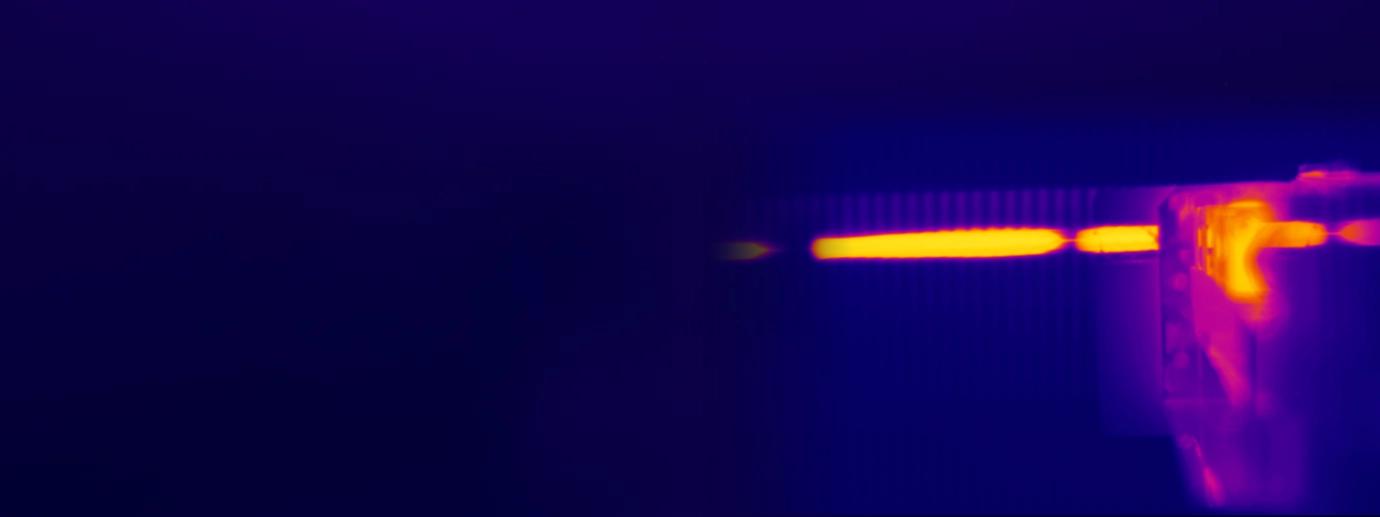
Ensuring Optimal Bond Strength and Placement with Real-Time Adhesive Application Monitoring
Monitoring Adhesive Applications to Prevent Defects in Plastic Part Bonding
Inconsistent Applications of Adhesive on Plastic Components
Monitoring adhesive applications ensures product quality and reliability across various industries. Consistent and accurate adhesive application guarantees optimal bond strength. In manufacturing processes, real-time monitoring can help detect irregularities such as insufficient or excessive adhesive, preventing potential failures and costly rework. Monitoring adhesive placement helps maintain process efficiency, reduce waste, and ensure compliance with industry standards. Many companies in sectors like automotive, aerospace, and electronics, where the integrity of adhesive bonds directly impacts safety and functionality, particularly in the aerospace and defense industries, require documentation of adhesive bond quality. Some may need documentation on every part to verify manufacturing parameters months or years later.
An engineering firm specializing in custom automation equipment for various industries must develop a system for applying adhesive beads onto ribbed plastic sheets. The adhesive application needs to be more consistent, compromising finished product quality, consisting of two plastic sheets bonded together. Each 900mm long plastic sheet is ejected from the adhesive application system every three seconds. The adhesive bead is applied at approximately 170 °C, while the area adjacent to the bead is around 25 °C, varying with the ambient temperature of the manufacturing facility. The client has used infrared handheld cameras with some success, but the manual inspection process for ensuring consistent adhesive application needs to be sufficiently quantitative.
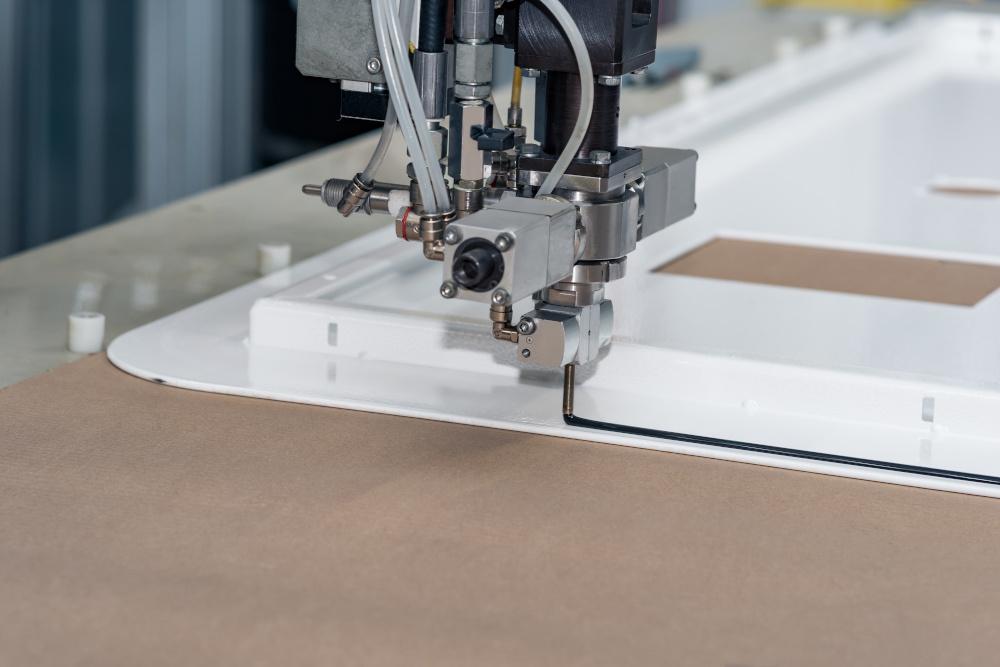
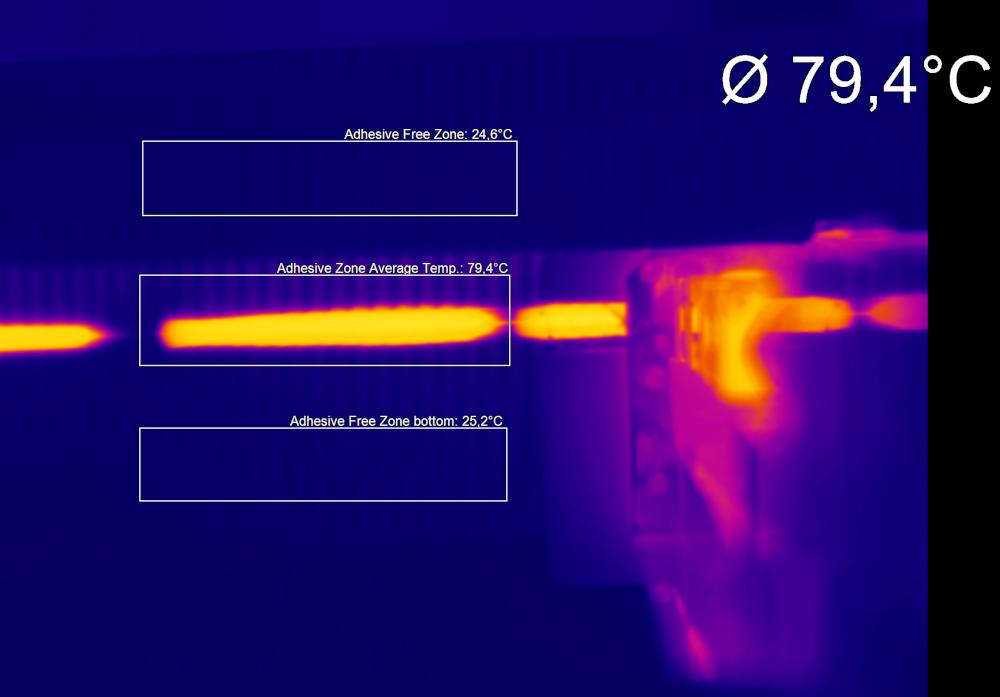
Ensuring Consistent Adhesive Application with Fixed Infrared Cameras
Thermal cameras enable continuous real-time monitoring, immediately detecting inconsistencies such as uneven application, incorrect curing, or overheating. They operate without physical contact, eliminating the risk of contamination or disruption to the adhesive application process. Infrared sensors facilitate thorough quality control by providing detailed thermal images and data.
To achieve consistent adhesive application throughout the day in this example, the best approach is to use a fixed infrared camera that observes the same area of the part at a precise moment after ejection. The size and location of the adhesive bead can be easily detected and measured with a long-wavelength infrared camera, with the quality of the adhesive application directly correlating to the area covered on the plastic part. Measuring the exact physical area of adhesive would require significant custom programming, which is unnecessary for determining adequate application.
Instead, a specific area on the part can be monitored, encompassing both the adhesive bead and the adjacent temperatures. The average temperature of all pixels in this measurement area can be used to assess the adhesive application, provided the camera captures and stores each image simultaneously after ejection, and the measurement area remains consistent. Testing has determined that an average temperature of 85 °C indicates an adequately sized bead. If the adhesive bead is smaller than acceptable, the average temperature will be lower than 85 °C, triggering an alarm.
The Event Grabber feature in PIX Connect software is utilized in this application as it will freeze an infrared image when input from a thru-beam photoelectric sensor is received by the Industrial Process Interface. A holdoff time of 1.5 seconds is set to allow ideal timing for capturing the temperature of the Adhesive zone.
The PIX Connect software can archive fully radiometric thermal images, allowing every pixel value to be measured in stored radiometric TIFF image files. The example images were captured with a PI 640i (640 x 480) using a 33° optic from 2m away, providing the detailed image quality required by the client. A mid-range resolution (320 x 240) would have been adequate for this application. Parts of varying sizes can be tested similarly by adjusting optics or working distance.
Simple Temperature-related Product Quality Solution without Custom Software Development Saves Cost
While some production solutions may require custom software programming to improve product quality, many can be implemented by simply connecting the infrared camera to a PC with PIX Connect software. This software offers numerous measurement tools that can provide maximum, minimum, or average temperatures from any shape drawn on an infrared image. The software’s triggering capabilities, which accept external inputs through the Optris Industrial Process Interface accessory, ensure precise location and timing for temperature data collection. The same interface that receives input triggers also communicates temperature or alarm information to the customer’s PLC through 0/4–20 mA or relay signals. Alarm conditions can be easily set in the Alarm tab of the PIX Connect software. Optris support is available to guide engineers in optimizing event capture, non-contact temperature measurement, and alarm features in the PIX Connect software.
Using the standard features of PIX Connect instead of custom software implementation is cost-effective, saving significant development expenses. It reduces time-to-deploy, enabling faster integration into manufacturing processes. PIX Connect’s functionalities are already thoroughly tested and proven reliable, ensuring robust performance and minimizing risks associated with untested custom solutions. This straightforward approach allows for efficient use of resources and guarantees consistent, high-quality adhesive bonding monitoring.
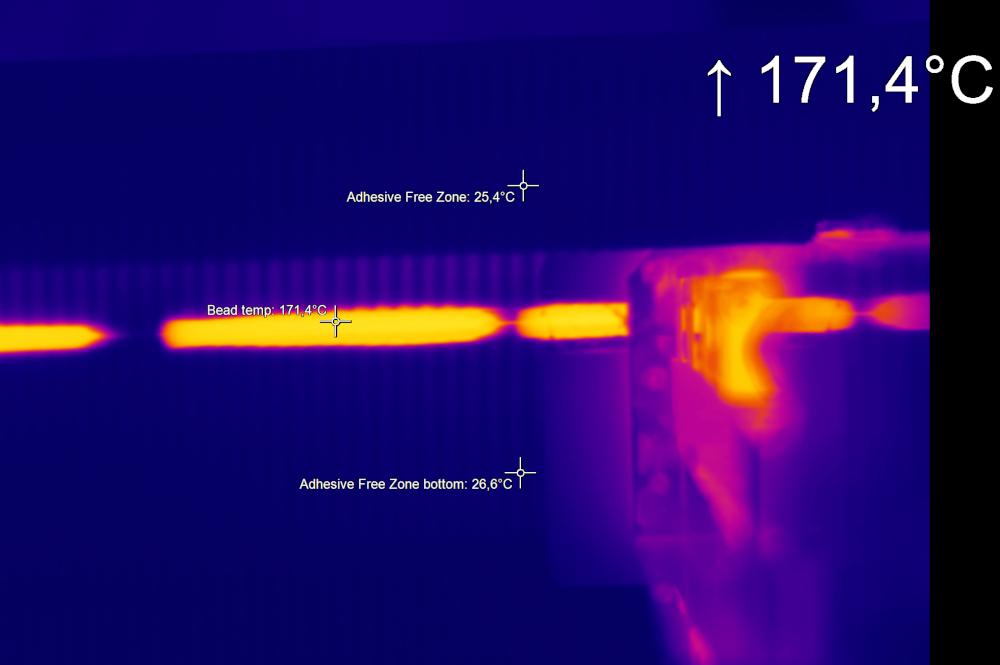
Recommended Products
Other General Manufacturing Applications
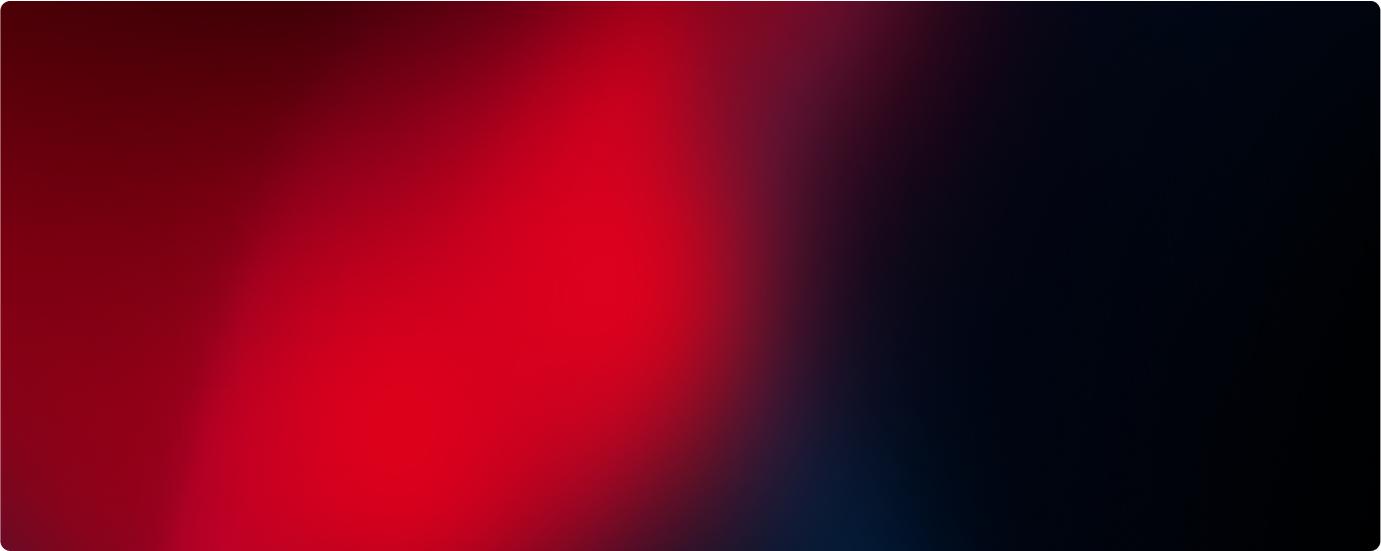
Talk to us about your IR Temperature Measurement Requirements
There are over 300 different pyrometer variants to choose from in the Optris infrared pyrometer portfolio each optimized for material, spot size, distance from the target, and environmental conditions. Fortunately, there is a trained engineer to phone or chat with to guide you through the process of choosing the perfect infrared sensor for your application.
The same support is available for the extensive IR camera product line.
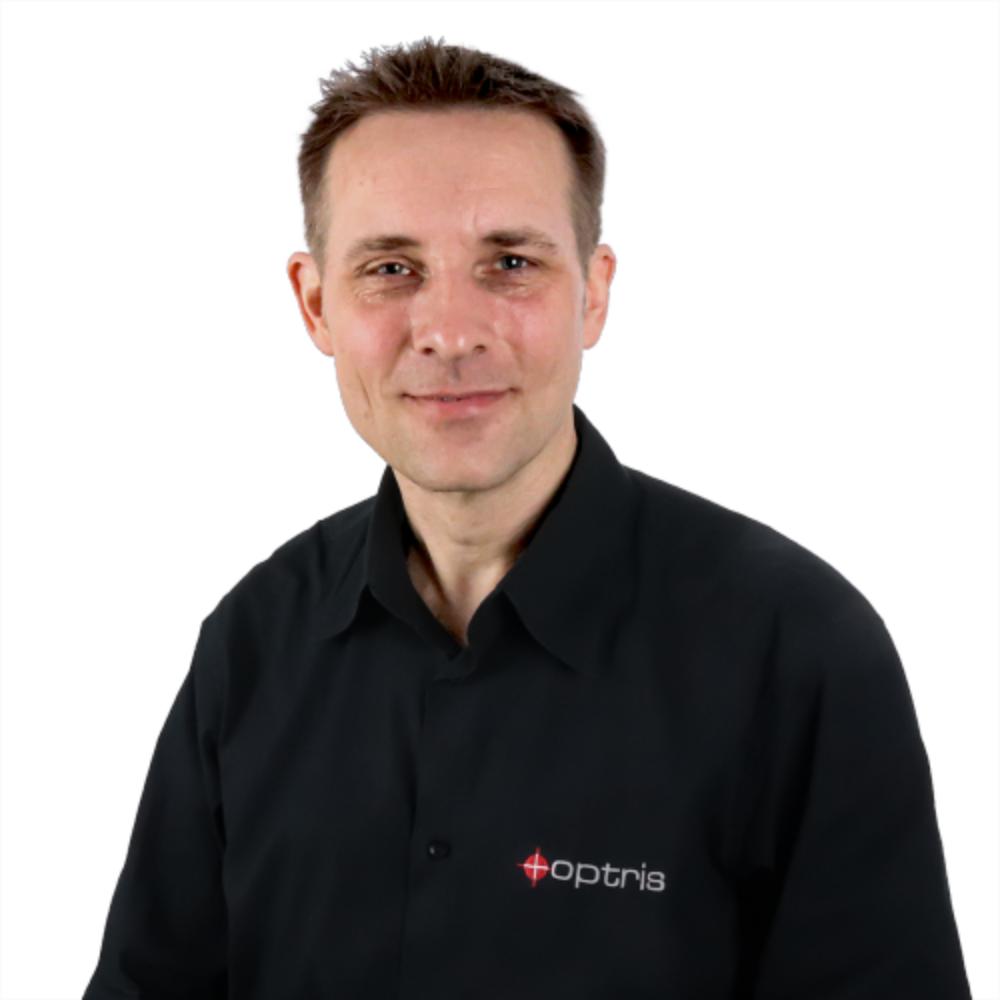