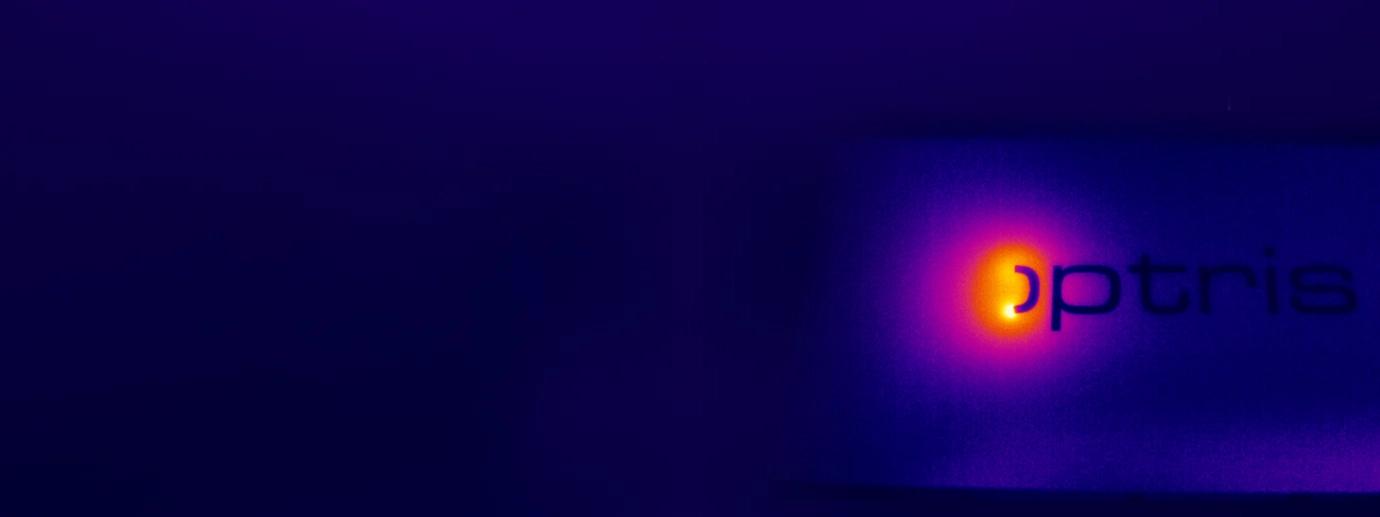
Optimizing Laser Cutting and Engraving by Measuring Heat Affected Zones with IR
Online Infrared Monitoring Optimizes Laser Processes to Ensure better Cuts and Material Integrity
Understanding the Thermal Dynamics in Laser Cutting and Laser Engraving
Laser cutting and engraving are highly precise and efficient methods for processing various materials, including metals, plastics, and ceramics. These processes utilize a concentrated beam of light, typically from a CO₂ or fiber laser, to cut through materials by melting, burning, or vaporizing them.
While laser cutting offers numerous advantages—such as high accuracy, speed, and the capability to produce complex shapes—it also introduces several thermal challenges that can impact the quality and efficiency of the operation. Laser cutters can generate extremely high temperatures, ranging over 1000°C, depending on the material, significantly affecting the processed material.
One of the major concerns in laser cutting is the formation of a Heat Affected Zone (HAZ). The intense heat from the laser beam can alter the material’s microstructure surrounding the cut, potentially leading to mechanical degradation. Research indicates that the size and severity of the HAZ are influenced by various cutting parameters, including laser power, cutting speed, and the type of assist gas used. For example, high laser power and slow cutting speeds can enlarge the HAZ, resulting in greater material distortion and reduced mechanical strength.
Temperature distribution during the laser cutting process is closely linked to the overall quality of the cut. Uneven temperature distribution can lead to issues such as dross formation, increased surface roughness, and variations in kerf width. Additionally, the high temperatures involved in laser cutting can cause thermal distortion. The rapid heating and cooling cycles can result in warping, especially in thin or highly thermally conductive materials, which affects the cut parts’ dimensional accuracy and complicates assembly processes.
The laser cutting machine’s thermal output directly influences the cut’s quality. Excessive heat can cause material deformation, melting, or charring, leading to imprecise or damaged cuts. Various factors, such as laser power, light amplification, focal spot size, plasma formation, resolution requirements, crystal properties, and even the use of inert gases, can all impact the thermal output during the cutting process.
Monitoring the thermal fingerprint of the laser process reveals new insights for optimization.
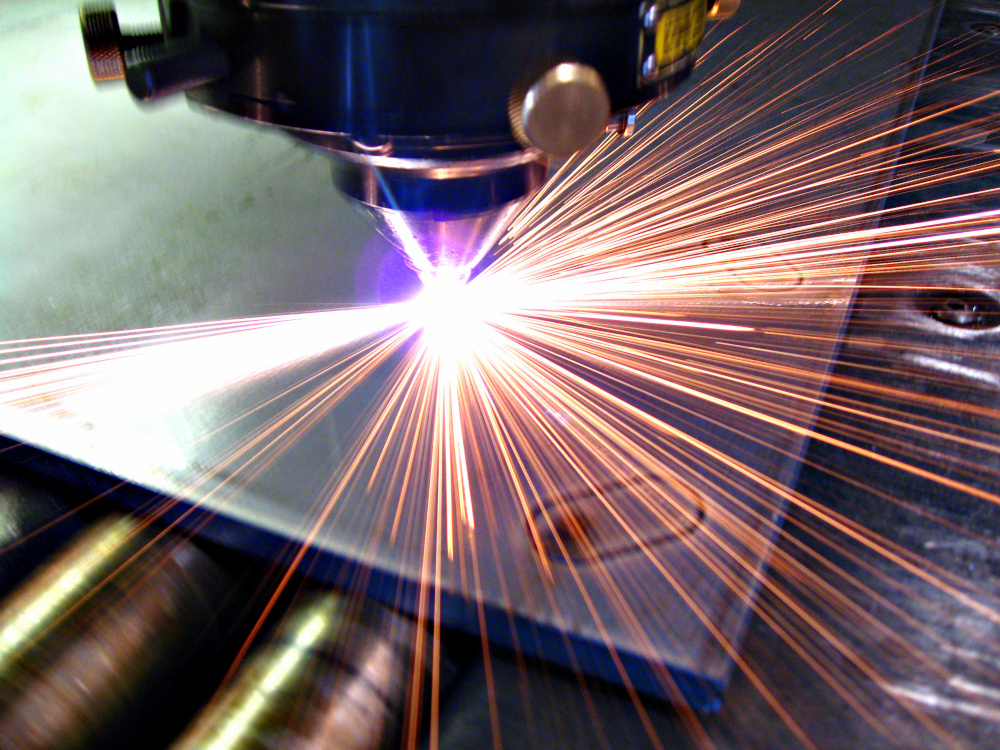
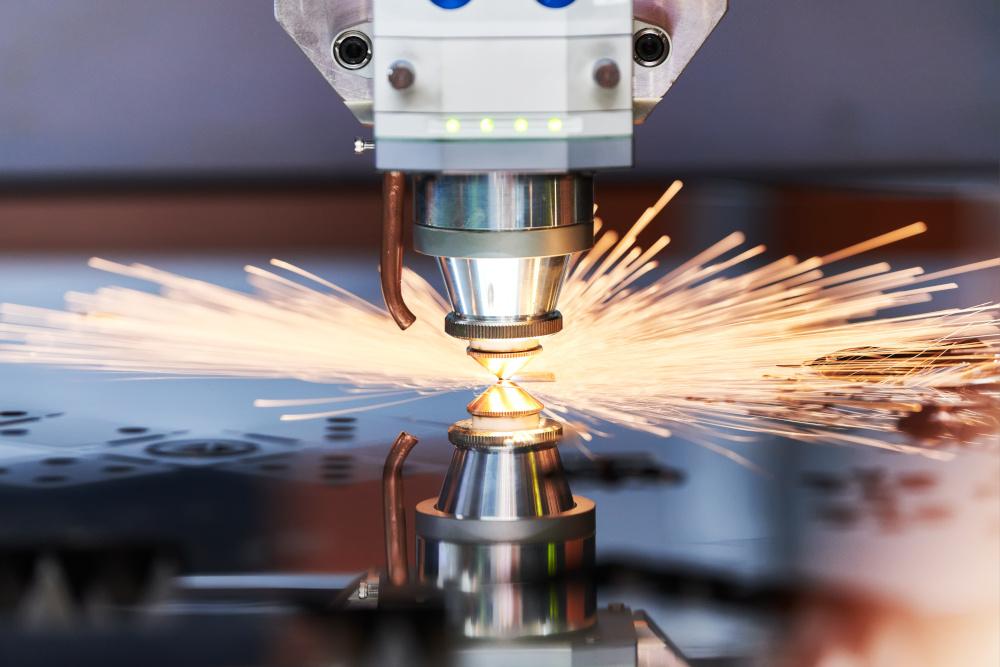
In-Situ Accurate Temperature Measurement of the Processed Material in Laser Applications
Emissivity is crucial for accurate temperature measurement and varies depending on material properties, surface quality, temperature, wavelength, measurement angle, and the measurement setup. Non-metallic surfaces generally have consistent emissivity across wavelengths but emit less radiation than ideal blackbody radiators, classifying them as gray bodies. Metallic surfaces, however, have emissivity that changes with temperature and wavelength, making them selective radiators.
For accurate metal temperature measurement, short-wave operation is recommended, as metals emit more radiation and have higher emissivity at shorter wavelengths and higher temperatures. This reduces potential measurement errors due to emissivity variations. However, this must be balanced with the laser’s interaction with the material, as absorption equals emissivity, following Kirchhoff’s law. A notch filter is necessary to block high-power laser light and prevent crosstalk that could damage the infrared camera.
When using thermal cameras for non-contact temperature measurement in laser processing, the cameras must withstand the high energy density of the laser and its reflections. Laser processes typically utilize solid-state lasers operating at 1064 nm or CO₂ lasers at 10.6 μm. Even minimal exposure to laser reflections can cause significant damage to the infrared camera. To prevent this, two strategies can be employed: using a camera that operates in a wavelength range distant from the laser’s wavelength or protecting the camera with a specialized filter. For instance, Optris offers notch filters for the PI 1M and long-pass filters for LT cameras to address this challenge.
Infrared imagers like the PI 08M provide comprehensive process insights, unlike single-point pyrometers that only measure temperature at a single point. The infrared camera’s temperature measuring range should align with the process temperatures to ensure accurate heat distribution recording. The Optris PI 08M measures at a wavelength of 800 nm and starts recording temperatures at 575°C, making it ideal for monitoring the heat distribution in metals and shiny materials processed at high temperatures. Another option is the PI 640i infrared camera, which utilizes a long-wavelength spectral range with a CO₂ filter, allowing it to measure temperature distribution starting from ambient temperatures.
Superior Quality Through Thermal Management by Integrating Infrared Thermography in Laser Applications
Utilizing infrared cameras for monitoring provides valuable thermal data that can be used to fine-tune the laser process, ensuring high-quality cuts while minimizing thermal damage. Effective management of these thermal challenges involves optimizing laser power, cutting speed, and focus to minimize the thermal impact on the material.
Real-time temperature monitoring using infrared thermography has proven highly effective in assessing and controlling cut quality. The role of infrared thermography in maintaining optimal conditions is crucial, giving manufacturers the confidence that they can prevent defects. Continuous monitoring of the temperature at the cutting front enables adjustments to process parameters, helping maintain optimal conditions and minimize defects. High-resolution thermographic cameras can detect early signs of thermal distortion, allowing for timely corrections to the cutting parameters.
Manufacturers can overcome these challenges by integrating advanced monitoring technologies with a thorough understanding of thermal dynamics, achieving superior cut quality and preserving material integrity.
Optris offers specialized infrared cameras designed for laser applications. The PI infrared imagers are easy to integrate into various systems, supporting both analog and digital outputs. In some machine integration setups, manufacturers use the PI infrared camera with a Linux computer, leveraging the SDK to develop custom software that ensures optimal process control and synchronization with other systems.
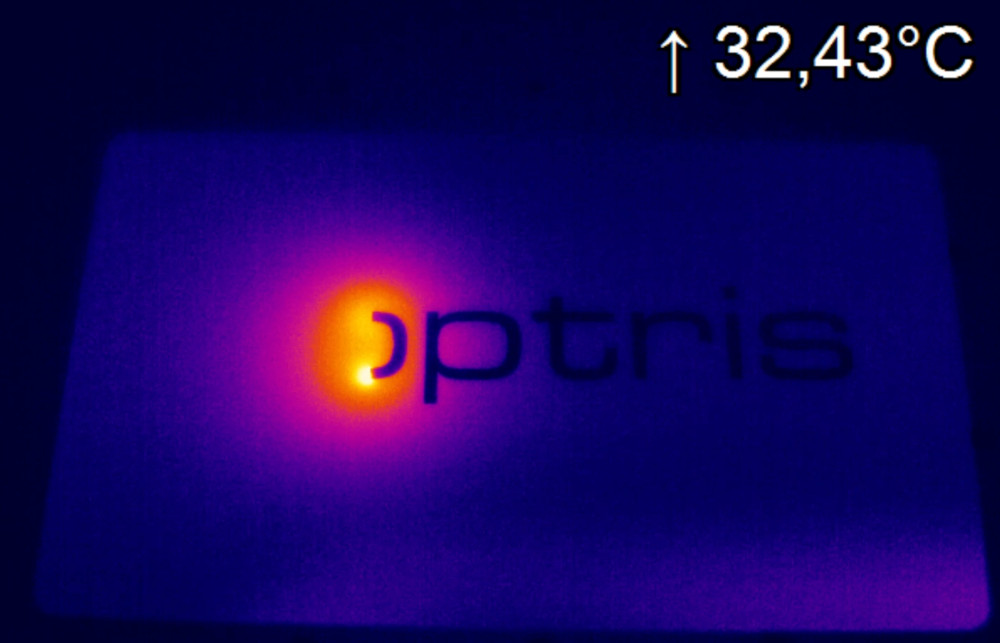
Recommended Products
Other 3D Printing & Additive Manufacturing Applications
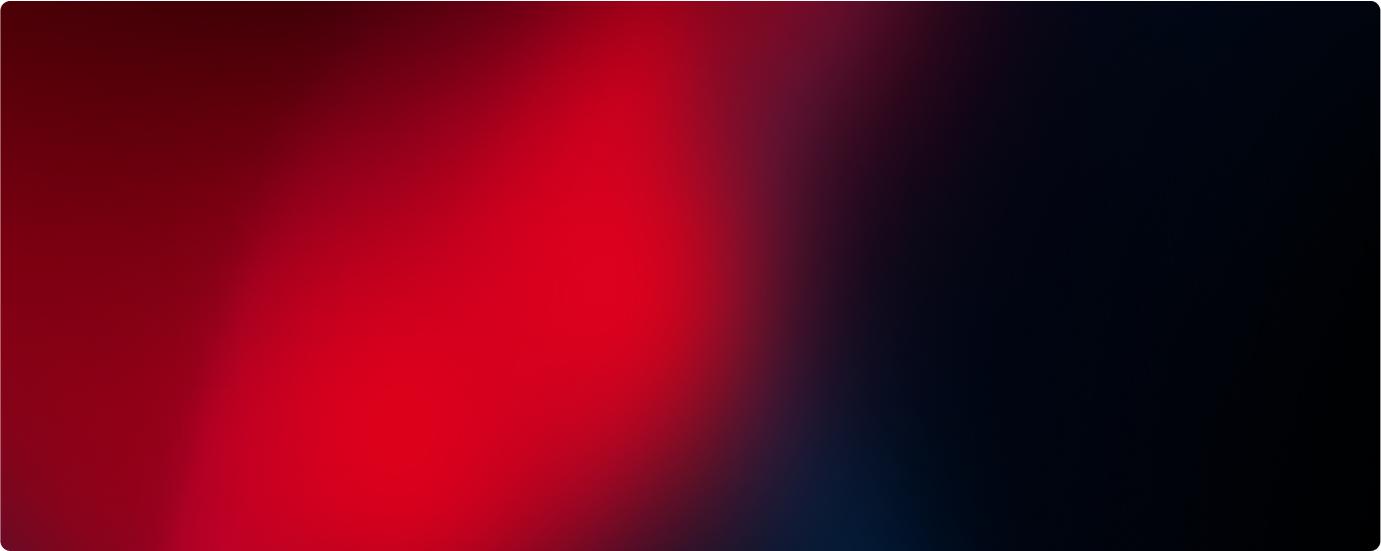
Talk to us about your IR Temperature Measurement Requirements
There are over 300 different pyrometer variants to choose from in the Optris infrared pyrometer portfolio each optimized for material, spot size, distance from the target, and environmental conditions. Fortunately, there is a trained engineer to phone or chat with to guide you through the process of choosing the perfect infrared sensor for your application.
The same support is available for the extensive IR camera product line.
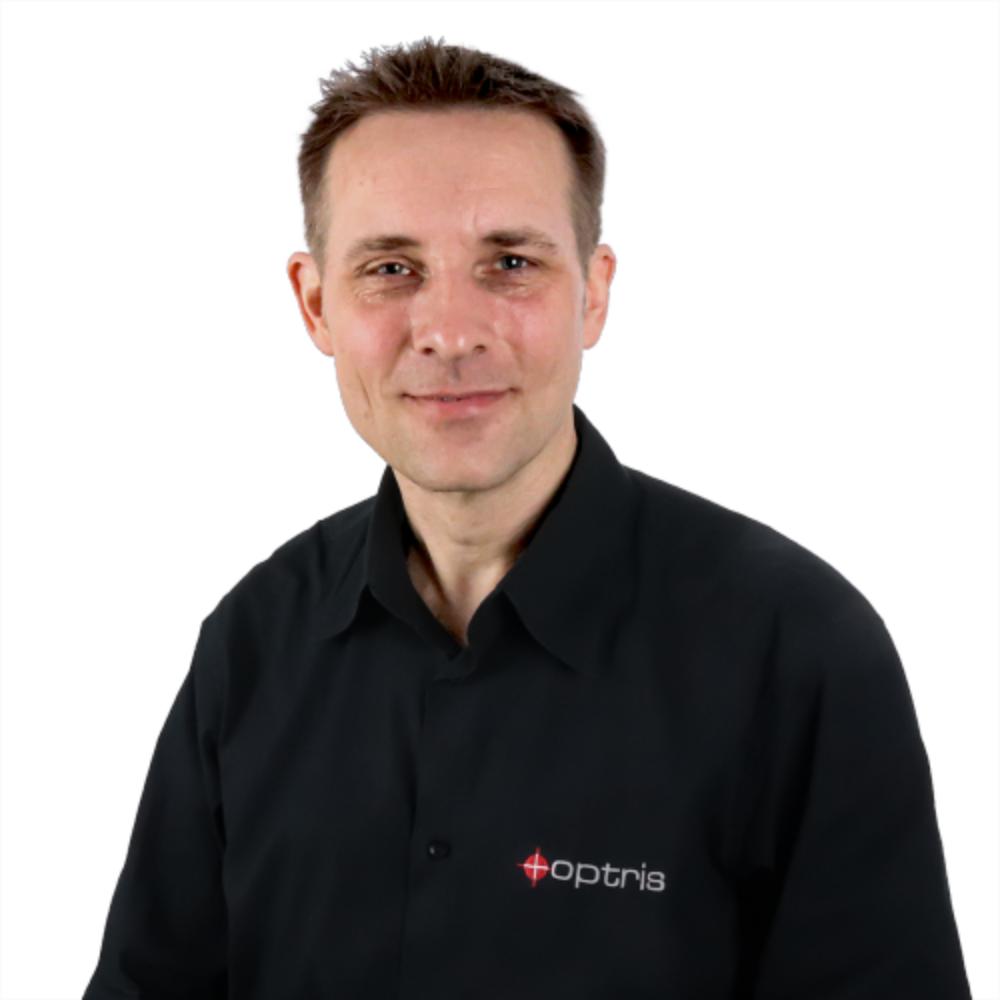